Smart work: how man and machine cooperate effectively
Use smart, rapidly evolving technologies to ensure that manufacturing companies’ scarce manpower remains effective, flexible, and sustainable. That is Smart Work. TNO puts this into practice using working environments that are replete with people-oriented technology, ranging from augmented reality, collaborative robots, and exoskeletons, to feedback sensors, big data, and artificial intelligence.
Smart Industry (a.k.a. Industry 4.0), stands for automation and for making the best possible use of digitisation. In manufacturing industry, factors such as small series and agile production processes limit the potential for automation. This is firstly because it is not always profitable, and secondly because it is not always possible. Accordingly, the human factor – the operator – continues to be a key link in the processes.
Give operators the very best support
There is no market demand for large production series, instead what is needed are small series of complex and constantly changing products.
“The customer sets high standards in terms of flexibility and quality. This requires the skilled professionals involved to be operationally agile. In addition, while one operator may be technically trained and experienced, another may be just starting out in their career. This is especially the case at times when the labour market is tight.”
Thus, operators need the very best support if they are to perform their tasks flawlessly and efficiently. New operator support technologies are available for this purpose, such as digital work instruction systems, projection technology, exoskeletons, augmented reality, and smart glasses such as the Microsoft HoloLens. The way in which this technology is set up is determined by the company’s goal and by the nature of the target group. It is also important to enhance the learning capacities of those who operate the machines, Mr Van Rhijn emphasises. “Armed with digital, step-by-step work instructions, they can successfully navigate their way through a given process, but will this knowledge sink in?”
Generating smart work instructions
Its experience in everyday practice has shown TNO that support systems really need to be adaptive. And that’s where today’s rapid developments in artificial intelligence come in handy. As a worker with little or no experience of the process involved, you will initially be given a lot of work instructions. But as you gain experience, work faster, and make fewer mistakes, you won’t want to re-read every single instruction at every single step. At that point, the system will automatically scale down its instructions, but quality control will still remain active in the background. The ability to automatically scale down to just the critical points is key to acceptance. Gu van Rhijn: “Without that, the operator would just click straight through, thinking ‘OK, no need to keep on telling me that’. Then there is the matter of actually generating the work instructions. Is there a smart way to ‘tweak’ 3D CAD models to make them automatically generate these work instructions? That would help companies to make savings in terms of the capacity required for work preparation, for example.”
Physical support by means of collaborative robots
TNO’s work in research, development, and application is focused on the manufacturing sector as a whole. Its customers range from a global player in the semiconductor industry who demands one hundred percent assurance in the manufacturing process or who has to train new operators, to employees in sheltered employment who are happy to receive longer-term support. TNO’s approach is to offer manufacturing companies both cognitive and physical support. For the purposes of cognitive support we use augmented reality and various other digital techniques. With regard to physical support for operators, our R&D focuses on cobots and their uses. Cobots, or ‘collaborative robots’, are specially designed to operate safely alongside human workers in the workplace.
Innovation in 3 steps
Any companies that are keen to see these and other technologies in operation are cordially invited to visit the Flexible Manufacturing field lab on the Brainport Industries Campus (BIC) in Eindhoven and the RoboHouse field lab in Delft. They can also make use of a demonstrator. “This enables you to explore your own process in an easily-accessible and targeted way, and to find out which technologies might be best suited to your own particular needs. In some cases that might be a projector, in others a tablet or smart glasses, such as the Microsoft HoloLens . That is step one. The second step, which takes place at the company’s premises, is a pilot project in the workplace in which the employees participate. In step three, the effects on productivity and acceptance are measured. In cooperation with the company (and operating in an independent role, as always), we use all of the available data plus a cost-benefit tool and other resources to determine what the technology can realistically deliver and what level of investment is required.
Curious what we can do for you?
Check out our projects or reach out to Gu van Rhijn.
Get inspired
Partnering for mutual progress
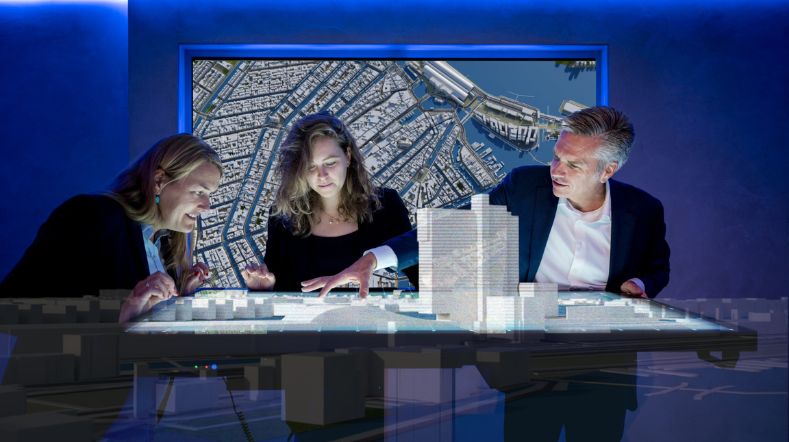
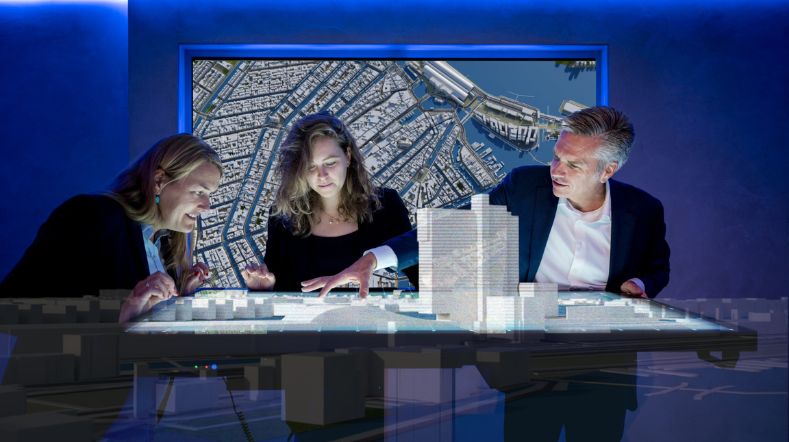
TNO spin-off Scenexus secures 1.6 million euro investment
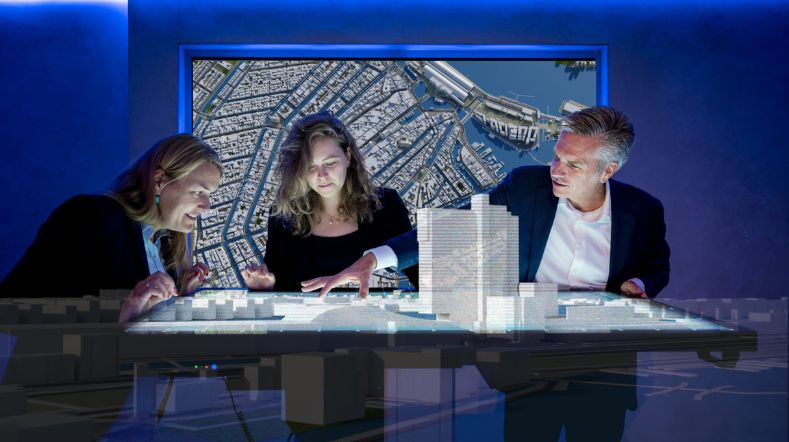
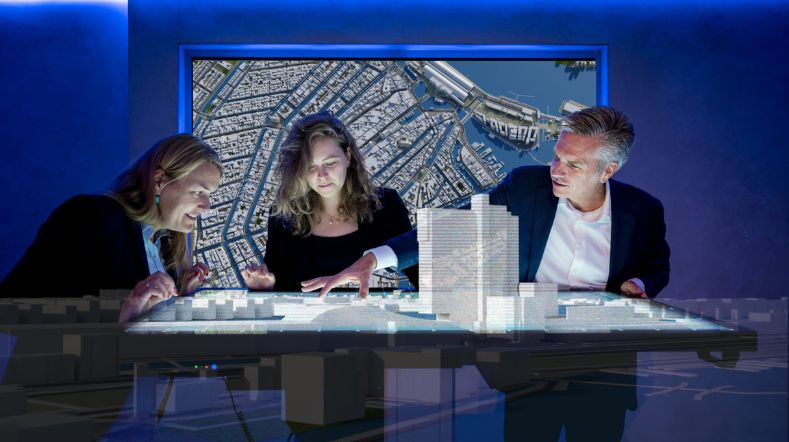
Scale up: manufacturing throughput and quality
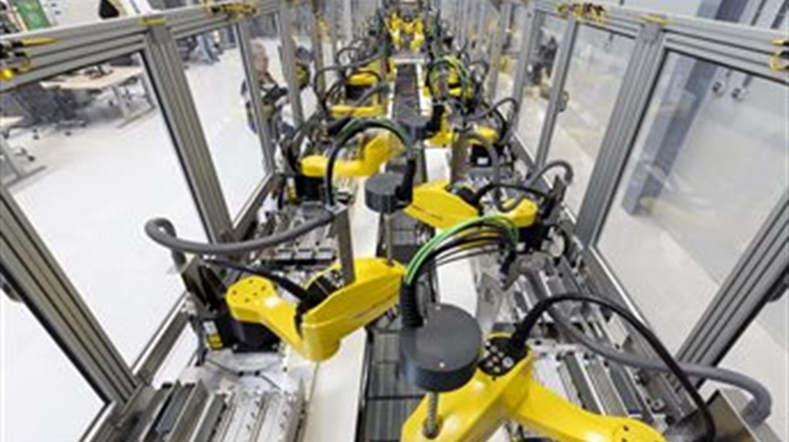
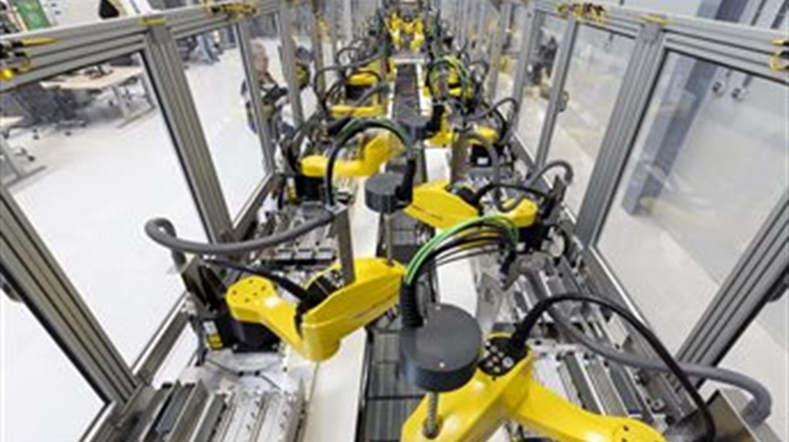
Non-destructive inspection
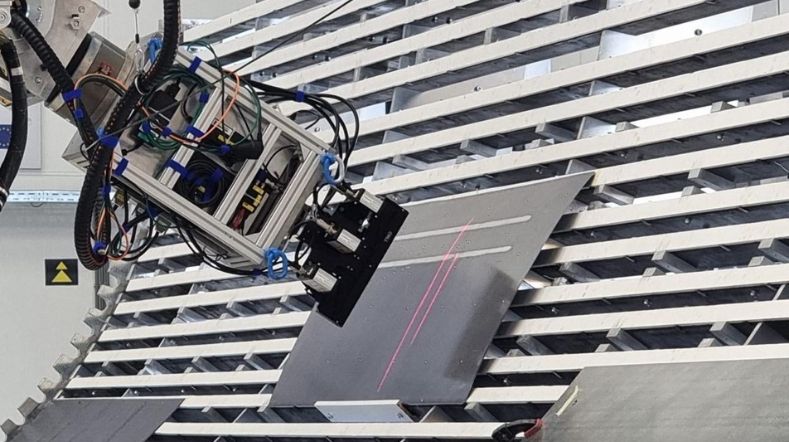
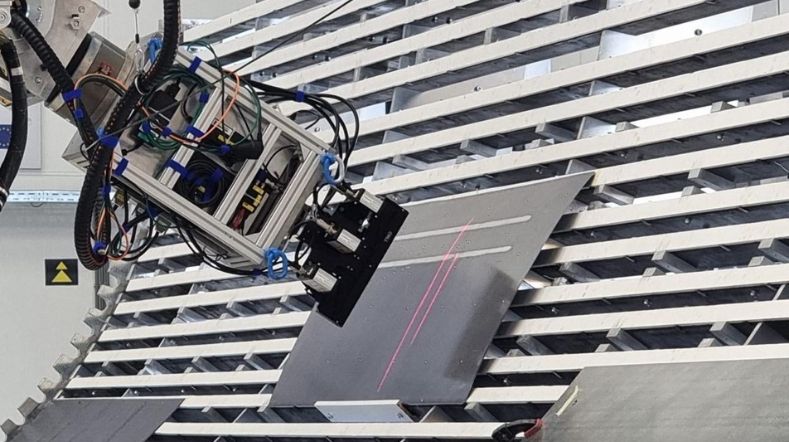
Strategic autonomy: digitalisation and value chain integration
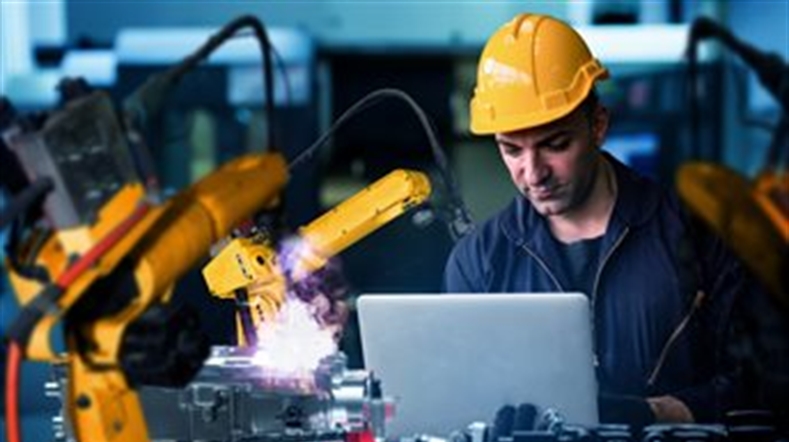
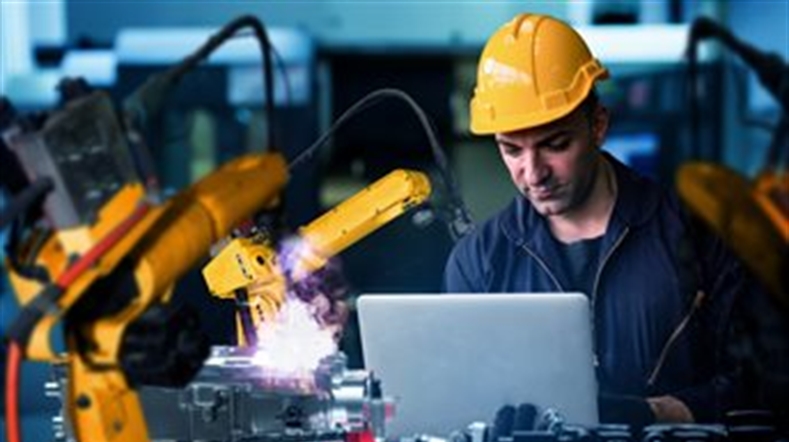