Research centre CO2-free hydrogen production
Hydrogen from renewable power sources plays a key role in the energy transition by reducing CO2 emissions related to industrial activity. Hydrogen is contributing as sustainable industry feedstock as well as energy carrier. In a test centre located in the Energy Transition Centre (EnTranCe) of Hanze University of Applied Sciences, Groningen – the so-called Hydrohub. This will take the production of green hydrogen to a higher level. Large-scale production of sustainably generated hydrogen is necessary to make the industry co2 neutral in 2030 – 2050.
The Hydrohub Innovation Program is aimed at developing largescale, electrolysis-based production of sustainable and low-cost hydrogen. Part of this program is the Hydrohub MegaWatt Test Center project for research and testing with full-scale small industrial Proton Exchange Membrane (PEM) Electrolyser and Alkaline Electrolyser (AE) units of 250 kW each.
Big steps are needed to produce green hydrogen on a large scale. One of these is to greatly improve the capacity and quality of electrolysers. Organizations can test their new equipment, electrolyser stack, components and materials in the Hydrohub MegaWatt Test Center. This state-of-the-art research facility for optimizing and upscaling electrolysis is unique in the world.
Collaboration and partners
Here, TNO brings together future hydrogen producers, the manufacturers of electrolysers and their suppliers with partners. That is special, because hydrogen producers are usually not very transparent towards the manufacturing industry that supplies them with the components. Companies that develop innovative components such as membranes or electrodes need to know how their new product performs in the manufacturer's electrolyser. In this test environment, organizations can test their innovations on an industrial scale in a controlled, realistic environment
International pioneering role
Although TNO mainly works here with the Dutch manufacturing industry, foreign companies are also welcome. In fact, there is already interest from large parties from European countries and the US. This increases the opportunities for innovative companies in our country to find new partners elsewhere and thus expand their sales market.
We are already working together with the entrepreneurial organization FME in the Elektrolyser Makersplatform NL to position Dutch companies more strongly in the electrolysis supply chain and to strengthen the competitive position of the manufacturing industry. The Netherlands can play a pioneering role internationally with this test centre.
Large scale green hydrogen
In the Netherlands, industry produces around 800,000 tonnes of hydrogen annually for use in its own production processes. This is currently achieved by converting natural gas into hydrogen and CO2 at high temperatures. By switching to the electrical production of hydrogen, industry is killing two birds with one stone: CO2 emissions and the use of natural gas are both being reduced drastically. This requires electrolysis plants that can convert water into hydrogen and oxygen cheaply and efficiently on a large scale through the help of sustainably-generated electricity.
The ultimate goal is to improve the robustness, flexibility and efficiency of large-scale production of green hydrogen through innovation and thus reduce costs in order to accelerate the energy transition. Electrolysis is an indispensable link in making our energy supply more sustainable.
A large number of parties work together in the Hydrohub MegaWatt Test Center. In addition to TNO and ISPT, these include the Hanze University of Applied Sciences, the University of Groningen, Gasunie, Shell, Nouryon, Yara and Yokogawa
Upscaling is necessary
The currently-available electrolysis plants, with a capacity of several megawatts, are far too small to supply industry with hydrogen. In order to switch completely to sustainable hydrogen, industry needs electrolysis plants with a total capacity of many gigawatts (1 gigawatt = 1000 megawatt). These plants must be relatively cheaper to procure and much smarter than the current small plants. In addition, they must be reliable and low-maintenance.
The preparations, design and construction took almost four years. The project, with TNO and ISPT as initiator, was made possible in part by the top sector Energy (TKI Energie & Industrie) and contributions from the industry. What makes the test center special is that it can test on a megawatt scale in an industrial setting. It is therefore a new step in the upscaling of electrolysis. This is badly needed to be able to produce green hydrogen on a gigawatt scale in the near future.
While experiments are carried out in TNO's Faraday lab in Petten on small surfaces (10 cm2 active cell surface) and stacks of 100 kilowatts, the test center can handle larger PEM stacks with an active surface of 2,500 cm2 for the PEM. It concerns two common electrolysis technologies: PEM, for which TNO has developed an electrolyser, and alkaline, which ISPT focuses on
Low temperature water electrolysis
TNO and partners are researching the development of Alkaline and Proton Exchange Membrane (PEM) electrolysis technology. These are the two technologies that are currently available commercially, but both still need to be significantly reduced in terms of cost in order to be applied on a large scale.
Stacks of electrolysis cells are installed in both types. For the stacks installed in the Hydrohub, it’s important that the size of the cells is representative of the size of the current commercial systems. Through an understanding of the scalability of the electrolysis process, it will soon be possible to apply the results obtained with smaller cells in the lab to the performance of large systems. This is an important step in accelerating the implementation of innovations from the lab in commercial systems.
More knowledge is available
In the electrochemical laboratory in Petten, called the ‘Faraday lab’, TNO is working (among other things) on the development of hydrogen production with the aid of PEM electrolysis. How can we use cheaper and readily available materials while at the same time increase the lifespan and efficiency of the electrolysis process?
The development is being carried out alongside Dutch suppliers of membranes and coatings, for example. It involves, for instance, using endurance tests to investigate innovative materials on a small scale, but also looks at how the manufacturing processes for electrolysers can be improved and scaled up.
Together, these aspects lead to improvements in the design of the electrolyser, which ultimately have to be applied on a representative scale. The combination of the Faraday laboratory and the Hydrohub research centre serves to ensure that more knowledge and experience will become available regarding the development and implementation of hydrogen production through water electrolysis. TNO leads the research in the field of PEM electrolysis within the Hydrohub and also provides the facilities of the Faraday lab.
CO2-free production throughout the chain
The development of affordable hydrogen production technology forms an essential step in the industrial transition to sustainable circular production, in which fossil raw materials and energy carriers make way for sustainably-produced raw materials and energy carriers.
From the optimisation of hydrogen production in the Faraday lab to the use of hydrogen in mobility and its application in the chemical industry within the VoltaChem programme, TNO is active across the entire hydrogen chain. The upscaling activities in the Hydrohub are an important link in the chain between materials research and application.
Projects
The production of hydrogen from renewable energy sources requires a dynamic operation of electrolysers. Process control plays an important role in this. Besides the construction of the Hydrohub MegaWatt Test Centre TKI Energy & Industry recently commissioned a first project.
The Hydrohub partners, including TNO, model and investigate the impact of the variable operation of the electrolyser on performance and the electricity grid. In this project TNO develops the control model. The aim is improving the overall operational efficiency of electrolysis for green hydrogen production.
Get inspired
World Hydrogen Summit 2025
Hydrogen in the energy system: The future of sustainable energy in the Netherlands and Europe
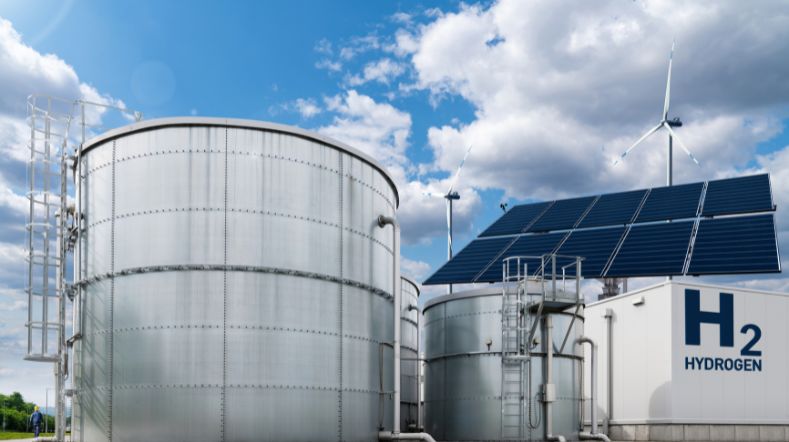
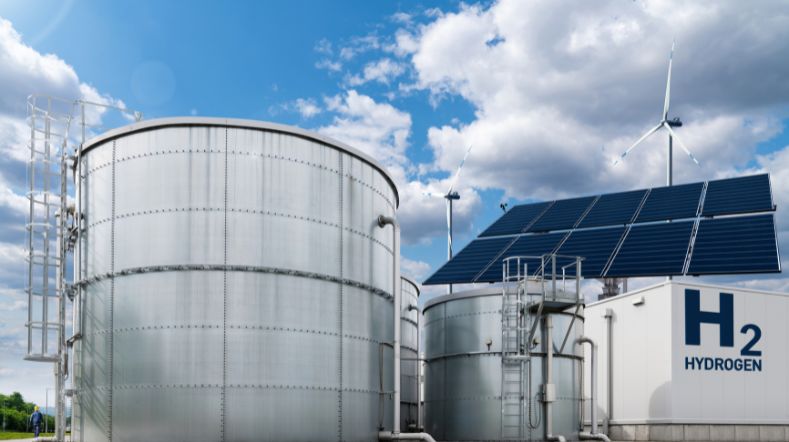
NORCE and TNO are entering into a strategic partnership on hydrogen developments
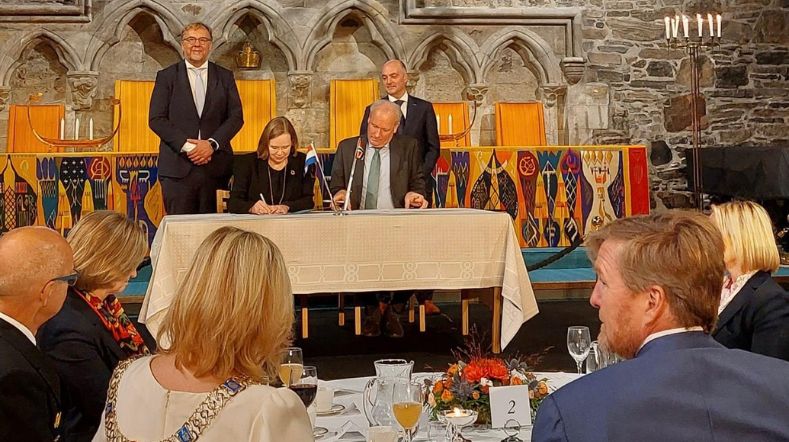
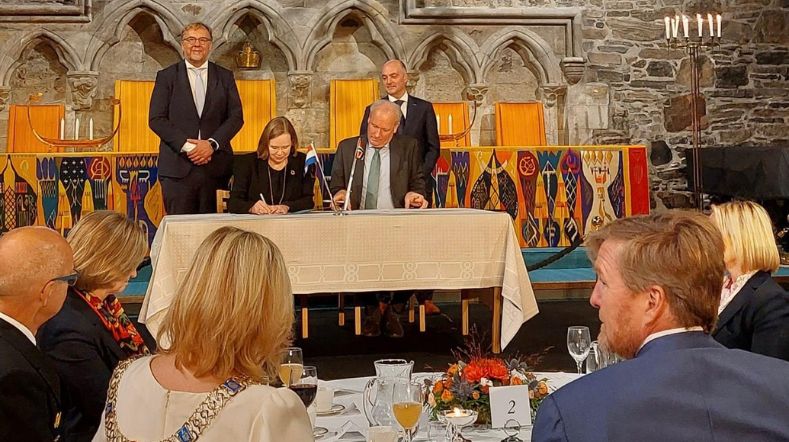
Dutch consortium participates in EU research project on large-scale hydrogen storage in depleted gas fields
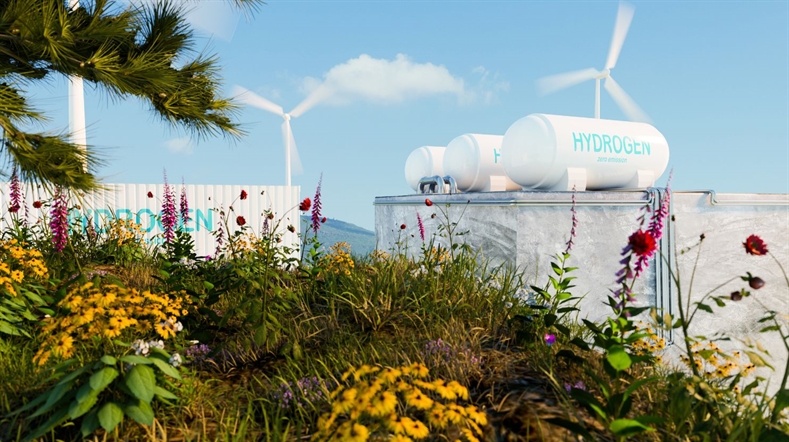
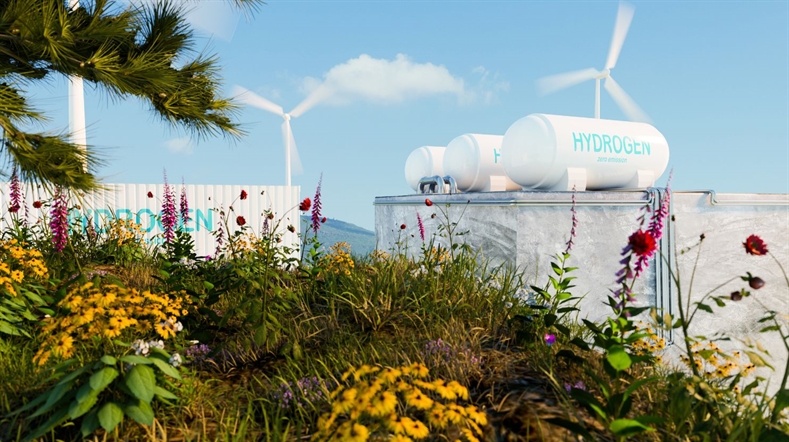
Underground hydrogen storage
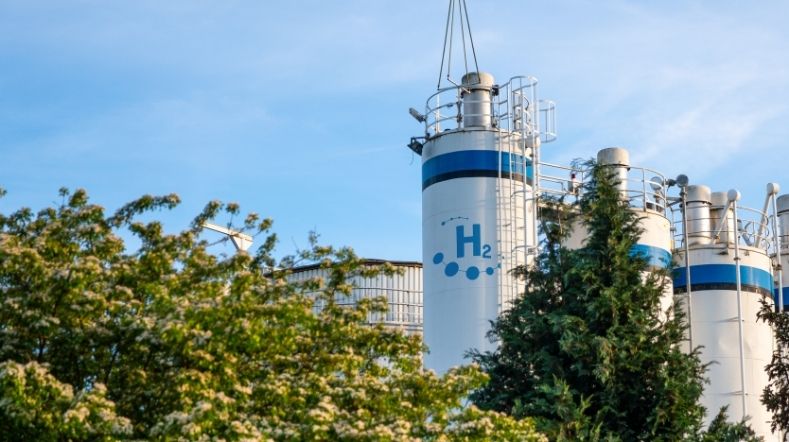
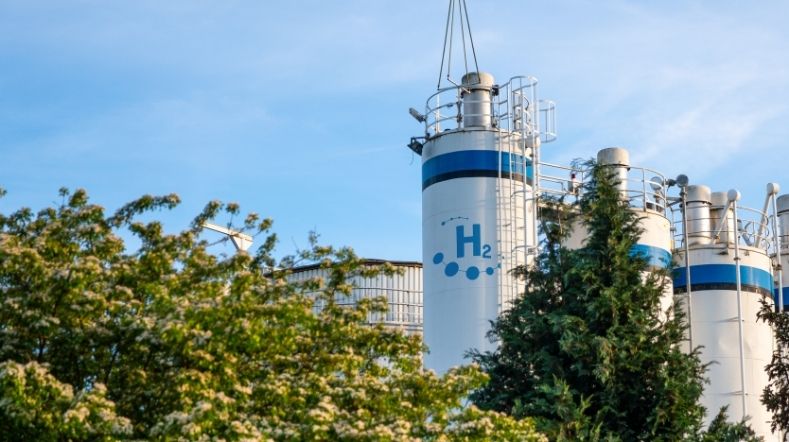