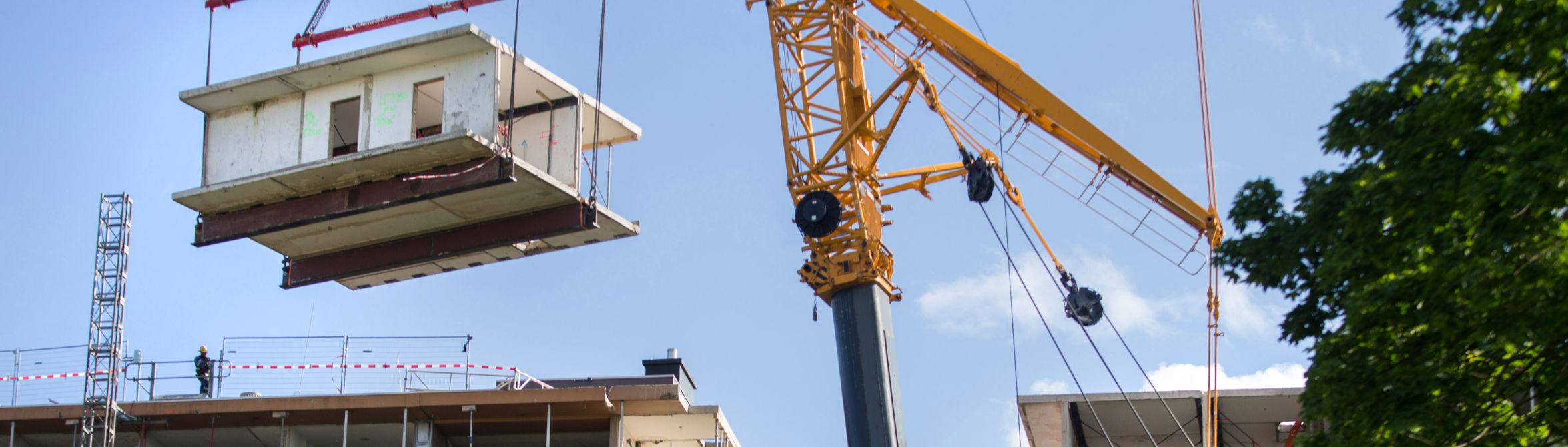
A second life for existing concrete
The production of concrete is responsible for 5 to 8 percent of global CO₂ emissions. Together with the construction industry, TNO is looking for solutions to this problem. In part 1 of this diptych, we searched for the best recipe for circular concrete. However, this solution is mainly focused on the future. What can we do right now? Time for part 2: a second life for existing concrete.
TNO advocates reusing existing concrete structures as much as possible. So too does Siska Valcke, the researcher specialising in circular concrete. “The best thing would be if you could use large concrete components as a kind of Lego block in a new building. But in the past, this sort of thing wasn’t taken into account when designing concrete structures."
"Some architects now design new structures that are easier to take apart later on. But instead of waiting for those modular concrete components to become available, it would be better to encourage the reuse of elements from structures that already exist.”
“New methodologies are needed to quantify the residual lifespan and residual capacities of reused elements”
New design rules
“We can do that by taking the quality of reusable concrete elements as a standard starting point when formulating the design rules,” adds Agnieszka Bigaj-van Vliet, the TNO expert on circular concrete structures. “This means that new methods are also needed to quantify the residual lifespan and residual capacities of reusable elements.”
Breaking down concrete
But what if the reuse of existing concrete elements turns out to be impossible? “Then we can’t avoid breaking down the concrete so that we can then reuse the sand, gravel and a small part of the cement as a secondary raw material when making new concrete,” says Valcke.
Cement recovery
Cement is responsible for no less than 90 percent of the total CO₂ emissions from concrete. Concrete may still contain cement particles that have not yet undergone a reaction. At the end of the lifespan of a concrete structure, you can remove those specific cement particles from the concrete with a special machine and then reuse them as a binding agent. This is already being tested in large-scale practical trials. Although this is a good development, only small percentages of unrefined cement can be recovered in this way. In terms of volume and CO₂ reductions, this is therefore not a complete solution to the problem.
“It’s important that it also becomes legally possible to make new concrete using large quantities of recycled materials”
Restrictions
The reuse of sand and gravel is a simpler story. “Every year, more than 20 million tonnes of stony construction and demolition waste become available, 12 million tonnes of which is concrete rubble,” says Valcke. “On paper, this is already a large part of the material needed for the more than 30 million tonnes of concrete structures that are built every year. However, it’s important that it becomes legally possible to make new concrete with large quantities of recycled materials. At the moment, there are still restrictions on this.”
Read part 1: Searching for the best recipe for circular concrete
Want to know more about TNO's initiatives in the field of circular concrete? Please contact Jeroen Kruithof.
Get inspired
Carbyon: the TNO spin-off innovating in CO2 filtration technology
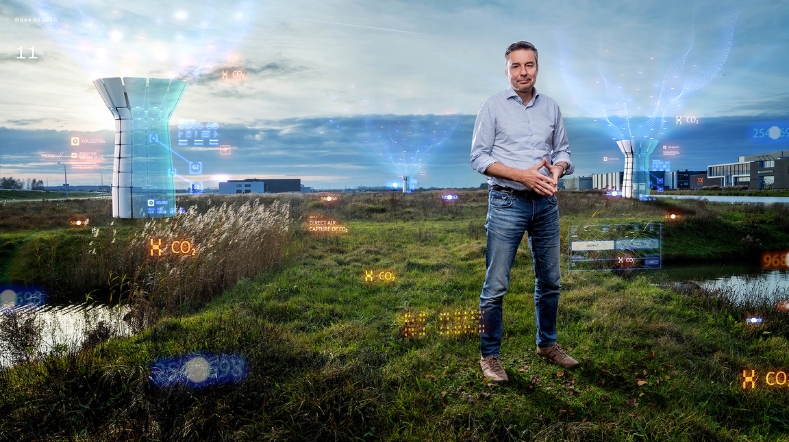
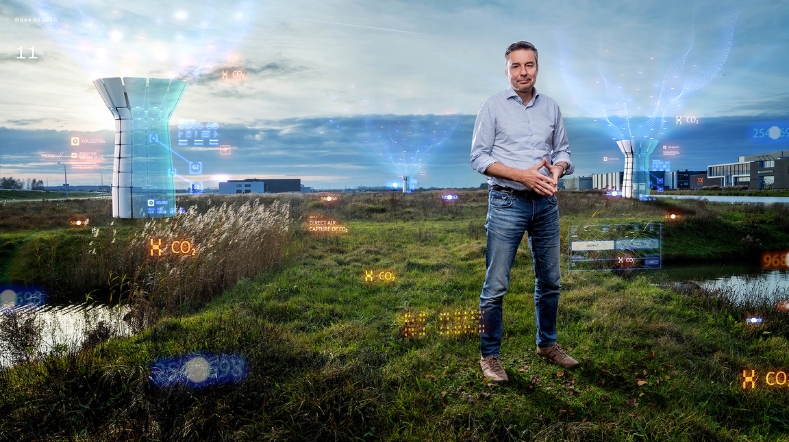
TNO’s next generation biorefinery accelerates material transition
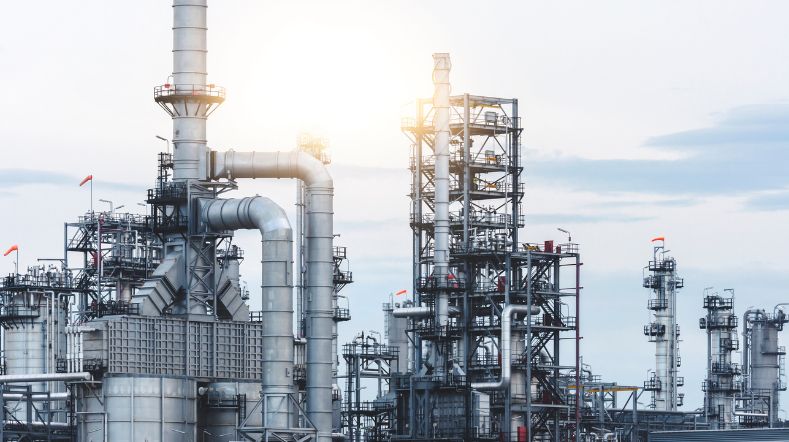
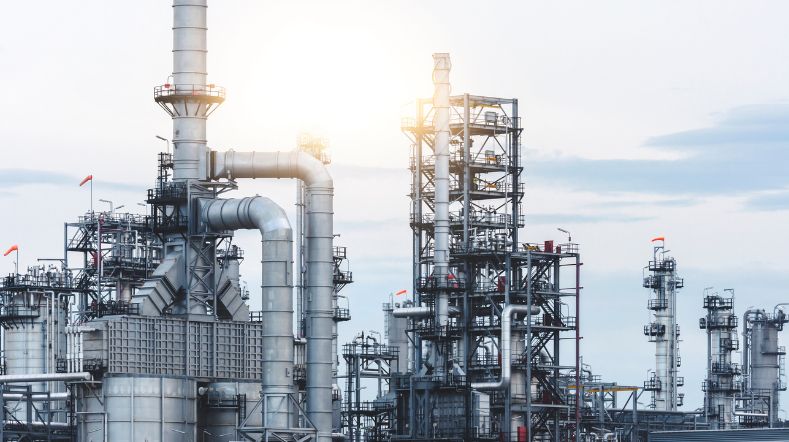
Local, circular, and biobased: towards the textile industry of the future with HEREWEAR
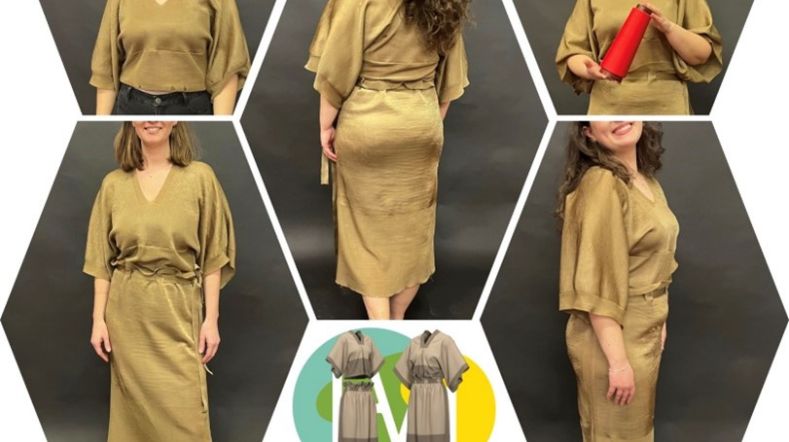
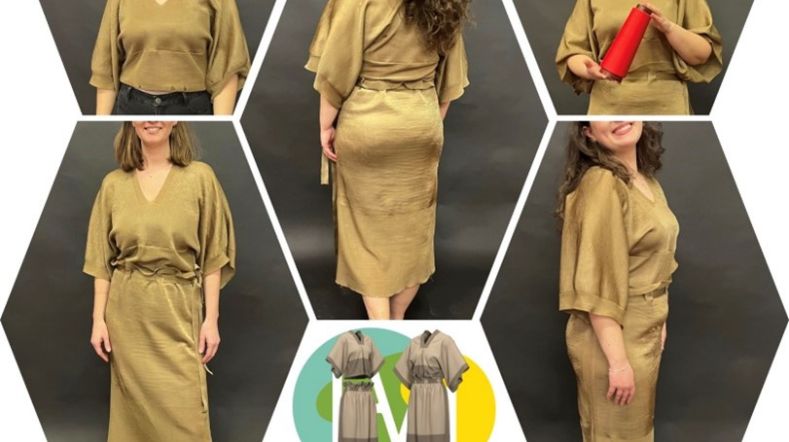
Hydrogen in the energy system: The future of sustainable energy in the Netherlands and Europe
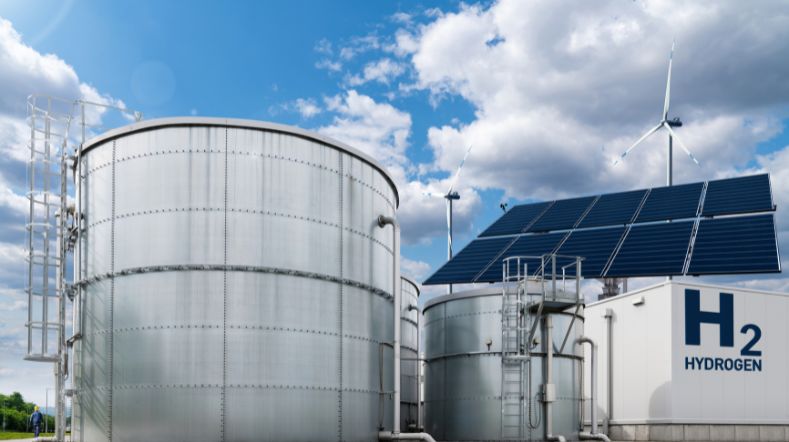
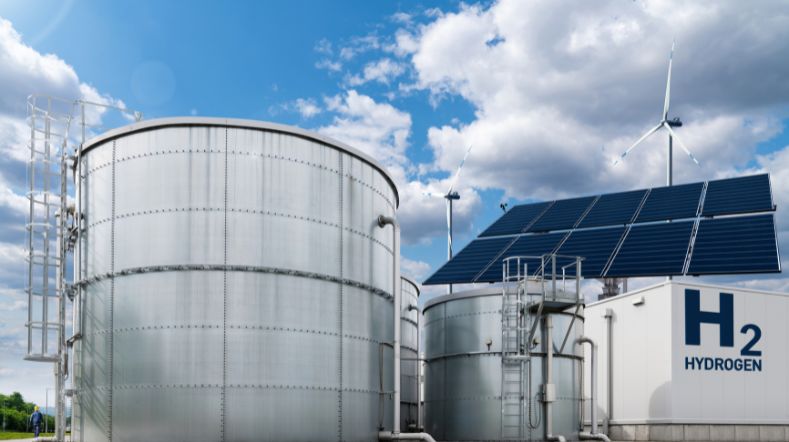
Three breakthrough technologies in drying and dewatering help industry produce clean and sustainable products
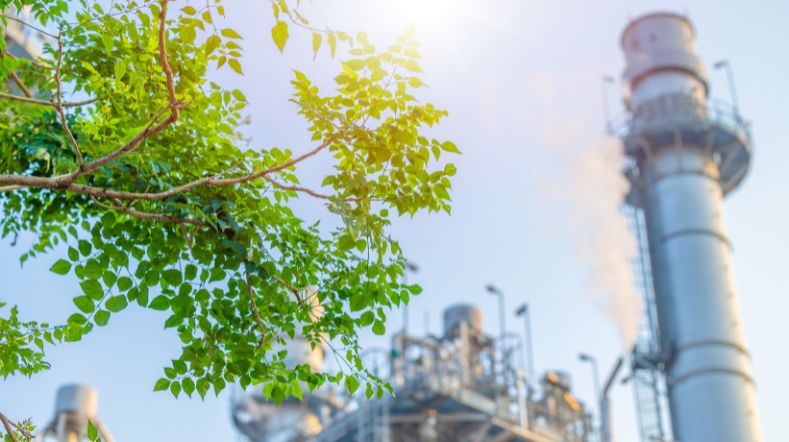
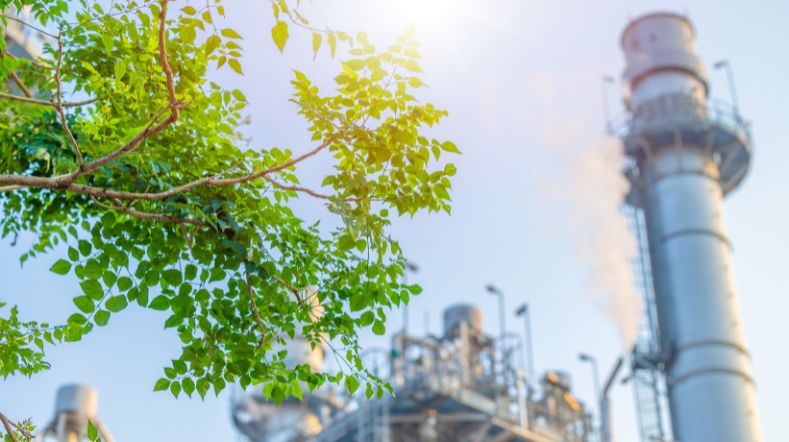