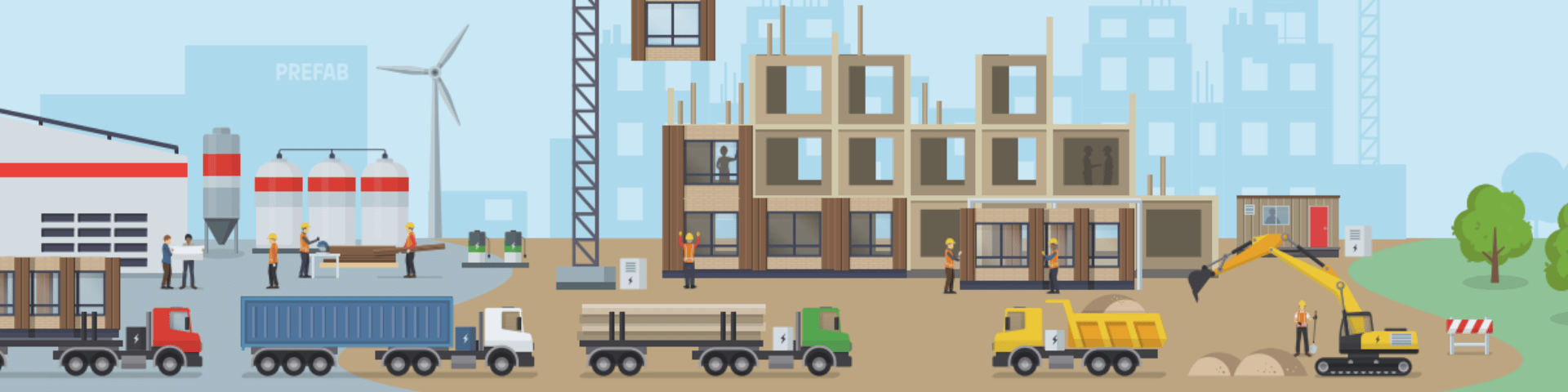
TNO nitrogen approach a blueprint for all sustainability challenges
The nitrogen crisis, combined with the growing housing shortage, poses a huge challenge to the Dutch construction industry. ‘Only by building and thinking in a radically different way, and collaborating more closely within the chain, will we be able to get construction moving again.’ An interview with Mario de Rooij, Principal Project Manager at TNO, on the future of zero-emission construction and the role that industrial prefabrication can play in it.
The Netherlands is facing a series of major challenges in which construction plays a central role. The tight housing market is giving rise to a substantial housebuilding challenge: almost one million additional homes are needed by 2030. At the same time, the energy transition requires us to make the existing housing stock more sustainable and expand and modernise our energy infrastructure.
A major obstacle to achieving these ambitions are nitrogen emissions, which are approaching or already exceeding limits in many parts of the Netherlands. To protect biodiversity, the brakes are being put on hard: emission permits are being withheld or revoked, and countless construction projects are being delayed or scrapped.
60% nitrogen reduction
To turn the tide, nitrogen emissions need to be reduced dramatically. The target for 2030 is a 60% reduction in nitrogen compared to 2018, a 0.4 megatonne reduction in CO2 compared to 1990, and a 75% reduction in particulate matter emissions compared to 2016. But how can this be achieved? Policymakers and the construction industry hope to find answers together within the Zero-Emission Construction knowledge and innovation programme, for which the government has allocated 50 million euros up to the end of 2023.
This programme, launched in 2021 by the Construction and Technology Innovation Centre (Bouw en Techniek Innovatiecentrum (BTIC), now known as TKI Bouw en Techniek), consists of seven sub-programmes. Each one is addressing a clear research question. For example, methods are being worked on that will provide more insight into the emissions of sub-segments in construction. The use of low- and zero-emission construction equipment and the application of smart construction logistics are also being explored.
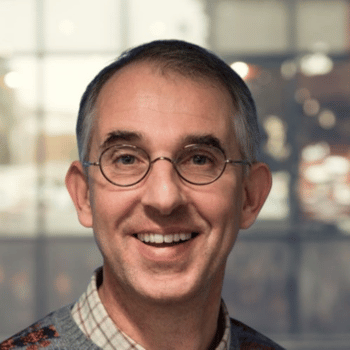
'Industrialised prefabricated construction in a factory not only allows you to build faster, but you also automatically reduce nitrogen emissions on site.'
Extensive network
This magazine focuses on the results of sub-programme 4: Industrial Modular Prefabrication (IMP), of which TNO is the lead partner. Mario de Rooij, Principal Project Manager at TNO and manager of the sub-programme, acknowledges that this is a new role for the organisation.
‘Taking the lead in a government programme is indeed something new for us, but there is growing enthusiasm about it within TNO. The main value we can add is our extensive network, which allows us to connect all kinds of parties from different disciplines. We know our way around public authorities, as well as the construction industry and other knowledge institutions. Managing programmes of this kind also gives us the opportunity to make adjustments to policy and research in the Netherlands. Policymakers can also see these benefits and have since submitted two new requests to us to head up programmes.’
No time to lose
Both protecting nature and speeding up construction require swift action. ‘We need to move from the current figure of 75,000 towards 100,000 new homes a year’, says Mario de Rooij. ‘At the same time, there is a shortage of construction workers. For that reason, we have transformed the BTIC’s original ambition, which was solely to reduce nitrogen emissions, into the industrialisation of construction. After all, industrialised prefabricated construction in a factory not only allows you to build faster, but you also automatically reduce nitrogen emissions on site.’
To save time and achieve quicker results, TNO also applied an innovative approach to this sub-programme. ‘Several projects were running in parallel and the outcomes were largely unclear. For the 21 sub-projects we launched together with around 120 partners, we therefore chose to work together in an adaptive consortium, based on a programme with broad outlines of goals and results. This adaptive format made it possible for us to evaluate the research proposals every quarter and adjust them if necessary.’
Level playing field
Until recently, nitrogen was not an issue in construction, a sector that already has to deal with all kinds of environmental standards. ‘When we started Zero-Emission Construction two and a half years ago, none of the partners could actually say how much nitrogen they were emitting,’ recalls De Rooij.
‘This was mainly because there were no uniform measurement methods or reporting procedures for nitrogen. Thanks in part to this programme, there is now increasing clarity in this area. Together with the ministries, we are working to level the playing field.’ Meanwhile, De Rooij has noticed that there is much more awareness about nitrogen in construction. ‘But perhaps more importantly, the realisation has dawned that we need to start working together in a very different way. To build with zero emissions, you need the whole chain.’
Prefabrication as an overall concept
Collaborating more intensively in this way is essential if industrial prefabricated construction is to be widely adopted, as a way of dramatically reducing nitrogen emissions on the construction site. ‘One of the main trends I have noticed in the sub-projects is that prefabricated construction is increasingly being seen as an overall concept, rather than as something that is just for carcass construction. It is being considered for everything from 2D or 3D façade elements through to complete housing modules in which all installations have been integrated.’
This way of building requires a detailed design phase, in which material use, the production process, and transport to the construction site are carefully considered in advance. ‘How do I design a wet room in which all the pipework is already installed and that can be manufactured and transported as efficiently as possible? You can only do this if you are already working with very small tolerances in the design phase. On the construction site there will be hardly any room to fix mistakes.’
Homes straight off the production line
Production sites are becoming increasingly automated and robotic, taking the automotive industry’s high-tech production lines as a template. Whether they will reach the same level of sophistication remains to be seen. ‘At the moment you will still often see a carpenter, who would normally be on the construction site, doing the very same work in a production hall.’
But there is also a different way of doing things, according to De Rooij, who cites an inspiring example from one of the sub-projects. ‘A number of educational institutions have looked into the automated production of wooden joints, as a sustainable alternative to heavy steel or concrete joints in prefabricated buildings. Based on their experience in the area of restorations, they studied old timber construction techniques. They then started thinking about how to automate production of these traditional joints, so they could be made using a CNC milling machine. This has resulted in a series of nice alternatives.’
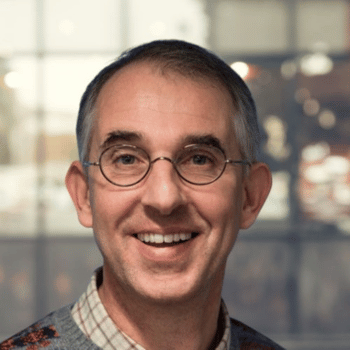
'You can calculate emissions for transport to and from the construction site for different vehicle categories, from heavy machinery through to passenger vehicles. You can also see the impact of a construction hub.'
Which requirements take precedence?
A major additional advantage of such a standardised and digitalised production process is the possibility of calculating emissions in advance. ‘Several sub-projects are working with dashboards’, De Rooij notes. ‘With these, you can immediately see the impact that design or material choices, for example, have on nitrogen emissions. This really was new territory for most of the parties.’ At the same time, these freshly acquired insights also throw up new questions.
‘One question many partners come up against is which parameters they should optimise for. Besides nitrogen requirements, the government also sets BENG (nearly energy-neutral building) requirements for building use and MPG (environmental performance of buildings) requirements for the construction itself, for example. These requirements are all different. This leads to discussions such as: which is more harmful, a few weeks of extra emissions during construction or 30 years of higher emissions when the house is being used? The question is whether we could bring all these requirements together a little more. Thanks to this programme format, we can quickly feed these kinds of practical dilemmas back to policymakers. So a lot more thought is being given to such issues now.’
Model calculations with calculation tool
Besides the construction process, construction logistics is also an important part of this sub-programme. ‘Nitrogen emissions are mainly caused by things with an engine’, explains Mario de Rooij.
‘In addition to construction equipment, transport to and from the construction site is therefore a key focus area. The market has hardly any knowledge of the impact that construction logistics has on nitrogen emissions. Due to its complexity, the programme board decided to assign this topic to TNO as an additional research question.’
Based on previous studies on emissions in logistics, TNO developed a calculation tool so that model calculations could be performed for nitrogen, particulate matter, and CO2 for the entire construction process.
De Rooij: ‘You can calculate emissions for transport to and from the construction site for different vehicle categories, from heavy machinery through to passenger vehicles. You can also see the impact of a construction hub. What’s more, the tool allows you to see exactly what the emissions are of the equipment on your construction site. In the future, we plan to expand the tool with additional features, by also incorporating the construction process, for example. Our main aim with this initial version is to start a dialogue between policymakers and the construction industry.’
The next steps
Now that sub-programme 4 has been completed, it is time to look ahead. What are the next steps? 'As far as Zero-Emission Construction is concerned, the Ministry of the Interior and Kingdom Relations is planning a follow-up, which will run from 2024 to 2026. Looking further into the future, say in five years’ time, my hope is that factory-built prefabrication will have become much more the norm. I also hope that we will have nitrogen emissions under control, and that we will be using this programme-based approach as a blueprint for other sustainability challenges. For instance, we are already turning our attention, together with policymakers, to the Water Framework Directive, which sets targets for 2027 and where we are also coming up against limits.'
'Hopefully, we will also start dealing with permits in a different way, taking actual emissions as a starting point. Reliable field measurements will be needed for enforcement. Finally, I want to stress that we are doing all this primarily with the aim of restoring nature. There is, of course, a strong basic need to keep building. But building a healthy future for the Netherlands is every bit as important. And we really need nature to make that a reality.'
Get inspired
Industrial and conceptual construction
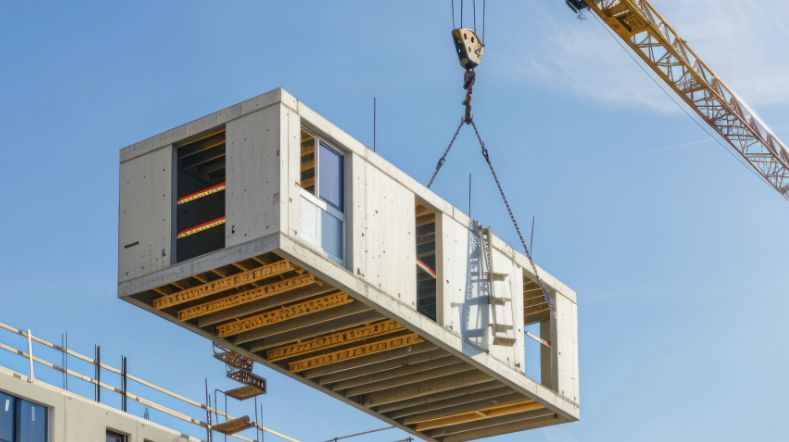
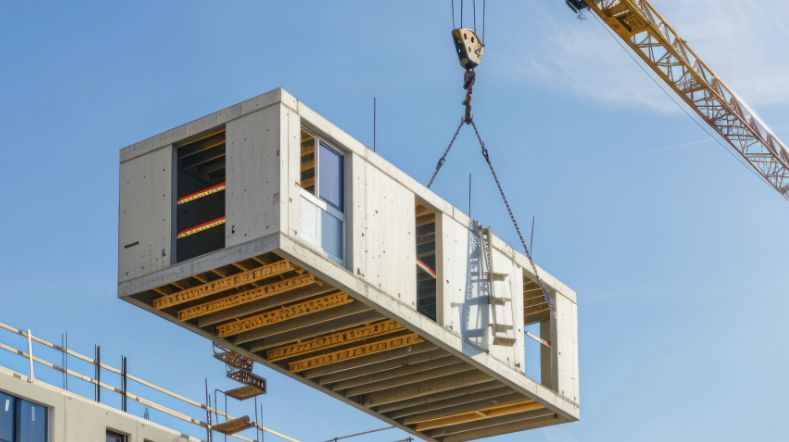
Reliable Structures
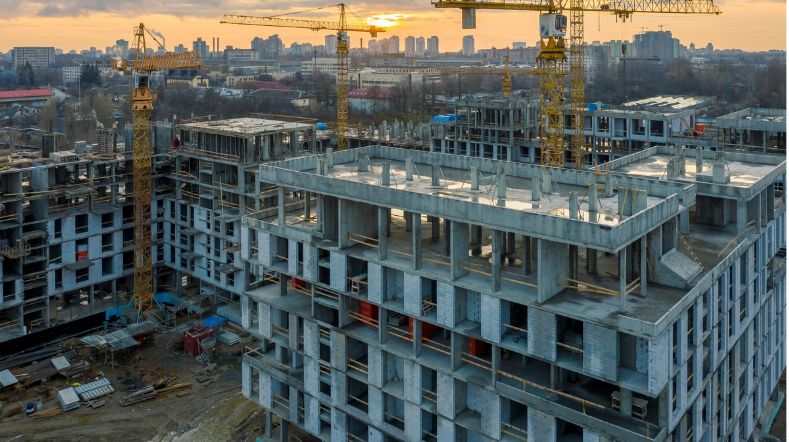
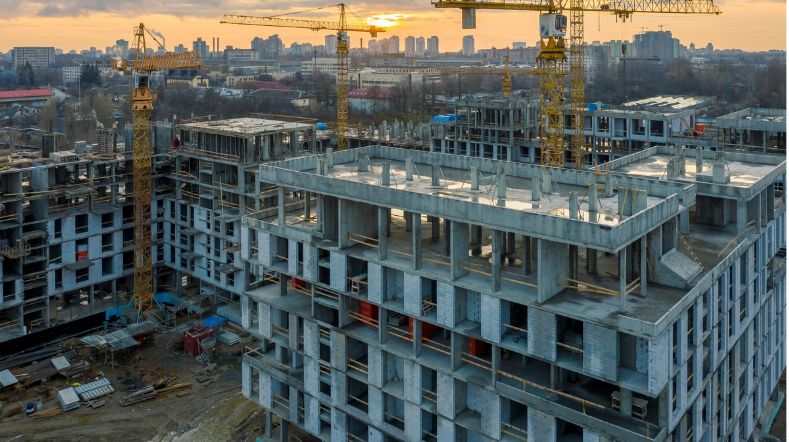
Building materials
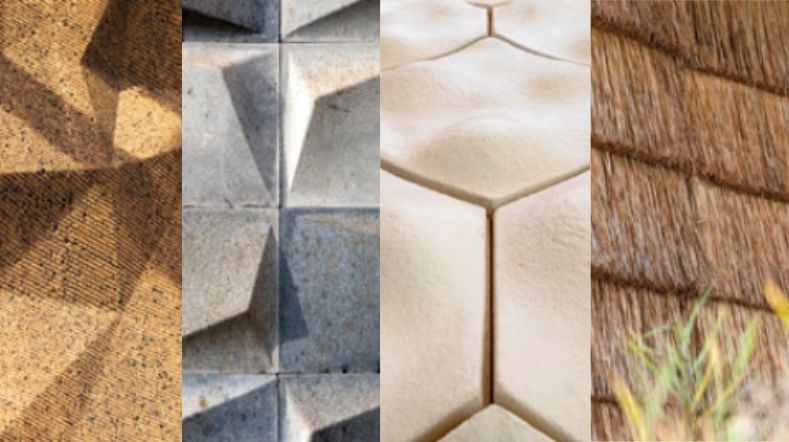
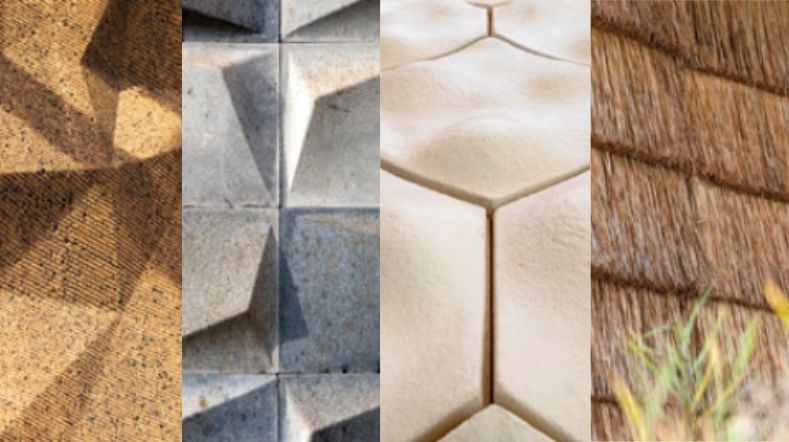
Building Materials and Structures
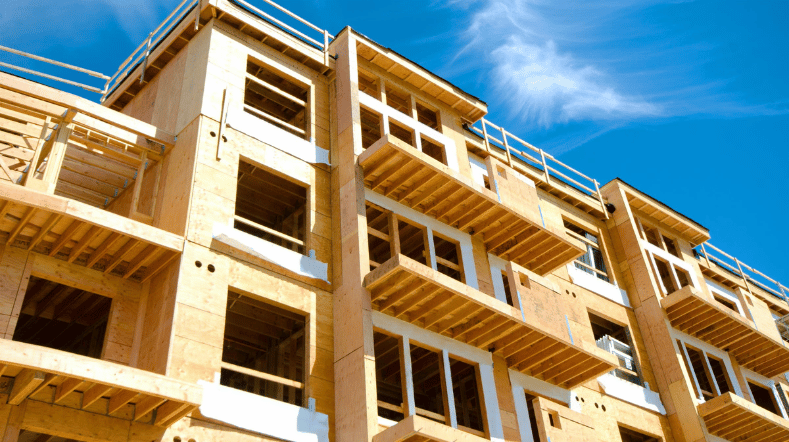
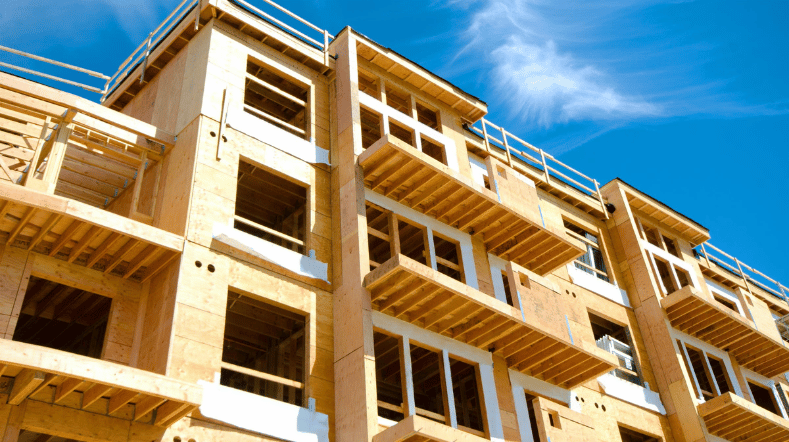
Western North Brabant becomes hotspot for biobased building blocks for the construction industry
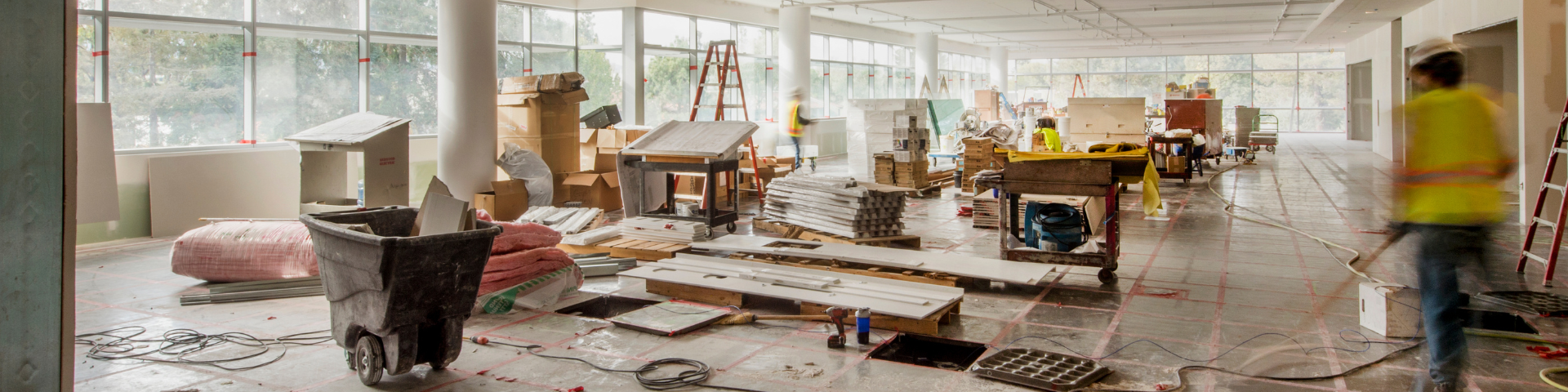
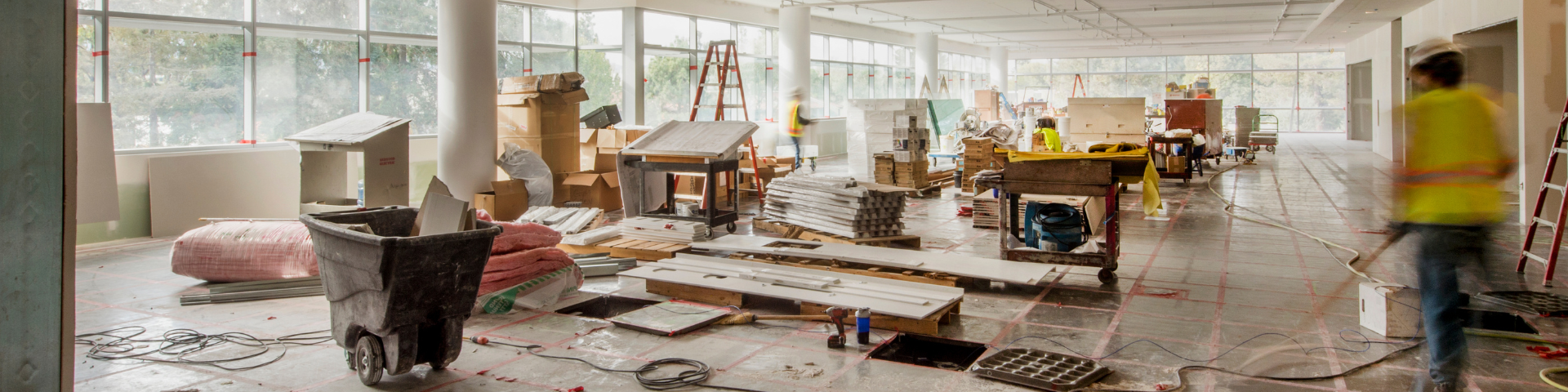