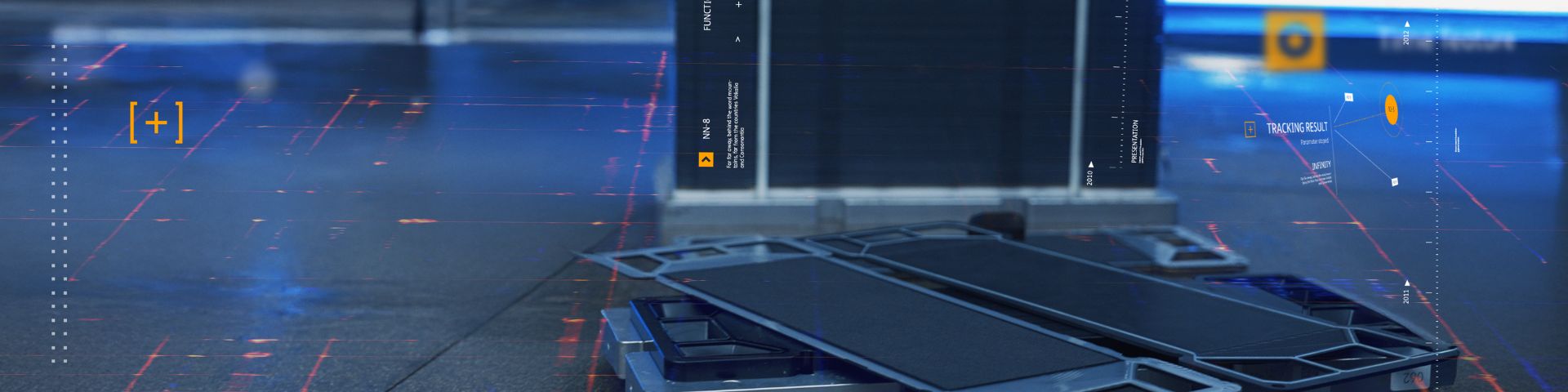
Fuel cells crucial for decarbonising heavy-duty transport and non-road machinery
While fuel cell technology is still in development, it holds great potential for decarbonising heavy-duty on-road, marine transport and non-road machinery applications. TNO Powertrains aims to accelerate this technology and bridge the gap to market by reducing fuel cell costs, improving durability, and supporting vehicle and vessel manufacturers, as well as technology integrators, in making smarter design choices.
As the debate on sustainable mobility and the superiority of different technologies continues, TNO believes that each application requires a tailored solution and that all technologies have a role to play. Hydrogen fuel cells are particularly crucial for hard-to-decarbonise heavy-duty niche sectors such as shipping, non-road machinery, and industrial stationary applications.
Cemil Bekdemir, Senior Scientist at TNO: 'The future of mobility is zero-emission, and fuel cell electric vehicles offer an efficient solution.'
Kamil Mrozewski, Hydrogen Fuel Cell Systems Engineer at TNO Powertrains: 'Fuel cells are highly versatile, converting hydrogen to electricity with no tailpipe emissions. This supports Europe and the Netherlands’ decarbonisation goals, air quality improvements, and zero-emission zones.'
Cemil adds: 'Grid congestion is a major issue, especially in the Netherlands. Hydrogen provides an alternative energy vector, transportable via trucks or existing gas pipelines. With strong renewable energy potential, the Netherlands can produce green hydrogen, ensuring a secure, geopolitically stable energy supply.'
Focus on cost reduction and durability
Although promising, the technology itself is pretty much still in development. Cemil: 'TNO is renowned for its fundamental research and expertise on fuel cells and electrolysers. This means we are still looking at hard core scientific and engineering topics like efficiency, durability, and cost effectiveness. Our role as TNO Powertrains is to focus on the application of fuel cells on a system’s level. As an orchestrator of innovation, TNO is able to build a powerful ecosystem that can really help accelerate this technology.'
Kamil: 'Cost reduction is, of course, a broad term. In essence, we support vehicle and vessel manufacturers and integrators in three key areas.
First, we help our partners in making smarter design choices by optimising the powertrain architecture, component sizing and developing the right control strategies. Optimising fuel cell operation significantly improves fuel economy, and component lifespan.
Second, when partners already have a system in mind or are developing a new prototype, we leverage our testing facilities to identify potential areas for improvement or critical failure points.
Third, we utilise a wide range of models and tools for data analysis. These models help us quantify the expected fuel cell lifespan, identify optimisation opportunities, forecast maintenance intervals, and ultimately reduce maintenance costs.'
Ideal for long stationary use
There is a wide range of fuel cell type. The most common is the low-temperature fuel cell, which uses a polymer electrolyte membrane (PEM). This mature technology has been intensely developed for over 50 years.
'Another promising option is the high-temperature solid oxide fuel cell (SOFC), operating above 600°C,' says Kamil. 'While more fuel-flexible and more efficient, SOFCs have longer start-up times, making them less suitable for dynamic applications, such as heavy-duty trucks, but ideal for shipping and other stationary applications. However, large-scale deployment, especially in the megawatt range for maritime and stationary use, still requires further development.'
Hybrid ships
Durability is one of the key challenges to make fuel cells applicable for the heavy duty sector, which is mainly determined by the way it is used. Cemil: 'The lifespan greatly varies with its application. The target lifetime for maritime applications is around 80,000 hours of operation, while for heavy-duty on road applications it’s roughly half of that lifespan. Therefore, fuels cells on ships need to have very long service intervals.'
Kamil: 'Existing, long-duration demonstrators, have shown that even low-temperature fuel cells can already operate for 65,000 hours. However, this figure was achieved in a specific stationary system and does not represent the typical durability of off-the-shelf products currently available for mobility applications. So the 80,000 hours of operation in real-world maritime conditions is an ambitious target. The primary degradation factor is operating load and that’s where TNO can support companies in the optimisation of the powertrain configuration and control strategies. A stable load extends lifespan, but real-world conditions rarely provide a perfectly flat load profile.'
'This is where other energy storage devices, like batteries, can absorb quick peaks in energy demand, perfectly complementing fuel cells and allowing them to maintain a steady output. Therefore, we are foreseeing ships with hybrid propulsion systems, combining fuel cells and batteries, which is the topic for a couple of new maritime projects we are starting as part of the Maritime Masterplan.'
Durable and sustainable
Material quality is another crucial factor in fuel cell longevity, further emphasising the importance of careful design and operation.
Kamil: 'In one of our recently granted projects funded by the European Union, we are modelling a non-PFAS membrane for fuel cells—an entirely new technology that could have a significant impact in the future, given a potential ban on PFAS-containing materials in the hydrogen sector. Our goal is to reduce the overall footprint of fuel cell technology, including supporting companies that develop the materials used and the production process. To achieve this, the project will develop fuel cell materials and components, such as cellulose-based membranes, which can be more sustainably sourced compared to current counterparts. We are also studying how these membranes will degrade over time, working to enhance their performance and durability.'
Cutting-edge facilities
Partners of TNO Powertrains benefit from an expansive range of cutting-edge testing facilities. Kamil: 'We have a total of six test cells that are hydrogen ready, with two more underway. We have been running tests with fuel cells and hydrogen combustion (H2-ICE) engines in the last couple of years. In addition, we have started testing with methanol and we are looking into ammonia in the future too, as a serious contender for fuelling maritime transport.'
In addition to hardware, the facilities also provide tools and models for testing software and control algorithms. The focus is on performance testing, revealing how the fuel cell is functioning in various operating profiles; with slow or very fast dynamics, at various temperatures, air pressures and humidity levels. Kamil: 'In our two climatic chambers we are able to create a broad range of climatic conditions, so manufacturers can make sure their technology works in every possible climatic condition our planet offers. With accelerated stress tests we mimic the natural degradation of fuel cell components in the best possible way, projecting test results on the real wear for accurate lifespan predictions.'
Watch videos
TNO's fuel cells
TNO's hydrogen engines
TNO's Battery Lab
Putting fuel cells into practice
Even though lab tests are crucial to mature fuel cell technology, valuable lessons can be learned from field tests. That is why TNO Powertrains helps partners set up demonstration projects, enabling integrators and end-users to test fuel cells in real-world operations.
Cemil: 'Currently, we are running two projects: a fuel cell truck for heavy-duty logistics, and a fuel cell excavator used for maintenance works at Lekdijk. Both projects are closely monitored to optimise performance. In addition, we will soon start working on maritime projects with a similar scope.'
Previously, fuel cells for non-road mobile machinery were tested in a TKI project called 'Elevate.' Kamil Mrozewski: 'Our team, in close collaboration with partners, supported the simulation and design of a battery and fuel cell powertrain for a multi-purpose non-road mobile platform for forestry machinery, including a digger and a cutter, as a sustainable alternative to diesel-powered equipment.'
Strategic hydrogen refuelling hubs
The question on everyone’s mind is: when will we see large-scale adoption of hydrogen and fuel cells? 'This requires a systemic change,' says Kamil. 'The biggest bottleneck for fuel cells and hydrogen combustion engines is, obviously, hydrogen availability. Infrastructure rollout remains a major challenge, delaying widespread fuel cell deployment. One short-term solution is the development of strategic hydrogen refuelling hubs in high-demand locations, such as the Port of Rotterdam, where both ships and trucks can utilise shared infrastructure.'
Cemil adds: 'Beyond hydrogen infrastructure, the cost of fuel cell vehicles is another major challenge. While vehicle costs are beyond TNO’s direct influence, reports indicate that scaling up production will drive cost reductions. For hydrogen to be viable, infrastructure and vehicle adoption must grow together. Our goal is to make hydrogen technically attractive, accelerating demand and lowering costs.'
Kamil concludes: 'In many ways, fuel cells face challenges similar to early-stage batteries, solar, and wind energy. Initially expensive and unfamiliar, these technologies became mainstream through economies of scale, technical improvements, and innovation.'
Get inspired
Health of electric bus batteries now measurable on-site via charger
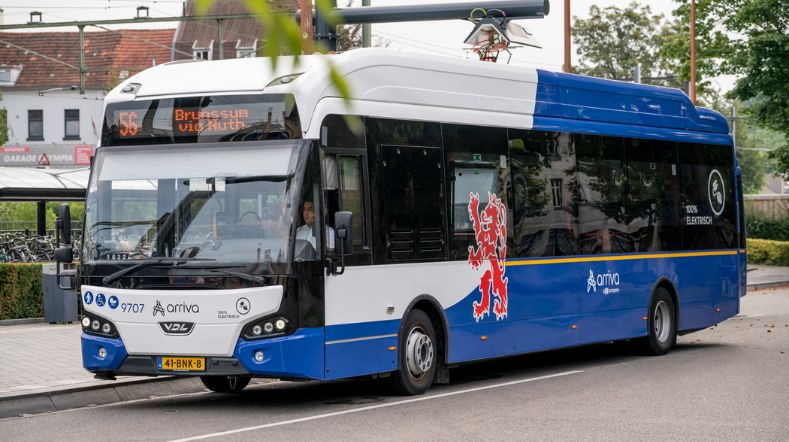
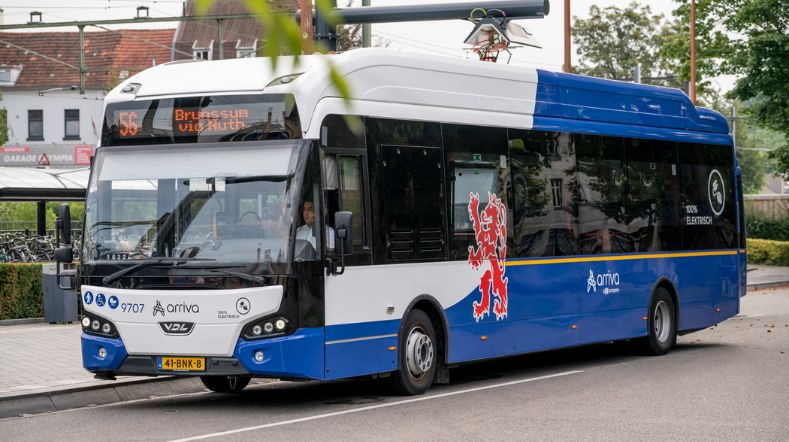
Demonstrations of automated driving and charging for logistics at Maasvlakte
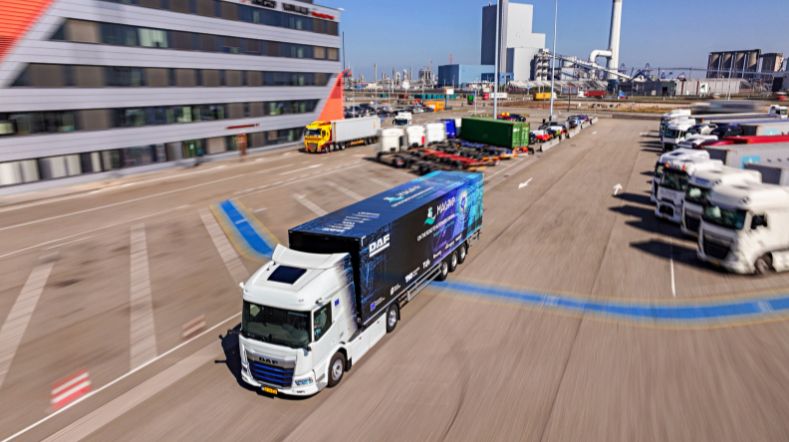
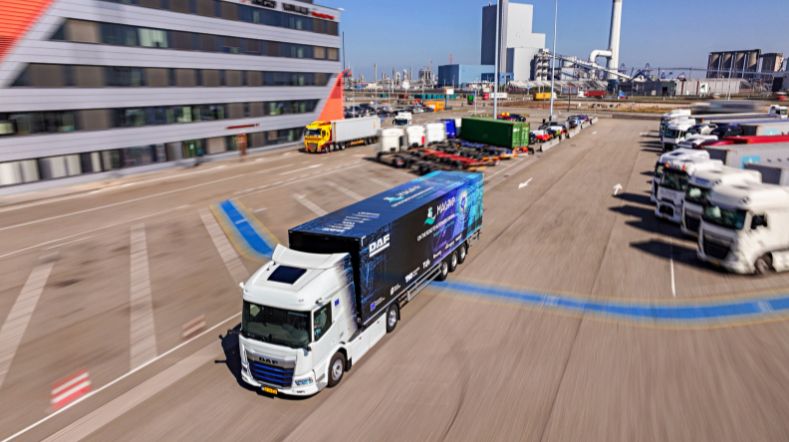
Transition co2 neutral mobility 2050
TNO accelerates electrification of logistics and construction through a deeper understanding of batteries
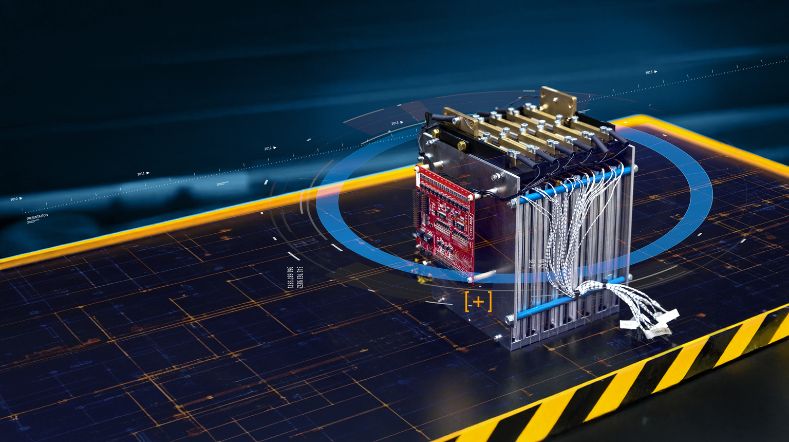
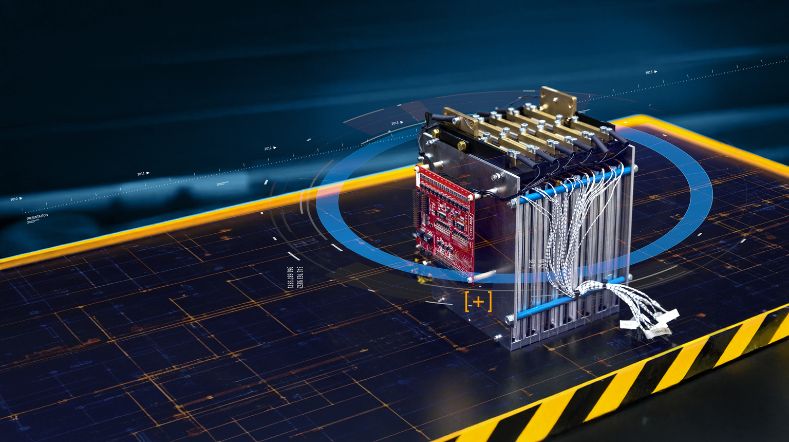
Clean and robust hydrogen engine pivotal for achieving emissions targets heavy transport
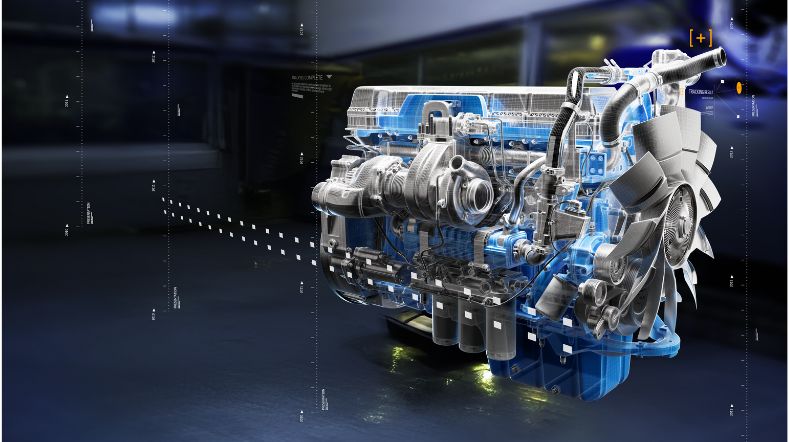
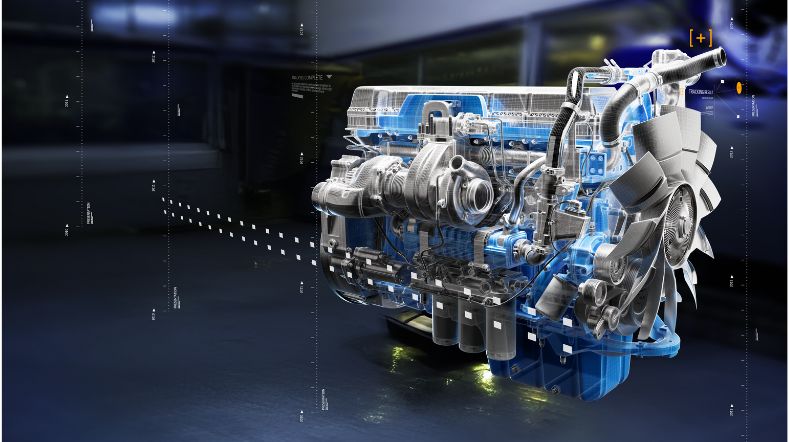