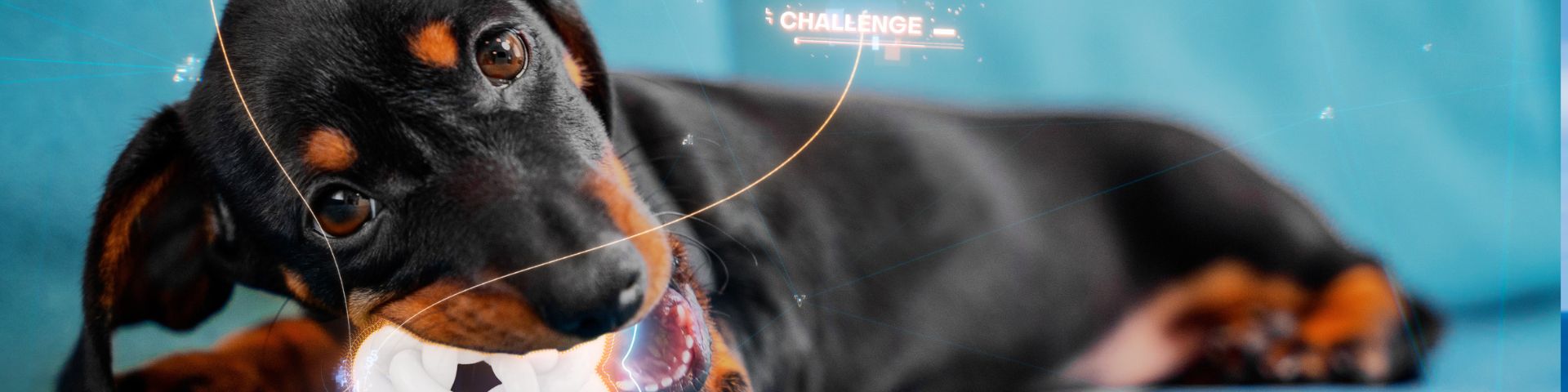
Biobased plasticizers: from compliance to competitive edge
Plasticizers are additives that increase the flexibility and pliability of plastics and reduce brittleness. They are found in everything from packaging to textiles, from dogs’ chew toys to 3D-printed automotive components. For decades, fossil-based plasticizers have dominated the market. Today, TNO is demonstrating how biobased plasticizers can not only be more sustainable and less toxic, but also enable significant competitive advantage for companies aiming to innovate.
Opportunity for growth
‘Chemical and plastics companies have been using fossil-based plasticizers for decades, so they have very little desire to change a winning formula,’ explains Paul Könst, TNO Project Manager and Biorizon Programme Manager. ‘Yet the most innovative organisations are already exploring biobased solutions, in anticipation of changes that may soon impact the entire plastics value chain.’
According to Paul, biobased plasticizers are much more than just a more sustainable alternative to fossil building blocks. As concern grows about the toxicity levels of these commonly used chemicals, there are increasing discussions about limiting, or even banning, their use.
‘However, our work has uncovered an advantage beyond sustainability or lower toxicity,’ Paul says. ‘Our novel biobased plasticizers have the potential to outperform fossil-based ones, and that’s really getting the industry’s attention.’
In 2013, TNO joined forces with VITO in the shared research programme Biorizon. Together, we began exploring promising possibilities to replace fossil chemicals with biobased alternatives. TNO is applying its expertise, experience, network and technologies to develop sustainable building blocks for the chemical industry. Together with VITO, we aim to address the growing need to replace fossil-based chemicals with sustainable – and superior – alternatives.
Rapid development, superior results
Marc Crockatt, TNO Senior Scientist and Biorizon Lead Scientist, explains how TNO is helping companies discover how biobased plasticizers can result in superior products. ‘Most companies don’t have the infrastructure, knowledge, or expertise to develop a biobased alternative to the plasticizer they need. Every product and application requires a specific type of plasticizer with distinct properties,’ he says.
‘TNO develops, validates, and characterises plasticizers with the exact properties needed for each specific application.’ And it happens faster than you might think: ‘We often go from theoretical concept, to gram-scale validation, to kilogram-scale production of a viable biobased alternative in less than 12 months.’
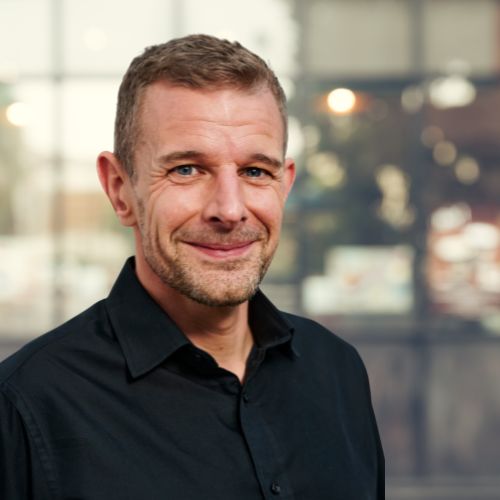
‘We often go from theoretical concept, to gram-scale validation, to kilogram-scale production of a viable biobased alternative in less than 12 months.’
Swift development is just one of the many advantages of partnering with TNO. Instead of only developing drop-in replacements for fossil building blocks, TNO also aims for novel replacements that offer superior performance. In the BIO-CAPPP project, TNO is working with the research institutes Avans/MNEXT and Centexbel –developing applications in biobased plastics and textiles, respectively.
Together, the BIO-CAPPP partners have developed biobased plasticizers that enable resilient textile prints that are less prone to cracking, and 3D-print filaments that are easier to handle and result in more durable products than their fossil counterparts.
‘We developed sustainable, less toxic plasticizer alternatives that meet Avans and Centexbel’s exacting specifications. Avans even discovered that they can achieve similar performance using much less biobased plasticizer than they used with petrochemical plasticizers, which can result in cost savings,’ Marc explains.
Partnering for change
Both Paul and Marc recognise that many companies are hesitant to change a process that has worked for decades and face the costs and risks that innovation can bring. But, they say, ambitious companies that aim to stay ahead of a changing market should start today.
‘In addition to changing legislation and the threat of a limit being imposed on fossil plasticizers, consumer demand is shifting significantly towards sustainable alternatives,’ Paul says.
‘Through Biorizon, TNO addresses our partners’ specific requirements for their market application, and achieve representative scale swiftly – driving fit-for-purpose biobased alternatives that are stronger, safer, and more cost-effective.’
TNO and Biorizon engage in nearly every form of partnership – from early shared research to targeted and contracted private development. SMEs in the Interreg region can even take advantage of Biorizon’s innovation voucher programme to get started.
‘We know that the transition to sustainable plastics won’t be easy, and won’t be fast,’ Marc adds. ‘But each step we take towards viable biobased alternatives will bring the industry closer to full circularity and safety.’
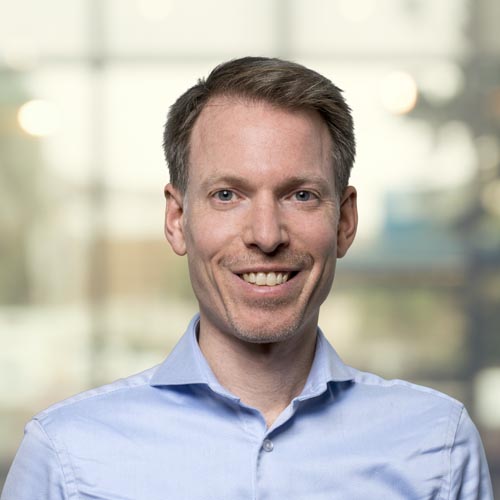
‘We address our partners’ specific requirements for their market application, and achieve representative scale swiftly – driving fit-for-purpose biobased alternatives that are stronger, safer, and more cost-effective.’
Visit us at the K Trade Fair
You can find us at the world's largest trade fair for plastics and rubber.
8 to 15 October 2025, Düsseldorf, Germany
📍We will be in Hall 7, stand SC10
Get inspired
Progress in circular packaging for soups and sauces
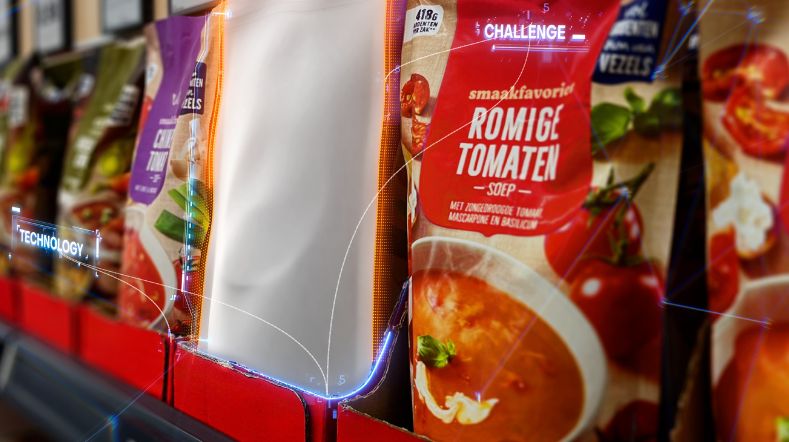
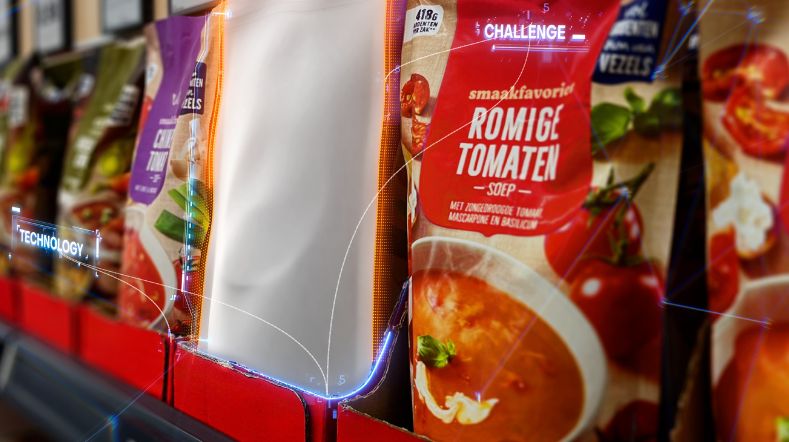
Microplastics in clothing
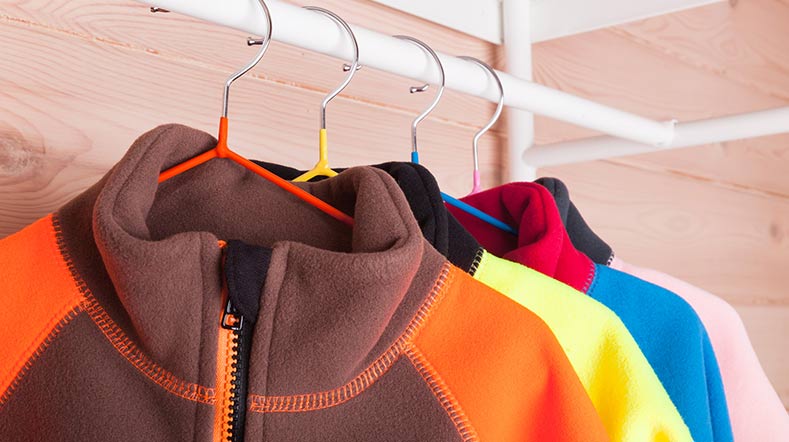
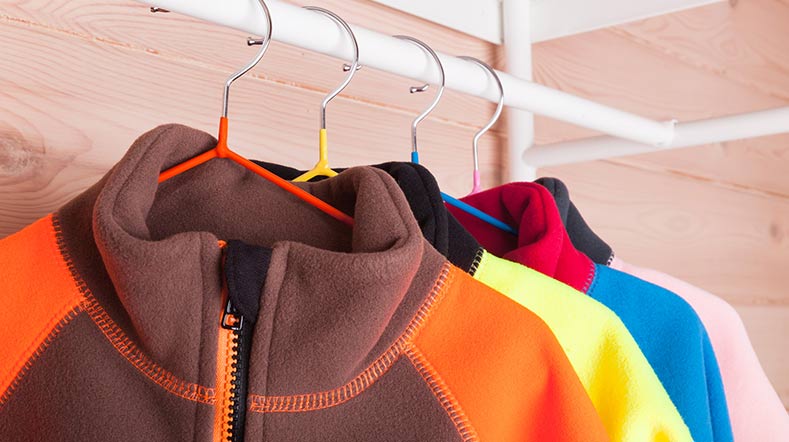
Early results show the potential of circular healthcare plastics


Thermoplastic composites for sports innovation
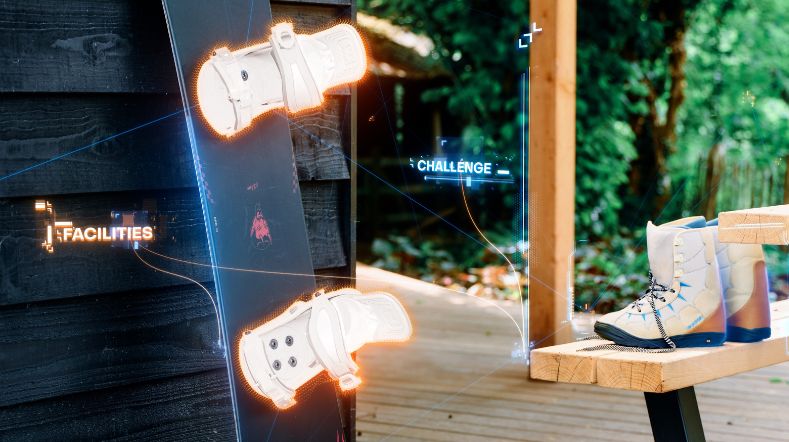
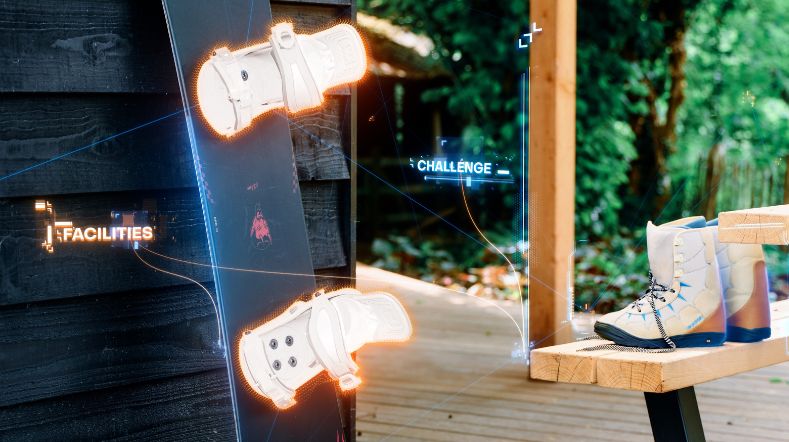
Biobased materials
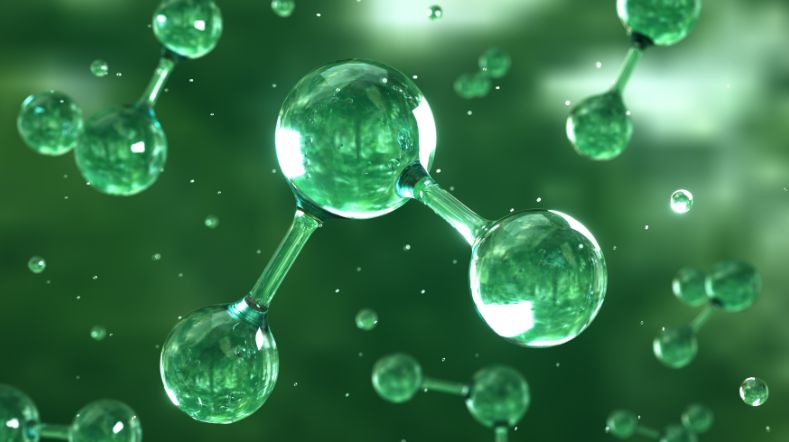
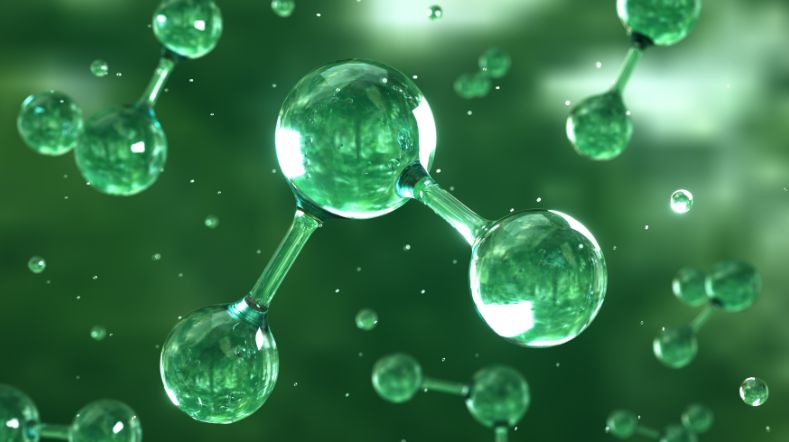