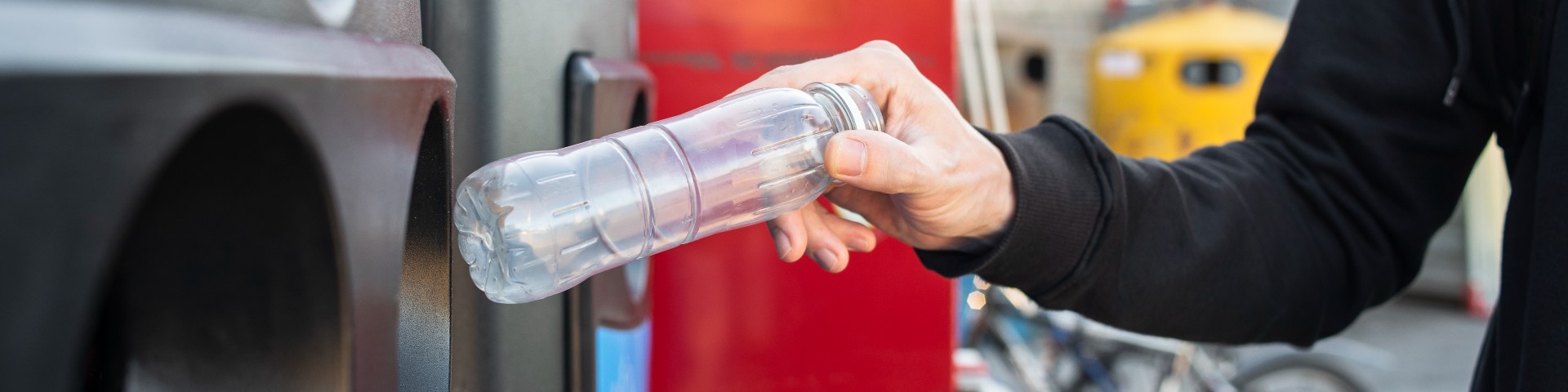
Improve quality of plastic waste with innovative Upwash technology
Currently, only a small proportion of the plastic we use every day is recycled. Reusing more plastic waste requires innovative technologies that can recycle plastic as efficiently and effectively as possible. The Upwash concept devised by TNO is one such technology, which is now being further developed and made ready for scaling up.
Plastic waste as an alternative to fossil raw materials
In order for us to break free from using fossil raw materials for plastics, they must be replaced by alternative carbon sources. Plastic waste seems to be a good option because chemically, it’s most similar to the fossil raw materials it’s meant to replace.
However, it takes a very large amount of plastic waste to replace all the fossil raw materials used to produce plastic. So much that there will even be a scarcity of good, clean plastic waste.
Focus on the front end of the chain
Several steps are necessary to obtain suitable plastic waste for recycling. After collecting, sorting, washing, grinding, and granulating, the plastic has to be separated and purified to ensure quality for new plastic production.
The focus is now on converting clean plastic waste into new raw materials for polymers. However, the current quality and quantity of plastic from collection and sorting doesn’t meet the quality and quantity that will be required.
"As part of the Brightsite knowledge centre, we’re investigating how to improve quality while significantly increasing the amount of suitable plastic waste," says Rinke Altink, Programme Manager for Renewable Feedstocks at TNO Brightsite.
Clean plastic waste stream
The focus is on ‘mixed plastic wastes’, which remain after all the plastics that can be mechanically recycled have been sorted. Upwash, which is a hydrothermal technology, is one of the ways to extract greater quantities of good quality plastic from these waste streams.
How does Upwash work?
With Upwash, plastic waste streams are treated with hot water, well above 100° Celsius and under pressure. The density of polyolefins, widely used as packaging materials, is lower than that of water. These plastics can therefore be separated from other higher-density plastics.
Contaminants such as food residues are also removed during this hot ‘washing step’, leaving a much cleaner plastics waste stream. The advantage of Upwash is that no additives such as chemical solvents are needed.
Scaling up to economic scale
The Upwash process is currently being scaled up from laboratory scale – 30 litres, in which about 1 kilo of waste is purified per test – to pilot scale. The pilot scale is the intermediate step between lab and industrial scale: small enough to still be reasonably flexible, while large enough to be translated to the real thing.
In the pilot phase, we simulate the situation on a large scale and can also look at aspects such as the energy and water consumption of the process and how to minimise it. We’re working with a multidisciplinary team to properly highlight all facets of scaling up.
The aim is to have the pilot operational by 2025. Development to demonstration level should be ready about 3 years later, so that it can be run on an economic scale for the first time around 2030.
Vision of the future: part of the value chain
Ultimately, we want to ensure that the pure polyolefins obtained with Upwash can be channelled directly to factories, becoming part of the value chain. That means we need to move to a continuous process on an industrial scale, and getting there is quite a complex matter.
Altink explains: "We’re now looking at plastic waste streams coming from households, but in the future, we should also target other waste, as long as it contains enough of the right plastics, i.e., with a low density.
Moreover, the plastic waste streams of the future, in which recycling is taken into account in the design, will be different from today’s waste. We aren’t going to wait for that, but we have to keep it in mind. With Upwash, we can contribute in the relatively short term. And we need to start now, given the climate problems."
Join us!
We intend to work with partners over the coming period to determine how Upwash technology fits into the circular plastics value chain. Want to know more about the capabilities of Upwash? Or would your company like to contribute to the further development and validation of this technology? If so, don’t hesitate to contact us.
Get inspired
Circular packaging

