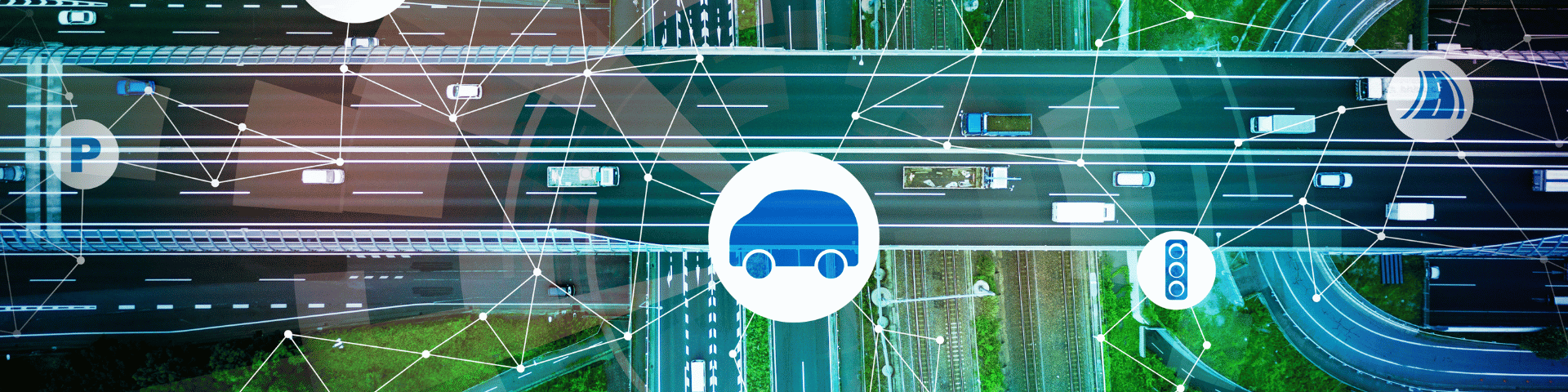
TNO research on powertrains
To achieve long-term sustainable transport solutions, the Powertrains research group supports a path requiring a monumental joint effort from policymakers and industry partners for on-road and off-road mobility, waterborne transport, and energy production. Innovative, more efficient, and cleaner powertrains will significantly contribute to the energy transition toward low- or zero-carbon mobility, impacting all sectors.
Creating tomorrow’s sustainable powertrains today
At TNO Powertrains, our team of over 35 scientists and 17 lab researchers excels in modelling, controlling, and testing powertrains. We focus on zero- or low-carbon fuels, including hydrogen engines, batteries, fuel cells, and energy management. Our goal is to accelerate the energy transition by developing these technologies through independent research, supporting industry integration and calibration, and consulting on optimal solutions. Additionally, we support the TNO Sustainable Transport & Logistics group by providing results that inform policymakers on the most energy- and environmentally-friendly strategies.
Accelerating R&D
The transition to sustainable powertrains aims to maximise overall efficiency, predict and extend powertrain lifetime, reduce development time, and advise on lowering the Total Cost of Ownership (TCO) for OEMs, integrators, and end-users. To achieve these results, we leverage our expertise in powertrain technologies, physics and data-based modelling, energy management strategies, advanced testing, validation methodologies, and certification in our testing facilities. We help accelerate OEMs’ R&D to bring sustainable powertrains to market.
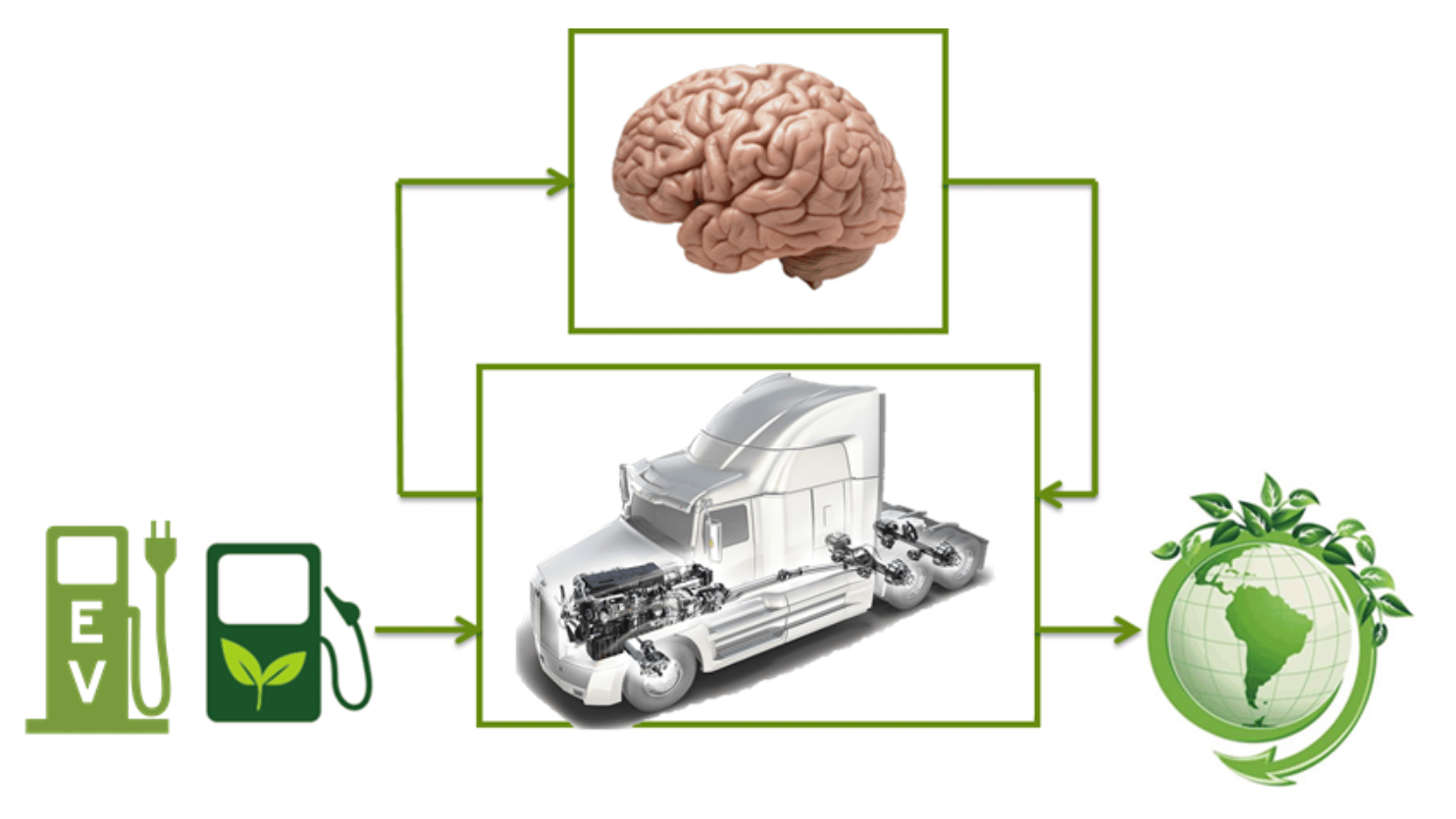
Physics-based and validated models
A representative mathematical model, based on TNO Powertrain’s in-house developed component library, defines the actual powertrain system. Uniquely, all our models are physics-based, validated in our facilities, fully predictive, scalable, and controllable, and can be implemented in real-time. Each component model is equipped with MATLAB-based tools for easy, systematic calibration for specific applications.
The impact of an optimised powertrain depends on the type of energy used and how the application operates in its target environment. This is in the context of current and future legislation and targets on gCO2/km.
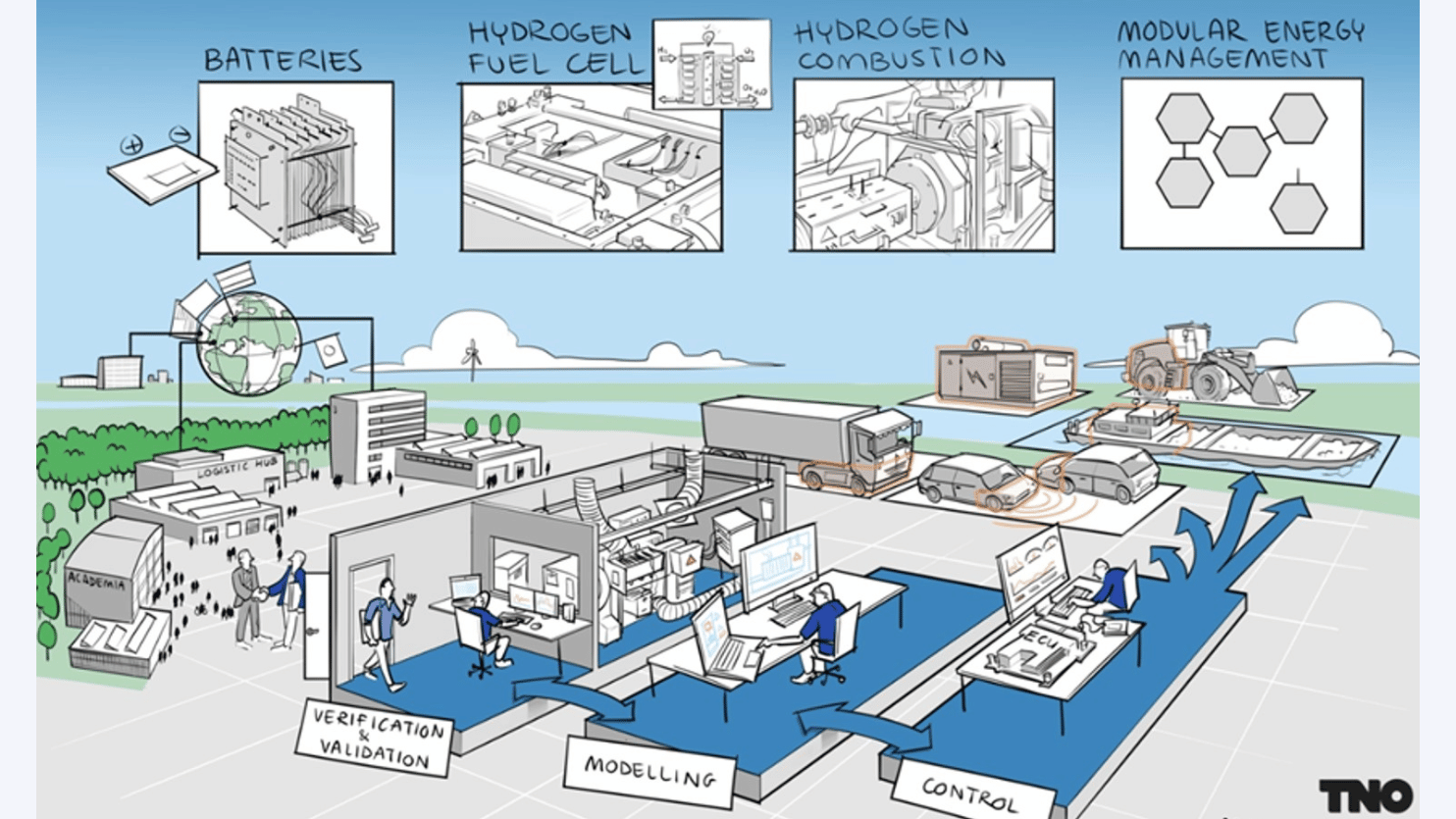
Four technology lines
Our expertise domains are in four different technology lines, distinguishing between testing, modelling, and control.
1. H2-ICE
-
Testing: model parameter and state estimation
-
Testing: health diagnotics
-
Modelling: aftertreatment
-
Modelling: internal combustion engine
-
Control: adaptive control
-
Control: optimal control
2. Energy management
-
Testing: model parameter and state estimation
-
Testing: health diagnotics
-
Modelling: aftertreatment
-
Modelling: battery
-
Modelling: internal combustion engine
-
Control: adaptive control
-
Control: optimal control
3. Battery monitoring and control
-
Testing: model parameter and state estimation
-
Testing: health diagnotics
-
Modelling: battery
-
Control: adaptive control
-
Control: optimal control
4. Fuel cell monitoring and control
-
Testing: model parameter and state estimation
-
Testing: health diagnotics
-
Modelling: battery
-
Modelling: fuel cell
-
Control: adaptive control
-
Control: optimal control
Our model-based tool chain enables us to use:
- Seamless integration of testing, modelling and control.
- Systematic, integrated approach that maximises overall powertrain performance.
- Exploit synergy between subsystems systematically.
- Expertise includes climate and on-road testing.
Powertrains Test Centre
To verify and validate our methods for sustainable powertrains, TNO Powertrains offers unique research and test facilities at the Powertrains Test Centre (PTC) in Helmond. The PTC provides testing, validation, and certification for heavy-duty and non-road mobile machinery by conducting experimental research on powertrains (full and partial assemblies), including combustion engines (mainly hydrogen), batteries (cells, packs, modules), and fuel cell systems.
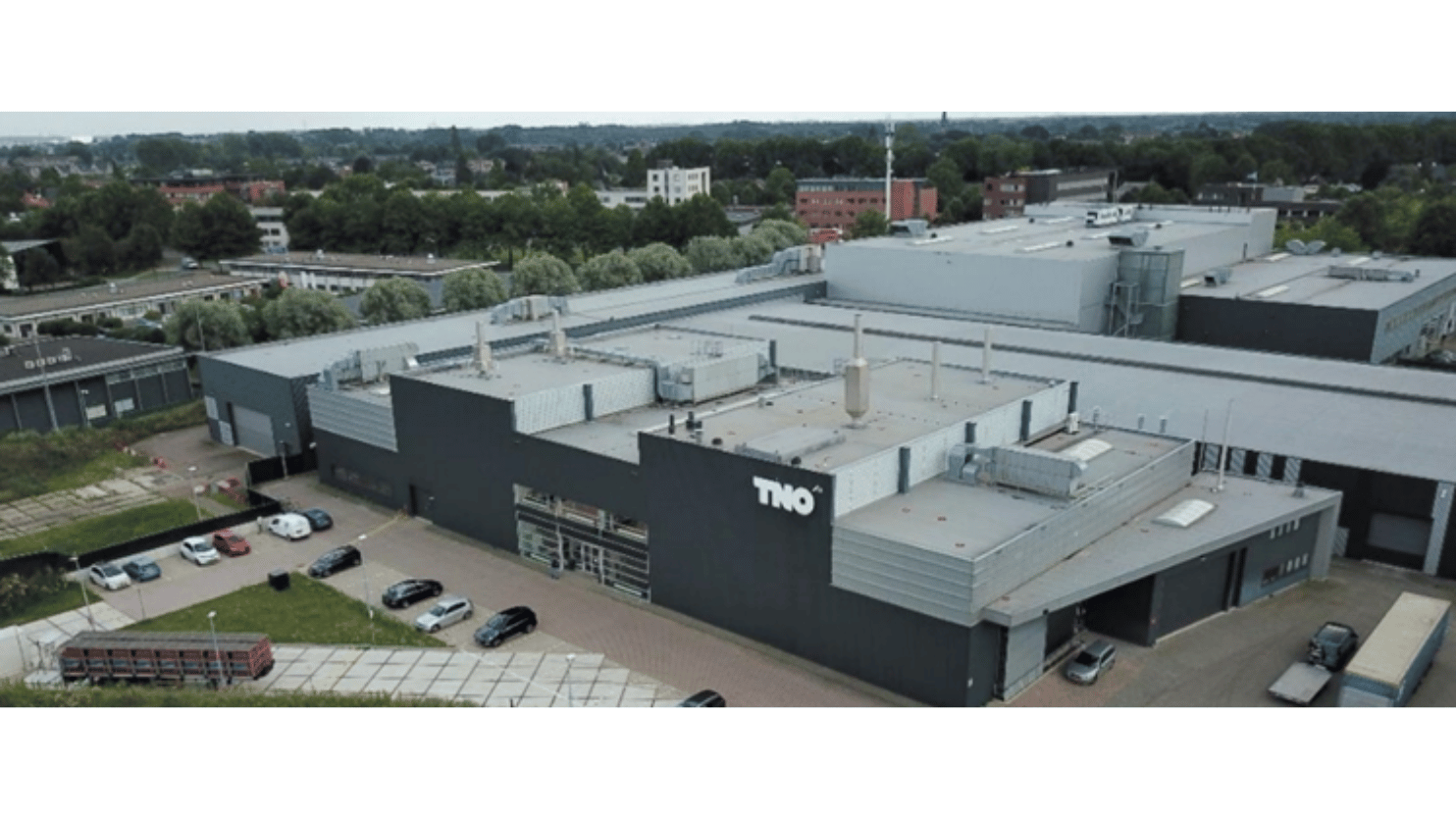
Unique test facilities
The PTC features multiple climate chambers, fuel and emissions testing facilities, electrical test benches, and a wide variety of liquid (ex. Methanol) and gaseous fuels ( including hydrogen) infrastructure, all operated by expert staff. Six engine test cells analyse regulated (NOx, CO2, THC, PM, PN) and unregulated (NO, NO2, CH4) emissions. These cells support extensive instrumentation, control, safety, and fuel and cooling management. The six cells, each with dynamometers ranging from 600 kW to 1400 kW, are nearly identical. Three cells include a bi-directional 300 kW electrical load/supply simulator for testing batteries and fuel cells.
Field test facilities
For field tests, we use our Portable Emissions Measurement System (PEMS) for on-road emission measurements (mainly NOx and CO2) of heavy-duty vehicles (trucks and buses). Measurement results are used for In-Service Conformity (ISC) testing and Real Driving Emissions (RDE). We also use the Sensor-based Emission Monitoring System (SEMS), developed by the TNO STL group, as a cost-efficient and effective alternative to PEMS testing and for monitoring electrified vehicles.
Battery Lab
The Battery Lab drives the advancement and adoption of new battery technologies, supporting its partners in accelerating the electrification of (heavy-duty) road and non-road applications forward.
Get inspired
Fuel cells crucial for decarbonising heavy-duty transport and non-road machinery
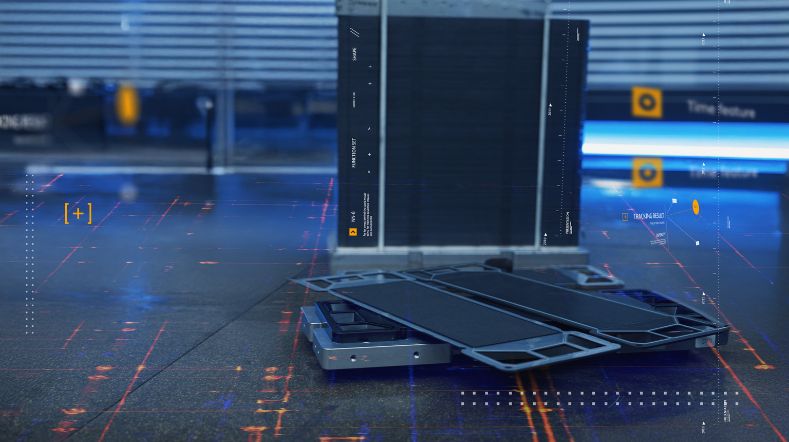
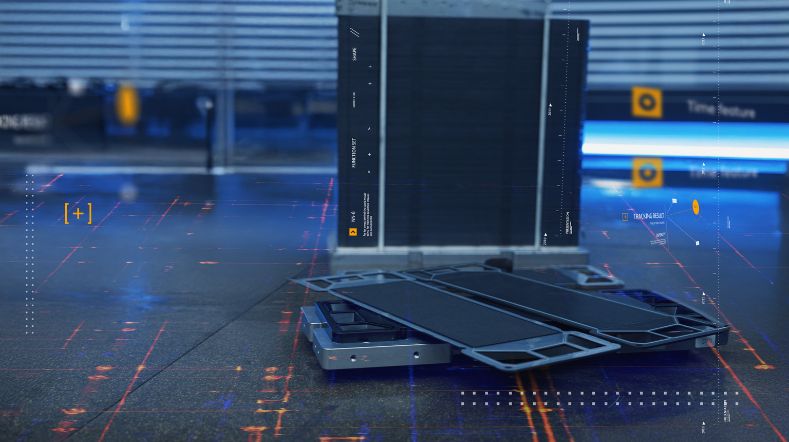
TNO accelerates electrification of logistics and construction through a deeper understanding of batteries
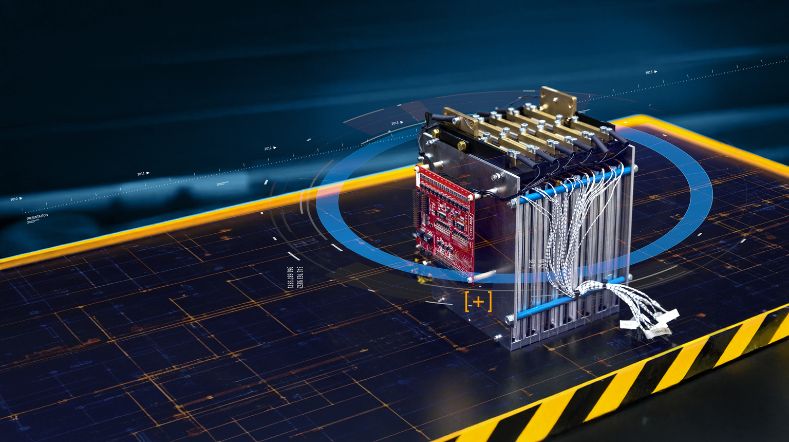
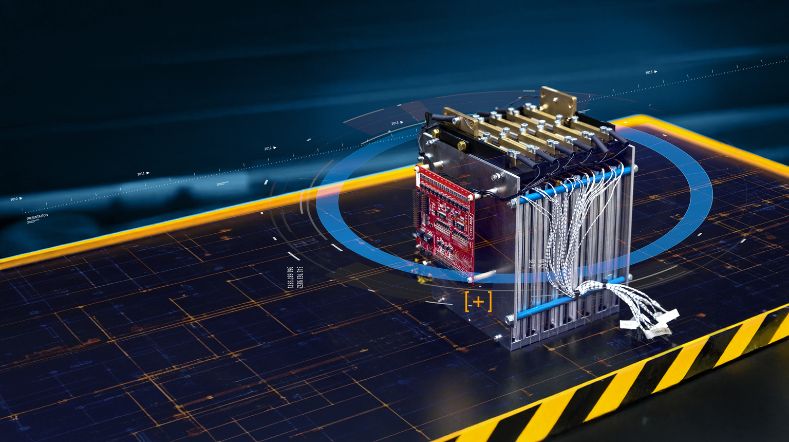
Clean and robust hydrogen engine pivotal for achieving emissions targets heavy transport
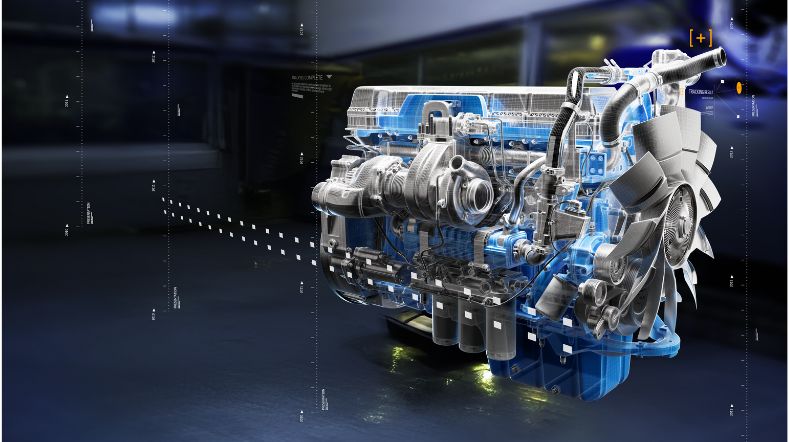
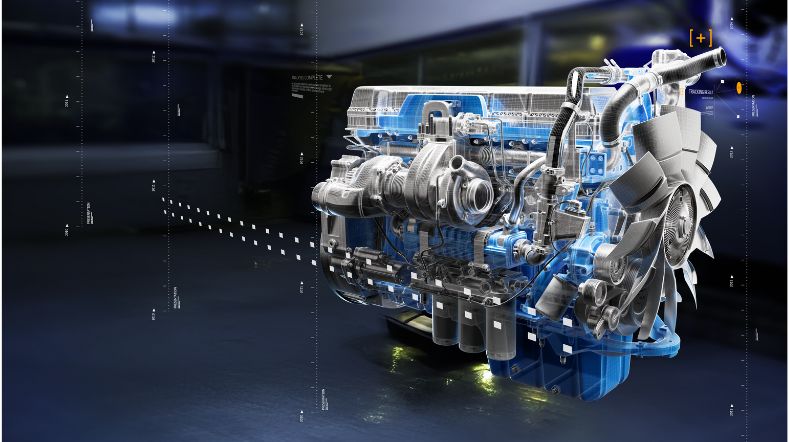
TNO helps battery and vehicle sector with future-proof implementation of battery passport
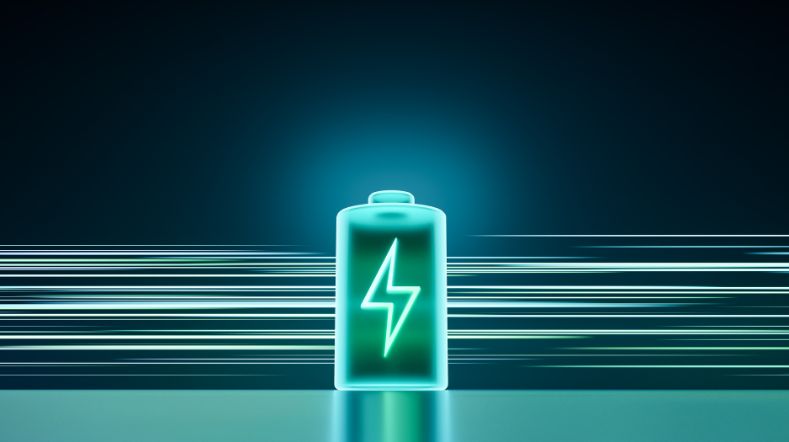
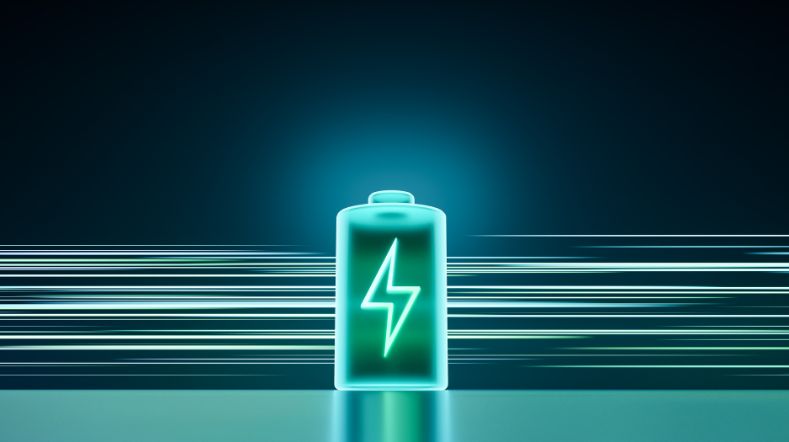
Optimal charging planning for logistics service providers considering grid congestion
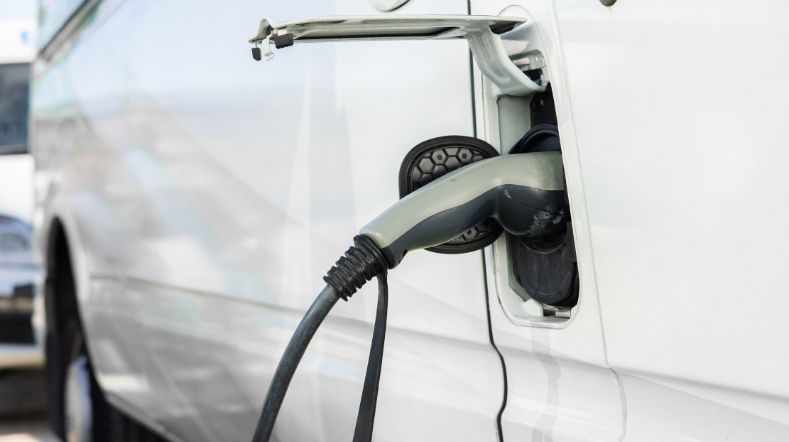
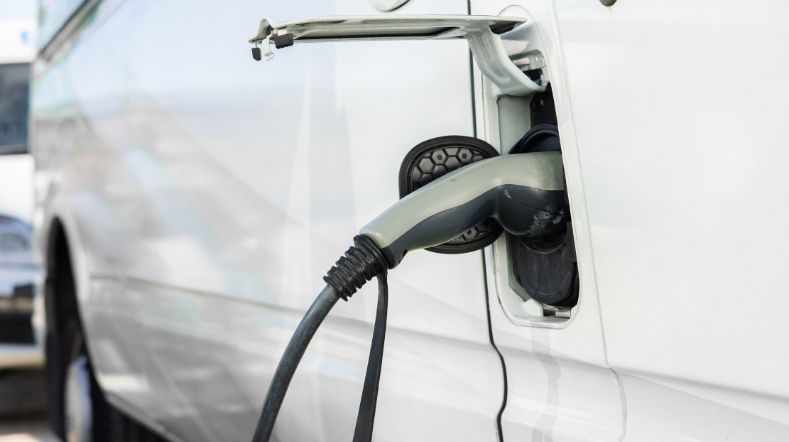