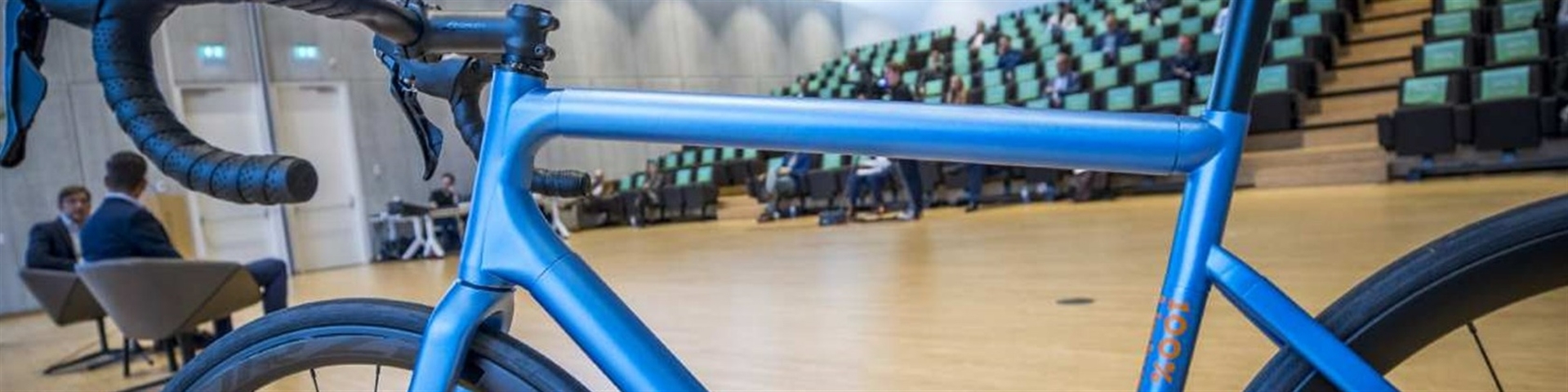
Brightlands Materials Center for new sustainable materials
The world's population will reach ten billion by 2050. Do we want to pass on a healthy planet to the next generation? If so, this will require major changes in the use of energy and material resources. Brightlands Materials Center takes on this challenge. We work on research and development programmes to accelerate the transition to a circular economy.
Brightlands Materials Center
At the Brightlands Materials Center, we conduct research into new, sustainable technologies in the field of plastics and their applications. We develop innovative material solutions for a sustainable future.
We do this together with industry, universities and entrepreneurs, to help a variety of companies and sectors with technical challenges to find sustainable solutions. These include smart coatings for solar control glass, thermoplastic materials for lightweight constructions, and 3D printing technologies for sustainable manufacturing.
Research programmes
In our research, we focus on major societal challenges. We work on aspects of sustainable mobility, sustainable buildings and circular packaging. We deal with buildings and mobility, as they are responsible for a large part of the carbon emissions that cause global warming.
Plastic is a very efficient way of safely packaging food products. But there are no circular solutions for it yet. This is why we develop innovative technologies for sustainable and circular materials. Find out more about our three research programmes:
Want to know more?
Find out more about our research programmes on the Brightlands Materials Center website.
Get inspired
VoltaChem Year Event 2025
Renewable syngas: essential for industrial decarbonisation
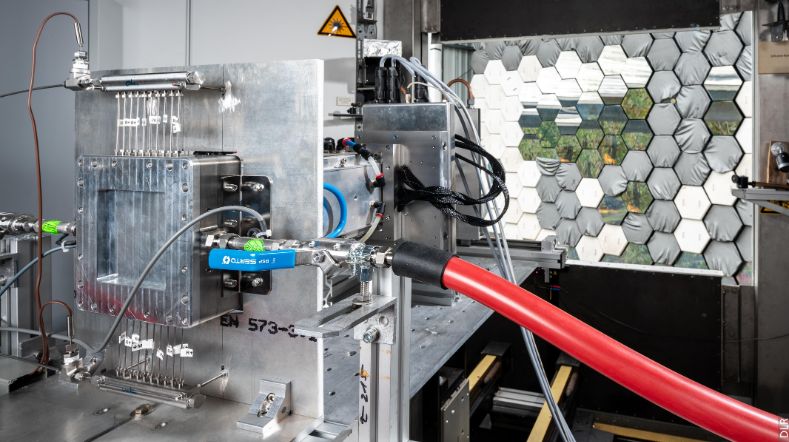
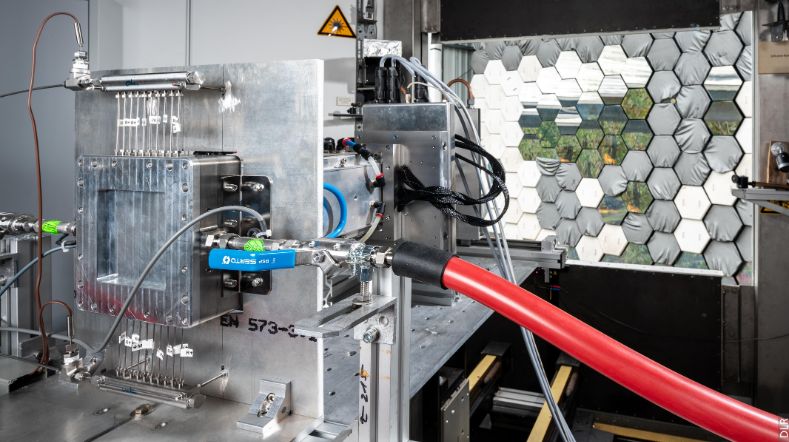
Western North Brabant becomes hotspot for biobased building blocks for the construction industry
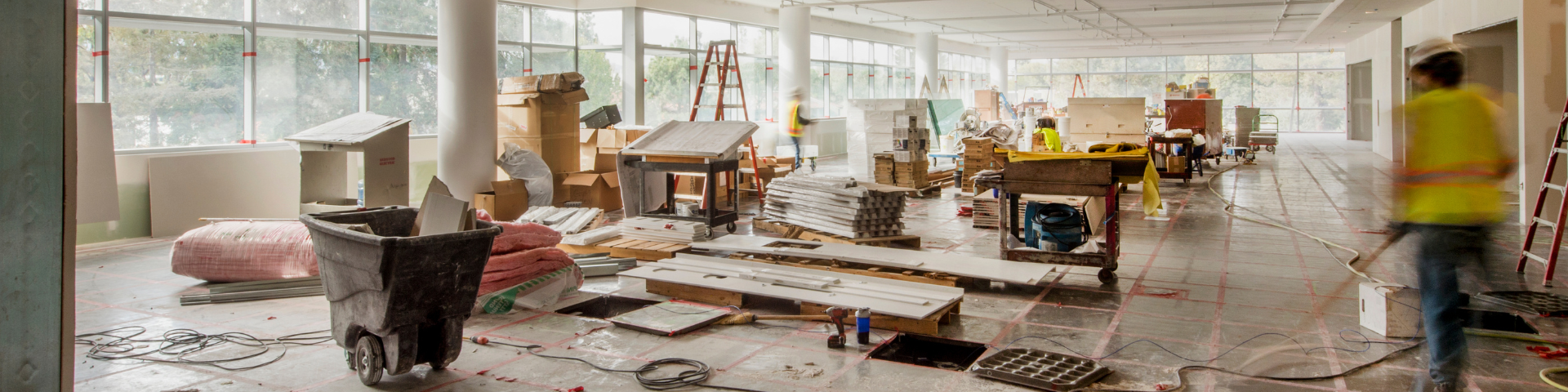
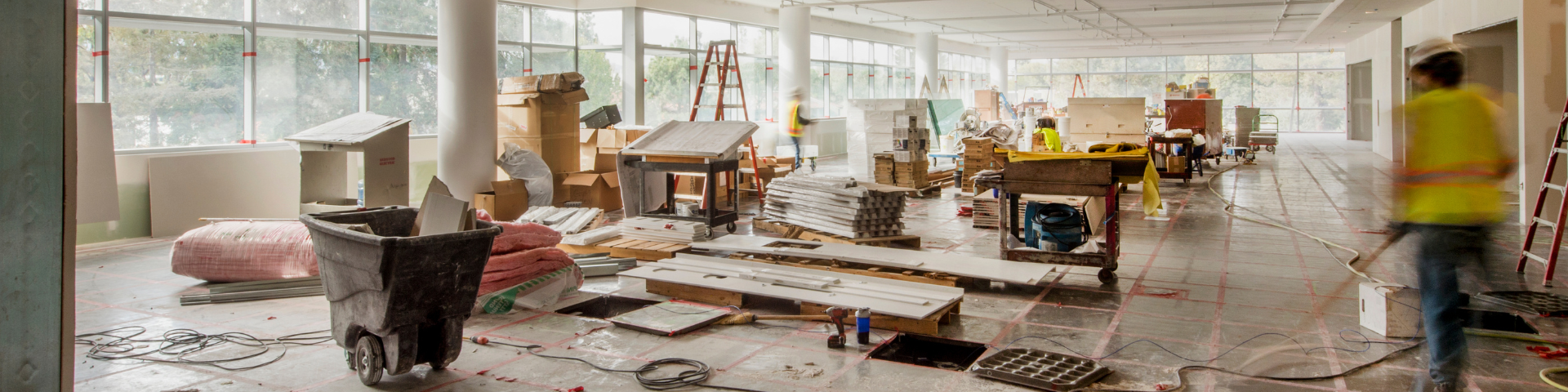
New facility to develop circular plastics on an industrial scale
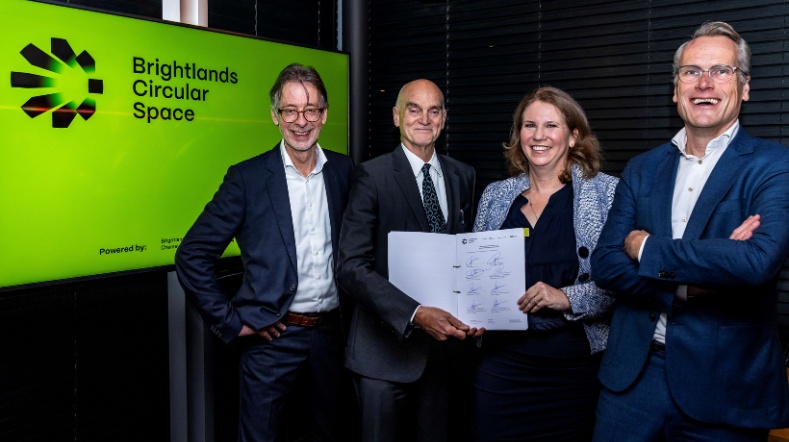
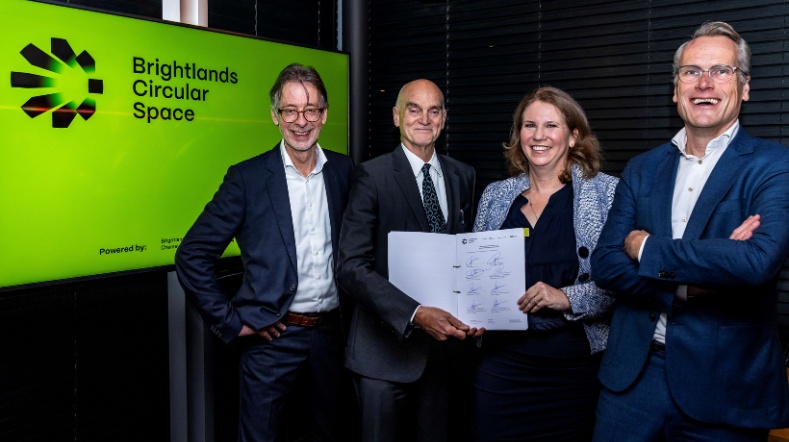
Time setters: Smart windows bring climate-neutral living a step closer
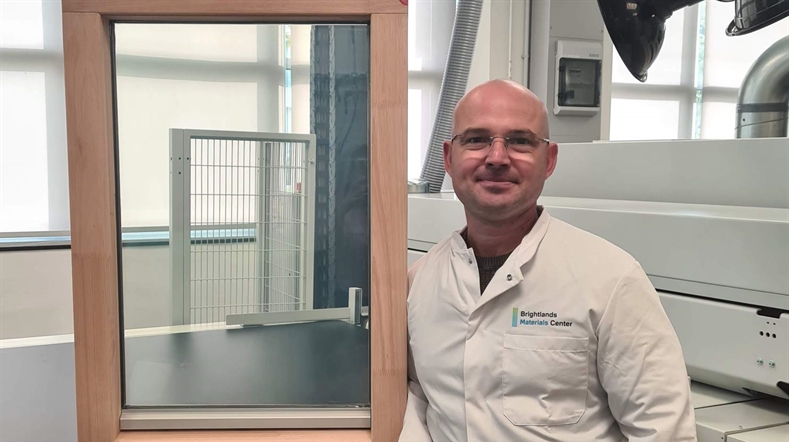
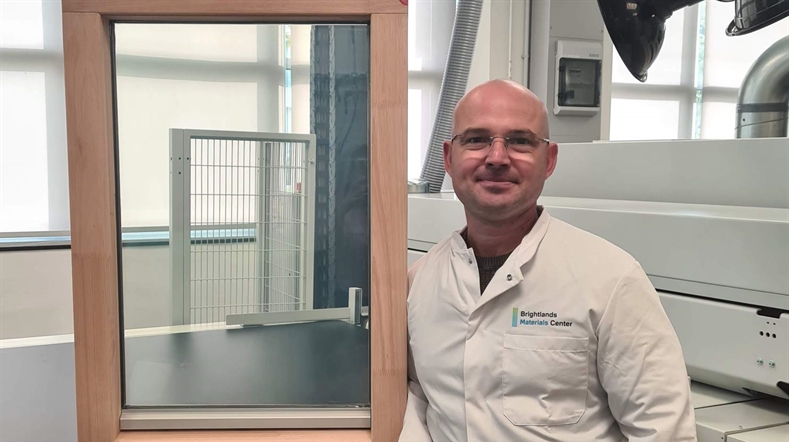