Sustainable industry
The chemical and process industries face enormous challenges. The pressure to reduce CO2 emissions, embrace circular economy and stay competitive at the same time is increasing. Companies are looking for ways to make their processes more sustainable without sacrificing efficiency and profitability.
At TNO, we understand these challenges. We research, develop and orchestrate breakthrough innovations that enable the transition to a carbon-neutral industry and society.
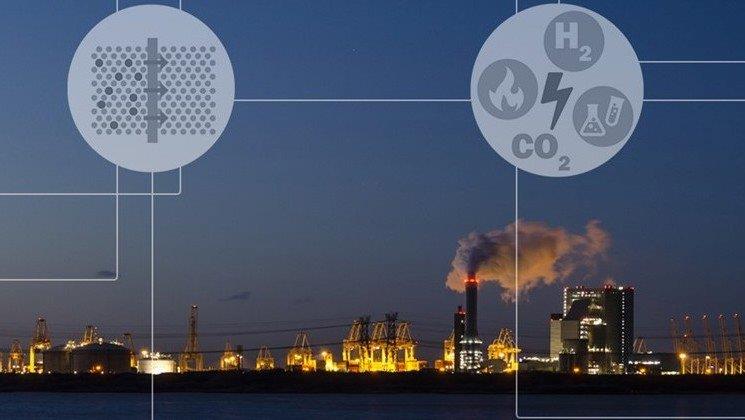
Towards a CO2-neutral industry
Industry accounts for about one-third of CO2 emissions in the Netherlands. We’re working to make industry carbon-neutral by 2050, so there’s a huge amount to do.
Our latest developments
62 resultaten, getoond 1 t/m 5
Energy infrastructure and transport
Together with our partners, we are developing infrastructure that safely, efficiently, and sustainably transports CO₂ and hydrogen across land and sea.
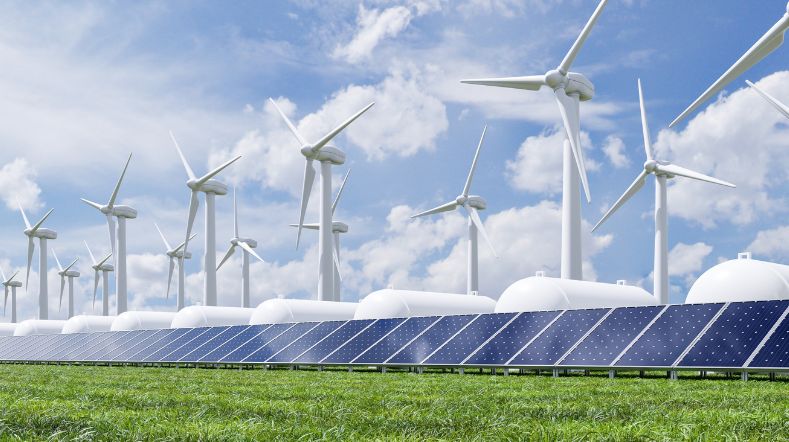
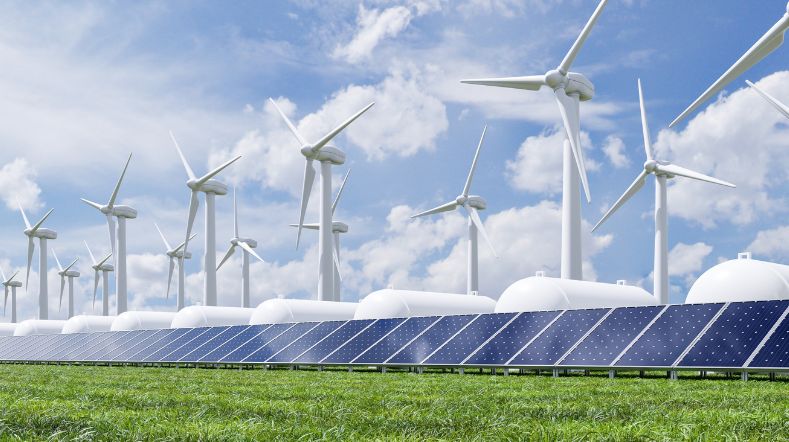
The North Sea as Europe's energy heart requires smart choices
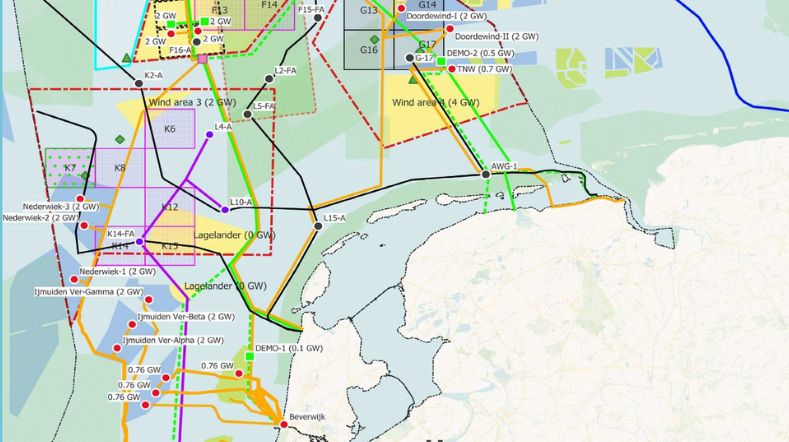
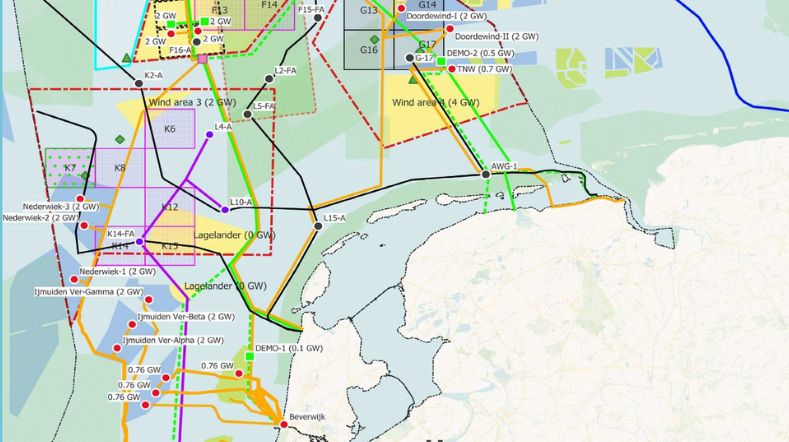
Tomorrow’s hydrogen production and infrastructure: building towards a secure and robust energy system
World Hydrogen Summit 2025
Scaling-up electrochemical technologies for renewable ethylene production
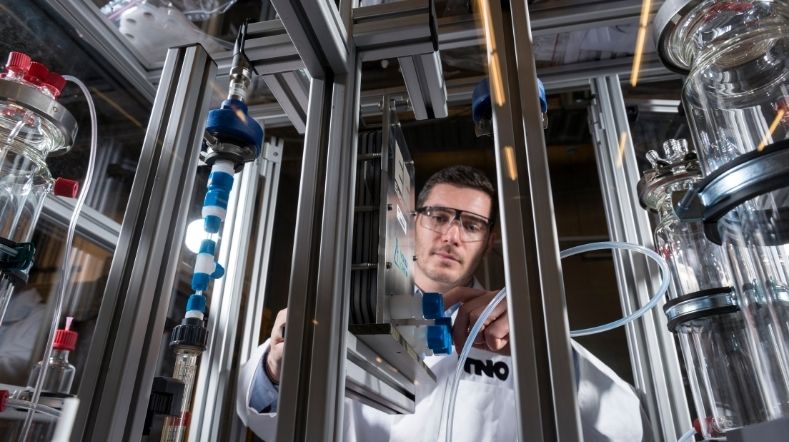
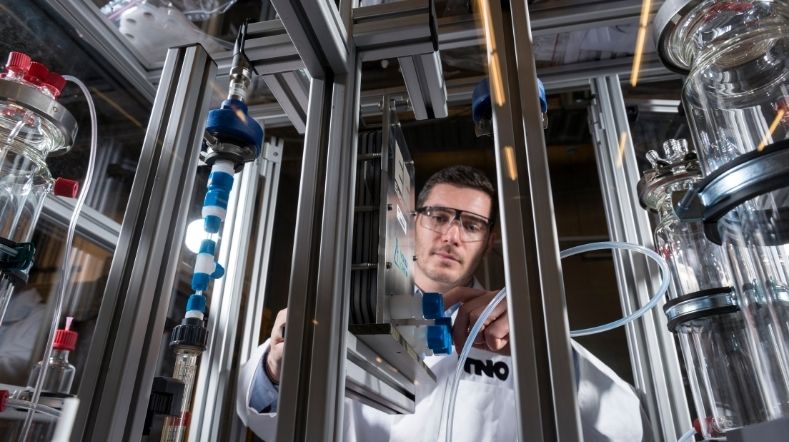