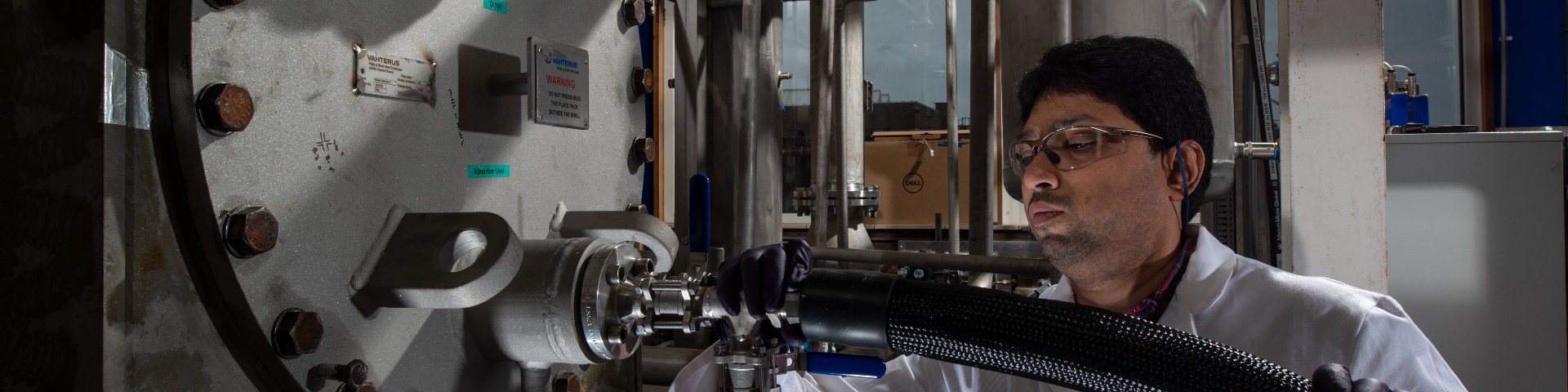
Making industry more sustainable
Industry causes high carbon emissions and often inefficient use of raw materials. In many areas, this can be done much more efficiently and sustainably. We are working on technologies for reusing and recovering residues and on solutions for more sustainable industrial heat management.
The energy chain
Valuable components can often be recovered from industry waste flows. Through the optimal use of raw materials and the reuse of waste and process flows, the cycle of industrial processes is closed. We contribute to this through the development, upscaling, and implementation of innovative technologies and systems. The emphasis is on developing key technologies such as:
- membrane separation
- adsorption
- ion exchange
- electrically powered separations such as membrane capacitive deionisation (MCDI)
More information about carbon-neutral industry
TNO’s contribution
We bring together parties such as end users, technology developers, and suppliers. The main sectors here are the chemical, food, paper, and steel industries. We have test facilities for separation and conversion technologies as well as prototype manufacturing. We are working on:
- a pilot for removing and reusing salt from process water
- nanofiltration membranes to recover valuable metals from chemical processes in an energy-efficient way
- HybSi membrane technology to dehydrate solvents from the process making them suitable for reuse
Technologies in practice
After successful lab tests and pilots, we transfer promising technologies to industry. What matters is that they are actually adopted. This is important for energy-efficient industry, and it provides opportunities for new market entrants. In this way, sustainability and new business come together.
Making heat management in industry more sustainable
Heat management should also be more sustainable. Dutch industry needs more than 500 petajoules of heat annually, for separation processes, reactions or heating of raw materials. Today, this heat comes almost entirely from fossil fuels such as natural gas, oil, and coal, while regulations, consumer demand, and cost savings demand that their processes become more sustainable. This can be achieved via three routes: process efficiency, reusing and upgrading residual heat, and a more sustainable heat supply.
1. Process efficiency
Process efficiency is the development of efficiency processes or ‘unit operations’ for application in existing and new processes. This is how we achieve major, step-by-step reductions in energy consumption. This has already led to several inventions that make industry and business more sustainable, including:
- HybSi® membrane technology for the purification of solvents
- HYSEP® hydrogen separation modules
2. Reusing and upgrading residual heat
Energy from industry enters the environment as residual heat through active cooling, flue gases or heat loss from installations. Reusing this residual heat reduces energy demand, lowers energy costs, and reduces emissions.
The challenge here is that the temperature level of the residual heat is often too low or the timing does not match demand. We are working on technologies to solve this, for example, regarding effective heat storage. Together with fellow institutes, we have also drawn the attention of the EU to the importance of heat pumps for industrial energy transition via a white paper.
Download the white paper (pdf) (pdf)
Reusing and upgrading residual heat is a little further from the heart of the process and that makes implementation easier in the short term. This solution is applicable in all industrial sectors.
3. More sustainable heat supply
Making heat supply more sustainable is the third route to making heat management in industry more sustainable. By using more renewable energy sources in heat production, the use of fossil energy sources is reduced, as are carbon emissions.
Current projects and labs
We are working on many projects in the field of efficient use of energy and raw materials and making industrial heat management more sustainable. We are also developing technologies in our labs.
Projects
- COSMOS is developing organic dissolving nanofiltration membranes on low-cost ceramic supports.
- HEADLINES (LINK) is developing heat-integrated distillation that makes innovative ethylene crackers possible.
- E-Champ, which stands for Energy-efficient Combined Heat And Mass Process, is developing and scaling up a new technology to increase the efficiency of adsorption and distillation processes.
- EuRyDice is developing energy-efficient valorisation of components from process flows, aiming at solutions for the recovery of salts and organic compounds from process flows.
- NWO Perspective research programme Microsync supports the development of efficient separation technologies and carbon membranes.
- NWO Perspective programme ReCoVR is developing new materials and coatings for electrically driven separation technologies for the recovery of valuable substances.
- The LowCapex project is developing a full-scale compression heat pump system that can produce 120-degree steam from residual heat of 60 degrees Celsius at a cost of 200 euros per Kilowatt-thermal (kWth).
- In the ENCORE project, on a somewhat smaller scale (100 kWth), we are researching how supply temperature can be increased to 180 degrees Celsius.
- The COMTA project aims to provide heat up to 200°C with a TA heat pump developed in-house.
- In the SCHP project, we are working with StandaardFasel on a prototype system for upgrading from 0.2 bar steam to 5 bar steam.
- Steam compression technology is being worked on in the SPOT project. In addition to the StandaardFasel technology, a DBS concept is also being tested.
- In the IDEA project, a sorption heat pump is being developed specifically for drying applications.
- In the FLEXSTEAM project, TNO is working on a system that stores heat compactly at 150°C.
- The SPOT project studies the application of molten salt for the storage and transport of temperatures up to approximately 600 degrees.
Labs
- Carnot lab, for the development of residual heat recovery technology
- Mollier lab, for the development of energy efficient drying & dehydration processes
- Membrane separation lab, for the development of energy-efficient membrane technology
- Combustion lab, for the development of sustainable combustion technology
Industrial decarbonization and thermal energy storage
One quarter of total final energy consumption in the European Union is consumed by industry. Within that quarter, over 80% is consumed by heating and cooling processes. The continued, wide-scale use of gas, oil, coal, and other fossil fuels for industrial thermal processes leads to an estimated greenhouse gas (GHG) emission of 513 Mt CO2 equivalent per year, 12% of total GHG emissions. Thermal energy storage (TES) can assist in the decarbonisation of industrial heating and cooling, and increase energy system flexibility and security. The full roll-out of industrial TES could enable a potential 1,793 TWh of fossil fuel replacement by renewable energy and/or surplus heat. This is one of the conclusions from the white paper “Industrial Thermal Energy Storage – Supporting the transition to decarbonise industry” by TNO and partners from the EERA Joint Program Energy Efficiency in Industrial Processes