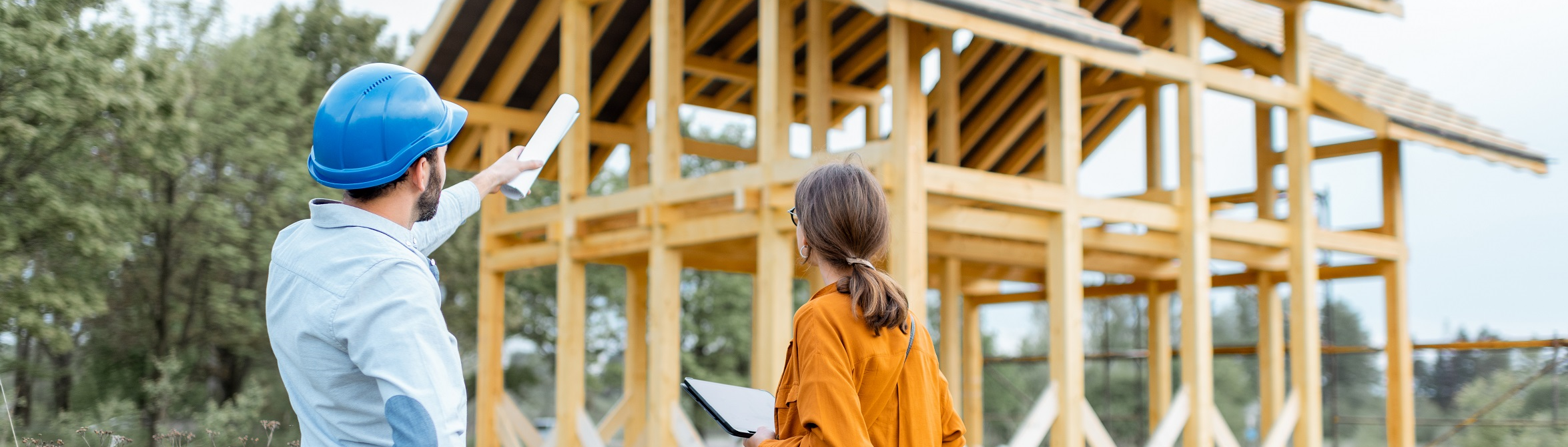
Circular construction with timber, and what’s needed for serious scaling up
Use of timber as a construction material is currently advancing rapidly, but not rapidly enough. Because timber construction is relatively new for many construction companies, there are still many questions about the application possibilities, sustainability and aspects such as noise, fire safety, connections and reuse. Together with market parties TNO intends changing that situation. The aim is to make circular construction using timber more common and on a larger scale.
“There are a number of major advantages to circular construction using timber,” says Peter Fraanje, Senior Consultant in Sustainability & Circularity at TNO. “For example, it has a low environmental impact and a building using it can store CO₂ for a long time. Innovations in timber frame construction and cross-laminated timber (CLT) are making timber a suitable option for more and more construction projects, including high-rise buildings. CLT also makes possible large-scale industrial production, which I think is a real gamechanger. And timber is often perfectly reusable a second time round. So if it’s used properly, it has multiple lives”.
'There are a number of major advantages to circular construction using timber. It has a low environmental impact and a building using it can store CO₂ for a long time.'
But as Mr Fraanje well knows, “There are still some challenges. As a builder, you must of course be aware of the possibilities and limitations of timber. It’s also important to construct the building in such a way that the timber can be easily reused afterwards. And you need to ensure that the timber used is included in the National Environmental Database, and therefore counts towards the 'Environmental Performance for Buildings' (in Dutch, the ‘MPG’).”
The challenges that Mr Fraanje mentions have one thing in common: to a large extent they can all be solved by sharing know‑how and experience. This gave him the idea to have TNO launch the 'Circular Construction with Timber' Technology Cluster.
Circular construction in practice
“We brought together seven companies that know from practical experience what’s involved in circular construction using timber. They have different backgrounds, from producers to contractors and from suppliers to architects. This creates effective interaction, and that’s precisely what we had in mind.”
Mr Fraanje explains: “Besides holding three plenary meetings, we’ll soon be visiting each of the companies. Based on their experience and questions, we can then see whether we can provide them with additional information. But it could also be that we need to carry out additional research. In turn, we at TNO are learning a lot from the participants. They’ve got some really good ideas and they can quickly put them into practice.”
Circular construction as a kind of LEGO
Maarten ten Breggen has 35 years’ experience in construction using timber. Besides his work as an architect, he now runs Maskerade, a company that has already assembled its own prefabricated timber elements for floors, walls, facades, and roofs at a large number of construction sites. His list of completed projects includes office buildings and apartment complexes.
“Our concept works like a kind of LEGO,” he explains. “In 2015, for example, we built two 75-square-metre city apartment blocks at Heijplaat in Rotterdam. People lived there for five years so that we could test how the various aspects of timber construction performed in actual practice. And then last year, we dismantled the building elements and reconstructed them as office space in the Merwedehaven district, on the other side of the river. We learned a lot from that too.
“As an architect, I’m now working with the Maskerade development team and the team at the VORM development/construction firm on a pilot project to construct a six-floor building with a total of 36 apartments in Rotterdam next year. And within three to four years, we want to scale up our construction concept and build at least a thousand housing units a year. We’re also interested in knowing how other parties are tackling these kinds of challenges – which is one of the reasons for me to be involved in this TNO initiative.”
'Why restrict the scope to timber when a lot more is possible?'
Bio-based construction
But why restrict the scope to timber when a lot more is possible? That’s also been demonstrated by Patrick Schreven of ECO+BOUW. In 2013, he started up a contracting company for timber construction and ecological building. The company has since expanded, making him a specialist in bio-based construction, not only as a contractor, but also as founder of the Knowledge Centre for Circular Construction (KCCB).
His most ambitious project so far has been construction of an eco-village in the small Dutch town of Boekel (province of North Brabant). Three round buildings made entirely of bio-based materials are currently under construction there, providing space for a total of 36 sustainable – and also affordable – homes.
“The year 2013 may not seem so long ago,” says Mr Schreven, “but back then people often used to laugh when I told them what I did, at a party for example. Insulating houses with sheep’s wool? They thought that was hilarious. But the world now looks rather different. The Paris Climate Agreement has been signed and everybody now knows how important it is to live and work in a more sustainable way. And bio-based construction can really play a big part in that. But then we do need to share the available know-how and experience properly. So it’s great that TNO has taken the initiative to bring parties together to talk about circular construction using timber, with there also being scope for exploring the possibilities of other bio-based construction materials.”
The Circular Construction with Timber Technology Cluster…
- is part of a special innovation programme in which TNO focuses on SMEs;
- involves seven participants, all of them with practical experience of circular construction using timber, namely CLT-S, Dekker, De Mar, Genius Homes, Nice Developers, Maskerade, and ECO+BOUW;
- is partly financed by the participants (a minimum of EUR 2000 per participating company) and for a large part by the Dutch Ministry of Economic Affairs and Climate Policy (project contribution of up to EUR 40,000);
- runs for six months.