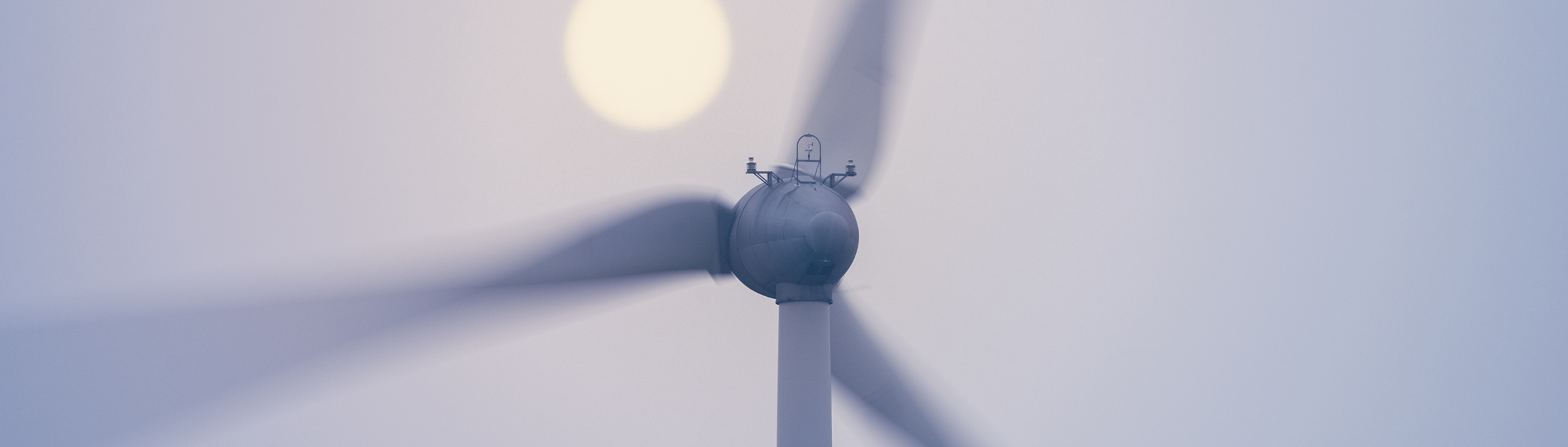
Wind turbine with 145-metre blades: reduced costs and greater efficiency
If the trend continues, wind turbines will have 145-metre blades in 2040. In the report entitled ‘Future Blades’, TNO investigates what these blades might look like but, above all, how they have to be tested and certified. Physical testing, as done currently, is almost impossible on blades of this length.
Wind turbines are increasing in size all the time and for the time being there does not seem to be any limit on how big they can become. In around 2040, they will be generating 27 megawatts, whereas the maximum is currently around 15 megawatts. The turbines of the future will have blades of 145 metres in length, approximately 35 metres longer than those of today’s largest wind turbines.
“Even longer blades mean that, with less wind, the same amount of power will be produced as the current generation of windturbines. And at high wind speeds, they will generate up to twice as much power as is currently the case”, asserts Noud Werter, who is a scientist at TNO. “So you’ll be able to construct even larger wind farms at sea, or reduce the number of wind turbines in a wind farm. That will make a considerable difference in terms of production, installation and maintenance costs. Reducing costs is an important reason for continuing to develop wind turbines and blade length.”
All aspects
In the ‘Future Blades’ report, TNO investigates all the aspects of 145-metre blades (pdf), from design and construction to production, testing and certification. Which steps have to be taken to make blades of this length possible? “Blades of this length will, for example, have to be slimmer than is currently the case, which will lead to relatively less weight and strain on the bolted connections”, explains TNO project manager Michiel Hagenbeek. “But it also means that the blade will bend more and that, in turn, will have consequences for the choice of material and construction.”
Blades which are 145 metres long also lead to practical problems when it comes to transportation. In the report, TNO investigates what is needed to produce blades in parts which will then only be assembled at the final location. This also involved an assessment of the advantages and disadvantages of various choices. Michiel Hagenbeek adds, “The tip of the blade will suffer wear and tear due to the effects of rain. If there is a lot of erosion you could, for example, opt to replace the tip after a number of years. The report investigates this and other scenarios.”
“With these blades, you will be able to construct even larger wind farms at sea, or reduce the number of wind turbines in a wind farm”
Use of 3D printing
TNO foresees that the production of blades will continue to become more and more automated. As Noud Werter explains, “The result will be fewer faults in the production process and that will take the sturdiness of the blades to a higher and more consistent level. You can, for example, automate the process of applying adhesive and finishing the blades.”
3D printing, which is a technology that is undergoing huge development, could also be used in due course. As Michiel Hagenbeek explains, “If you can print both resin and fibre with the same polymer, you will increase not only the stiffness of the blade, but also make recycling easier. After all, you will be dealing with just one type of material.” 3D printing makes it possible to use topologically optimised designs. The shape of the blade will then match the loads the structure is under, he explains. This will save weight and improve performance.
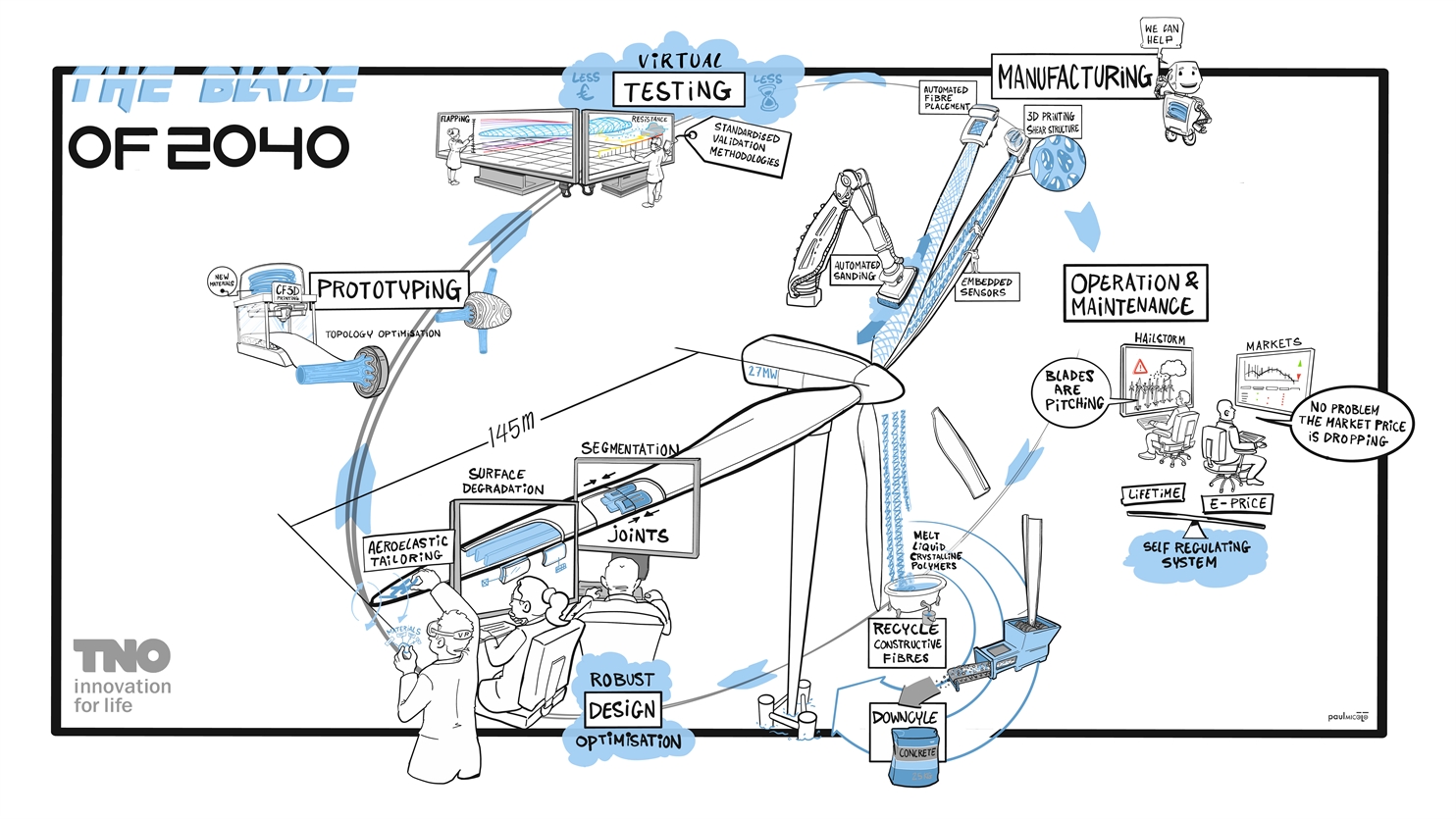
Sensors for continuous monitoring
TNO also looked at sensors in the blades. They make it possible to monitor the status of the blades continuously so that, for example, it is clear when maintenance is required. Sensors can also help blades respond to wind conditions. Michiel Hagenbeek continues, “At high wind speeds, the sensor can issue a signal which causes the turbine to relieve pressure on the blade. In this way, you can reduce wear and tear, extend the turbine’s service life and optimise the yield.”
The challenge: testing and certification
One of the challenges in 2040 will be to test and certify the 145-metre-long blades. At the moment, the robustness and expected service life of blades are tested physically. As Noud Werter explains, “Physical tests involve simulating the number of rotations that a blade makes over a period of around 30 years. That physical testing is already difficult in the case of blades which are more than 100 metres long, as is currently the case."
"You need gigantic testing locations and the tests themselves are taking more and more time. In the case of blades which are 145 metres long, it will be almost impossible to carry out fatigue testing in the traditional way. Such large testing locations simply do not exist and are extremely expensive to build. What is more, it will take even longer to simulate the number of rotations during the entire life of a blade.”
“Virtual testing is also more cost-effective because you only reinforce the components which do not do so well in the virtual test”
Virtual testing
In the ‘Future Blades’ report, TNO examines the virtual testing of 145-metre-long wind turbine blades. As Noud Werter explains, “Virtual testing means you identify variations in the blade’s properties. You break down the blade into its various components, in other words materials, construction and connections, and you test those components individually."
"This information is then integrated into an overarching model, thereby eliminating the need to test the blade as a whole. In the report we show – and we also know this from previous research – that this leads to a more accurate picture of the robustness of the total blade and the expected service life. It is also more cost-effective because you only reinforce the components which do not do so well in the virtual test.”
Michiel Hagenbeek adds, “One of the major benefits is that the part tests produce different values. The computer model therefore shows the bandwidth within which all blades produced in the future will fall. So virtual testing does not just tell us something about a single wind turbine blade – as current tests do – but about all wind turbine blades which are designed, constructed and produced in the same way. That makes certification easier.”
145-metre-long blades certainly possible
Virtual testing resolves the problem of the physical testing of 145-metre-long blades being virtually impossible in practice. It also means a new type of blade design can be brought to the market faster and more cheaply. As Noud Werter and Michiel Hagenbeek clarify:
“Technology still has a few more steps to take. In ‘Future Blades’, we explain which steps we believe are necessary. We think it is certainly possible to produce wind turbine blades which are 145 metres long. We also show that virtual testing leads to more reliable blade designs and can help resolve practical problems. We’re working hard on the virtual testing concept so that it can be validated as soon as possible.”
Want to find out more?
Contact Michiel Hagenbeek.
Get inspired
New UWiSE module for efficient offshore wind farm decommissioning
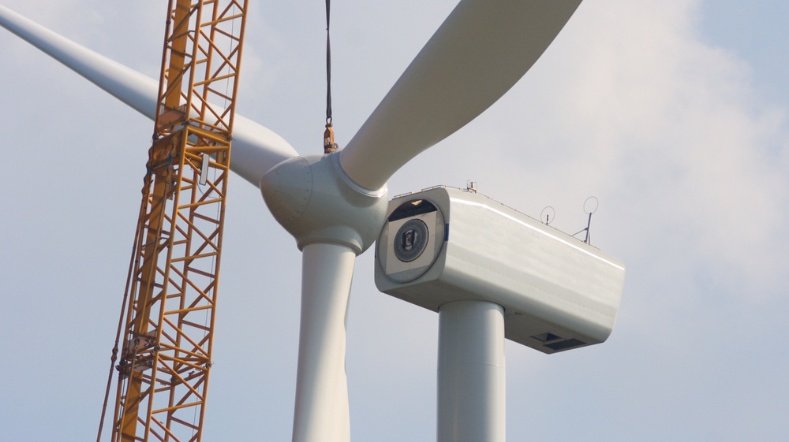
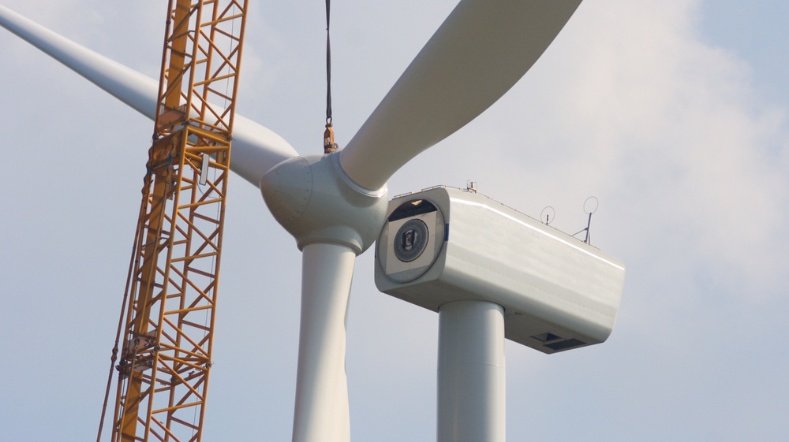
Wind turbine inspections with autonomous drones and digital twin modelling
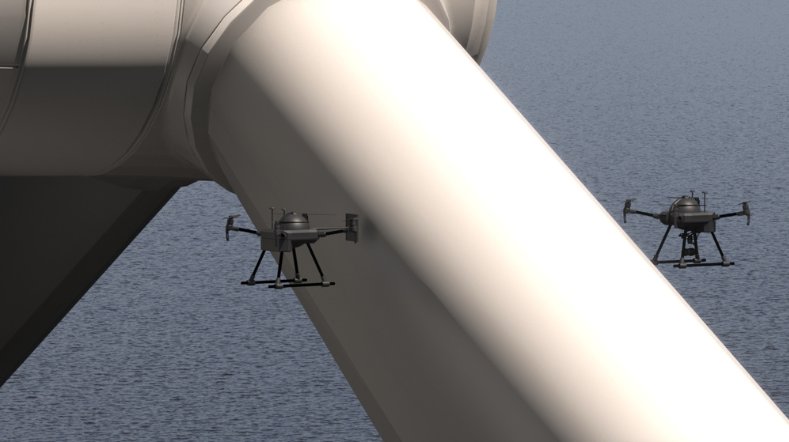
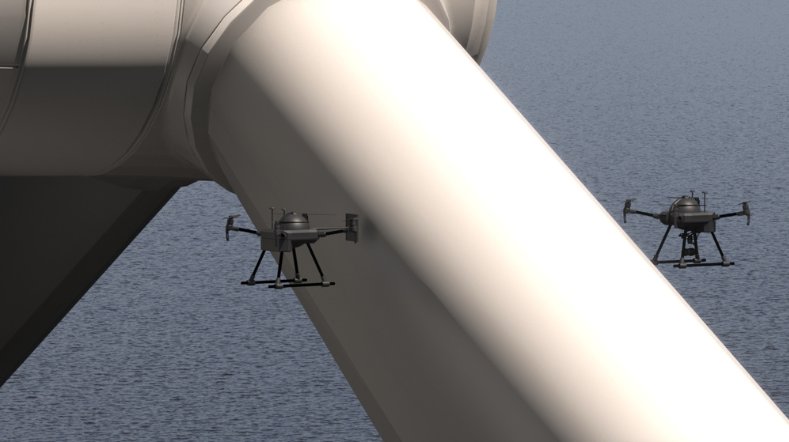
Profitability offshore wind in 2030 not self-evident
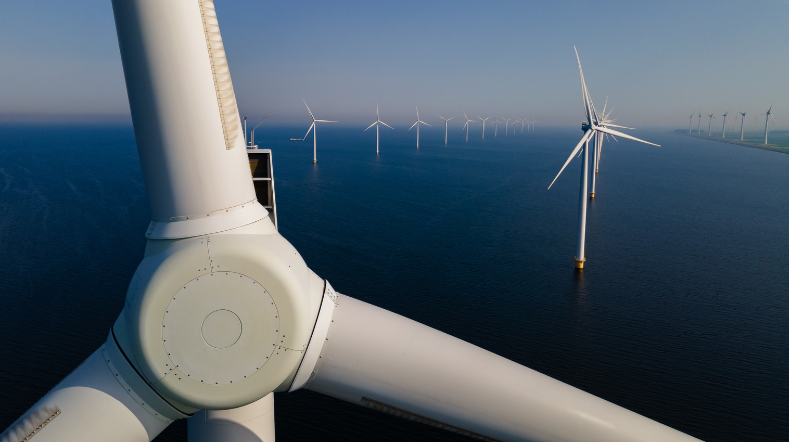
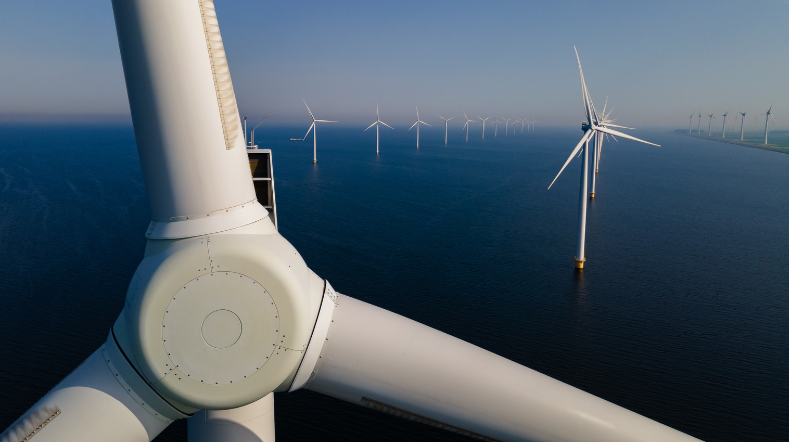