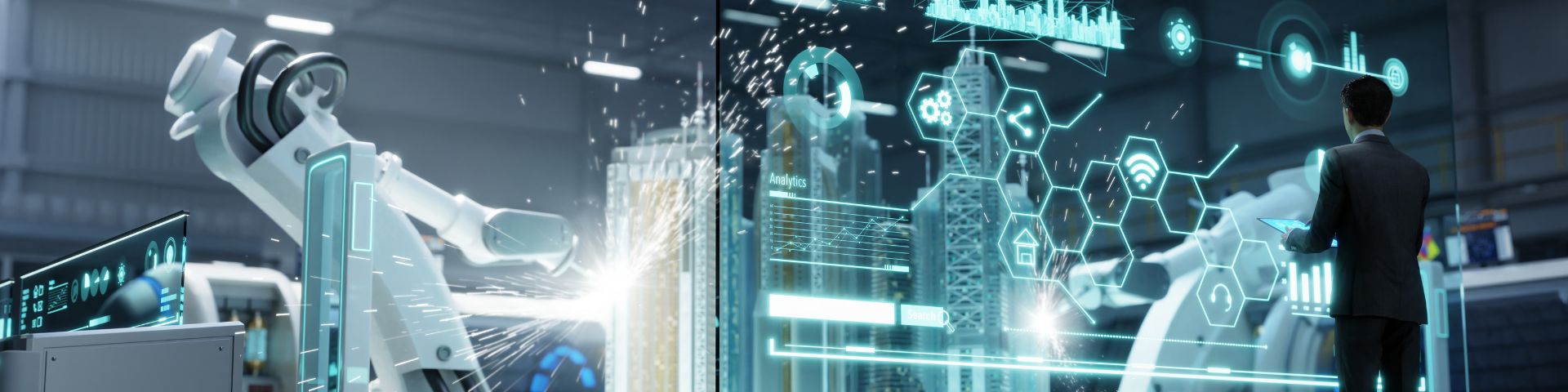
Digital Twins in practice: they’re very versatile, but what do you really need?
A Digital Twin lets you see exactly what happens inside a device before you’ve even made it. This enables you to eliminate errors from your prototype earlier, create more complex schedules, give your technician more precise direction, and know exactly how to manufacture the product – all examples of Digital Twins in a factory. Flemish company RheaVita develops unique freeze-drying equipment for the pharmaceutical industry and it improved its Digital Twin together with TNO.
Complex freeze-drying process
When RheaVita called on TNO for help in developing a Digital Twin, it soon became clear that the company already had a good idea of why this was needed. The freeze-drying equipment it develops and produces is becoming increasingly sophisticated. To take that technology to an even higher level, it had developed a process in which all the water evaporates and only the important material remains. The result is nice and light, and therefore easy to transport. And the material can also be stored for much longer. So there are many advantages, but it is a complicated process that requires many steps and everything has to work correctly to ensure those advantages are achieved.
‘Before creating a prototype, the experts at RheaVita wondered whether they could skip some prototype steps by using a software-based solution,’ says Jeroen Broekhuijsen, business consultant Digital Factory at TNO. ‘They envisioned a digital tool that not only controls the machine, but can also indicate the right process settings and recipes for different products. A Digital Twin would lend itself very well to that.’
Organisational aspects
‘The biggest challenge is that many manufacturing companies quickly lose themselves in technology during the exploration phase,’ says Broekhuijsen. ‘In their enthusiasm, they then often want to implement all the features of Digital Twins at once. But that isn’t realistic. The key question is what they will use that technology for. What is the goal? And what level of accuracy is needed for that purpose? It often turns out that a simpler version of a Digital Twin will suffice.’
Introducing a Digital Twin requires a different way of working. ‘This is actually many times more important than the technical solution,’ Broekhuijsen stresses. ‘Due to the fact that everyone tends to focus on the technology, you often see a Digital Twin initiative foundering, as too little attention was paid to the organisational aspects.’ Eventually, an employee from the company is going to be working with the results of the Digital Twin, so it is important to know first who that will be, what they will then need, and how it will change their employee’s work.
To avoid such pitfalls, TNO uses a seven-step model in Digital Twin projects based on three key questions:
1. WHY - What is the goal? What is the scope? And what is already there?
2. HOW - How do we make the technology applicable within our business? How do we make the Digital Twin operational? How do we evaluate, update, and improve our Digital Twin?
3. WHAT - This is where the real replica is made.
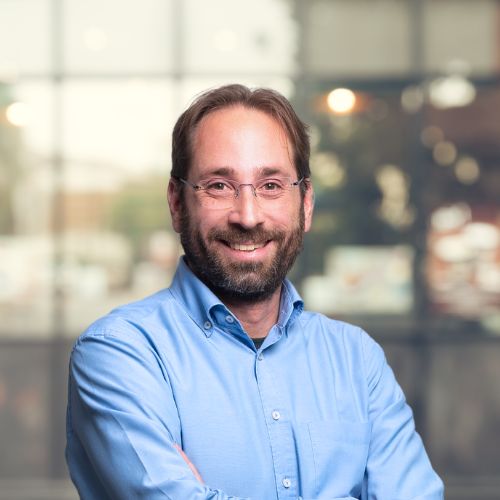
‘A Digital Twin is more than a replica; it offers new insights to optimise processes and devices. Startups, scale-ups, and SMEs in particular can benefit from this technology, but its effective implementation is challenging for these companies.’
Priorities
The biggest challenge was getting different parties to work well together. Indeed, up to the time of the collaboration, these were still fairly separate worlds. This immediately became clear when one of the companies involved made a visualisation of the machine. ‘It looked great,’ says Broekhuijsen, ‘but it didn’t contain any knowledge of the freeze-drying process. As a result, you could see how the device works, how you can control it and what you can do with it, but not exactly what is needed to freeze-dry a specific product the right way, which parts of the device are involved, and how to control those parts correctly.’
It takes considerable thought to determine which process parameters are important and which parties should provide which information to gain a good picture of the whole. Broekhuijsen explains: ‘Actually, it’s a hopeless task to do it all at once. For RheaVita, we looked at which option was really a priority. We then looked at what step we could take in that area and what value that would bring. In this way, we came up with a number of alternatives that were clearly feasible. We’ve now reached the point where we have an information model that enables us to improve the performance of a prototype freeze-drying machine. With the simulation of that machine, we can not only see on a computer screen how it works, but also check whether the operation deviates from what the information model predicted.’
What’s next?
The next step? ‘The Digital Twin now working for the prototype can also be supplied along with the machines RheaVita supplies to customers. In doing so, it would be even better if we could use the Digital Twin to indicate, based on various scenarios, exactly where something is going wrong and what the solution is. But that’s an even bigger step. RheaVita has laid the foundation to continue building and to start reaping the benefits of a Digital Twin.’
The Digital Twin is a crucial element for valorising the power of the available data in the production process and the final product through the use of all kinds of future AI applications. By focusing now on a solid framework from which data can be easily accessed, a manufacturing company will be able to quickly integrate new disruptive digitalisation applications. For example, improving its manufacturing throughput and quality with improved planning and the use of existing production facilities. An insight will often immediately result in an improvement in productivity, so that non-value-added steps can be quickly improved using the well-known lean manufacturing method. It also makes it easier to link future operator support systems, such as automatically generated work instructions, to the existing business automation. This additionally creates the possibility of sharing the data from the digital twin in the value chain, from the supplier and service provider to the end customer. In short, digital twinning is a crucial element in building the future earning capacity of a manufacturing company, large or small.
Standardisation
One way to make a Digital Twin accessible to smaller companies is to use European and other standards, with which larger organisations have defined how a Digital Twin works and what the best practice is. As a consultant, Broekhuijsen is actively involved in these standardisation organisations and helps to establish this best practice. Europe is increasingly focusing on Digital Twins, which is making it ever clearer how to link data, simulations, and the business process. Examples include ‘ISO 23247 - Digital Twin Framework for manufacturing’, with which a Digital Twin is made modular and which clarifies how parts should be linked.
In addition, Germany’s Platform Industrie 4.0 has produced the ‘Asset Administration Shell’ that describes what information a Digital Twin of a device can contain and where a standard interface is agreed upon that a device should have in order to connect universally to devices. In combination with the OMG Digital Twin Consortium’s ‘Digital Twin Capabilities Periodic Table’, it is then possible to set priorities, create a roadmap, and compile an overview of the information needed to achieve the goal. This approach has been developed by the EU project Change2Twin, in which 30 SMEs in Europe have created a first Digital Twin for their manufacturing company. This provides a structure in which you can clearly describe what production data you need, what the result looks like in a dashboard, whether you can capture the behaviour of the device in Machine Learning (AI), or whether you can link the twin with your factory planning, and you can plot this functionality over time, enabling the business case to be continually extended.
Get inspired
Japanese DNP opens Dutch R&D hub in partnership with TNO
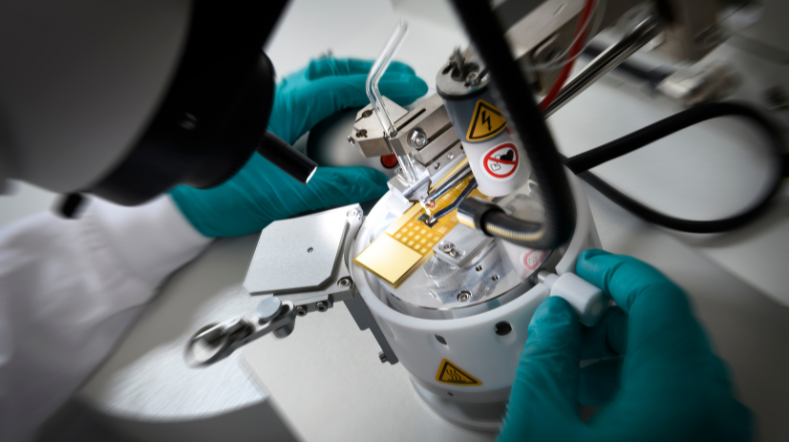
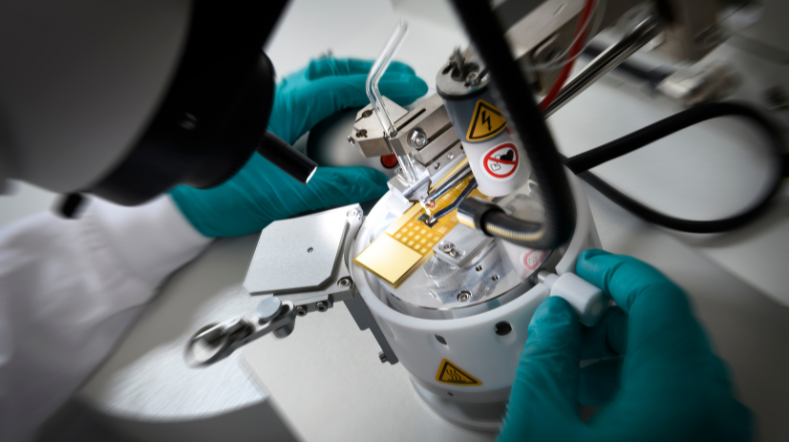
Dutch partners announce construction of climate satellite TANGO
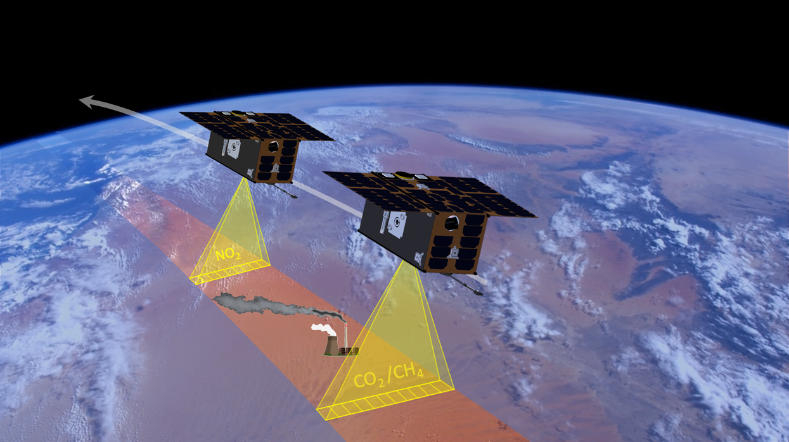
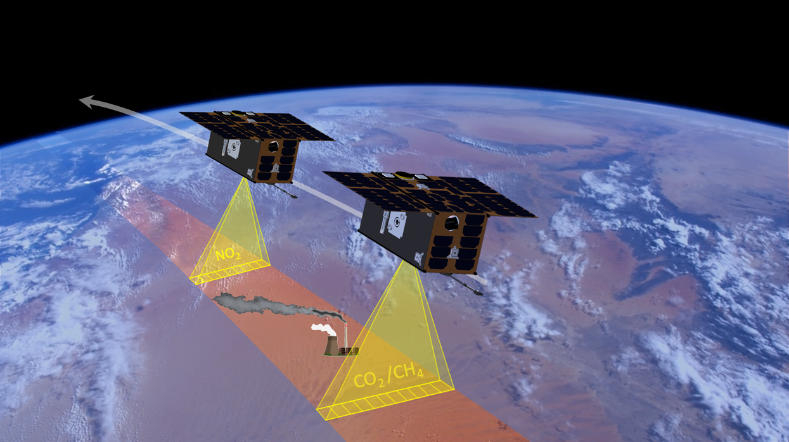
SEAMIIC: Autonomous parts handling and quality control
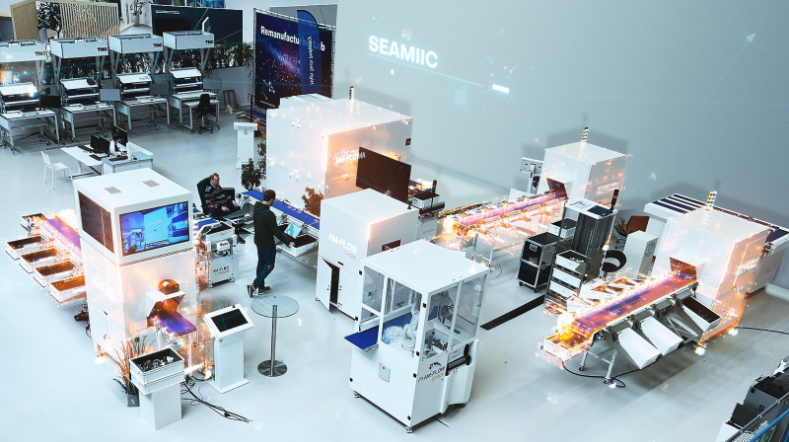
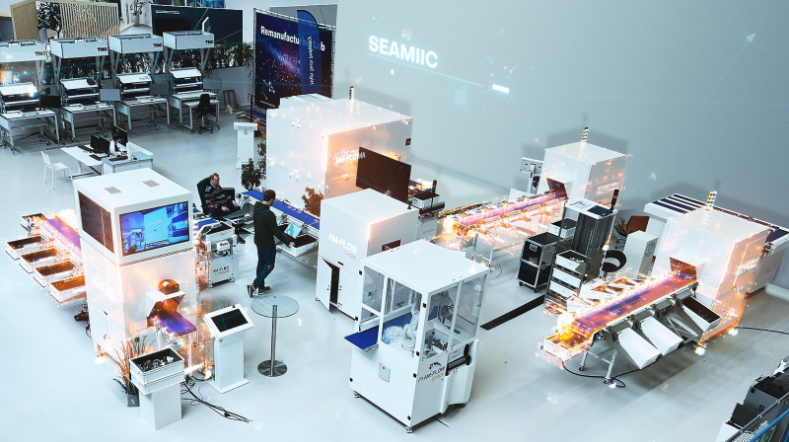
TNO: Megaclusters to create new tech champions
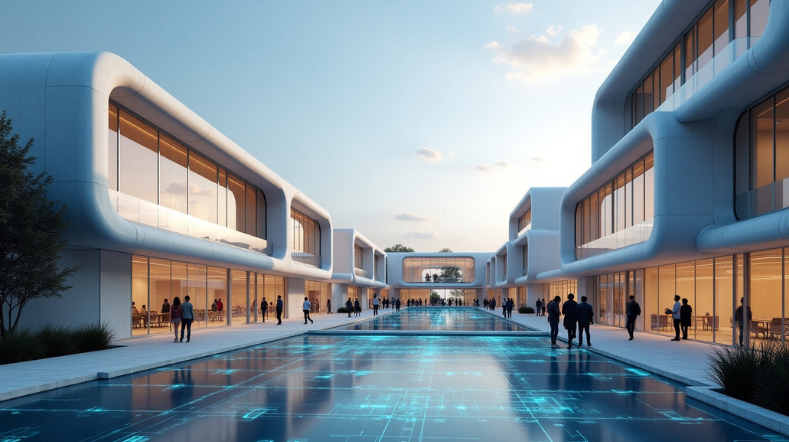
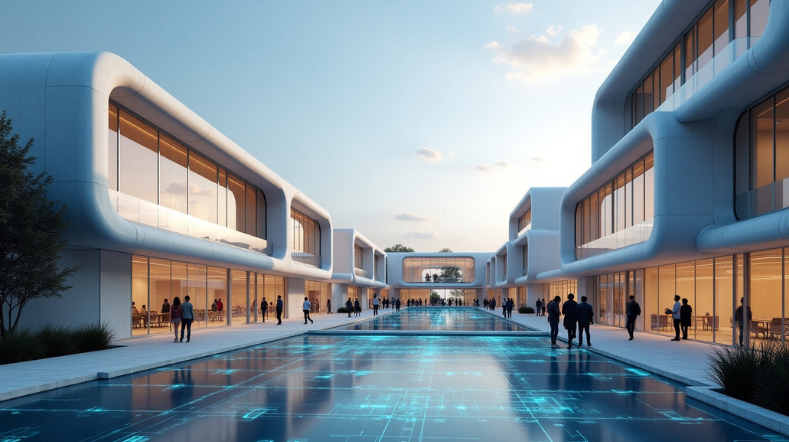
TNO and Jungle AI collaborate to detect cyberattack on wind turbine and improve detection capabilities
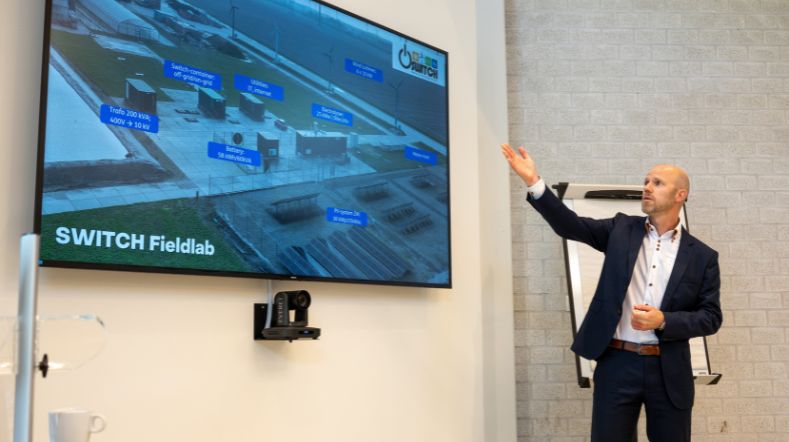
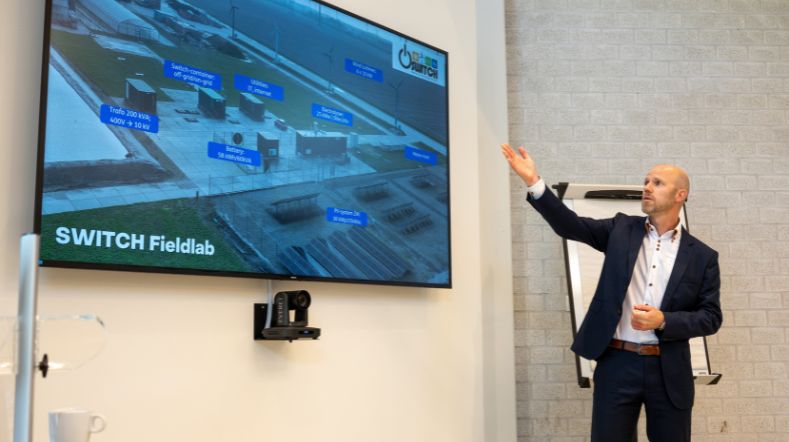