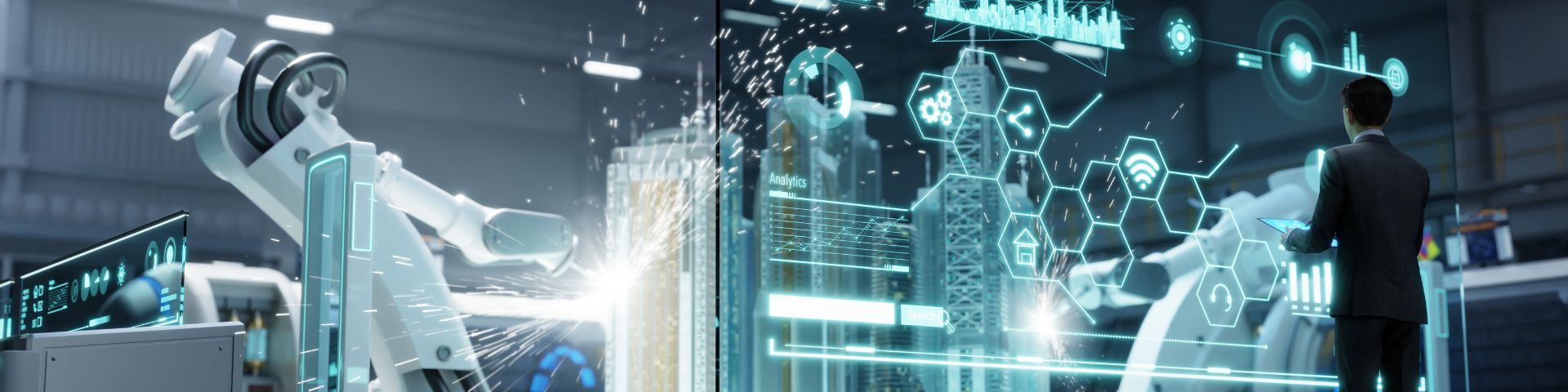
Digital Twins in de praktijk: er kan veel, maar wat heb je écht nodig?
Precies zien wat er in het apparaat gebeurt terwijl je deze nog niet eens gemaakt hebt? Dat kan met een Digital Twin. Zo kun je eerder fouten uit je prototype halen, complexere planningen maken, gerichter je monteur op pad sturen en precies weten hoe je het product moet produceren; allemaal voorbeelden van Digital Twins in een fabriek. Het Vlaamse Rheavita ontwikkelt unieke vriesdroogapparatuur voor de farmaceutische industrie en verbeterde met TNO haar Digital Twin.
Complex vriesdroogproces
Toen RheaVita bij TNO aanklopte met de vraag om te helpen bij het ontwikkelen van een Digital Twin, bleek al snel dat zij al een goed beeld hadden van het waarom. De vriesdroogapparaten die zij ontwikkelen en produceren worden steeds geavanceerder. En om die technologie naar een nog hoger niveau te tillen, hadden zij een proces ontwikkeld waarbij al het water verdampt en alleen het belangrijke materiaal overblijft. Lekker licht, dus makkelijk te vervoeren. Daarbij is het veel langer houdbaar. Veel voordelen dus. Maar het is wel een ingewikkeld proces waar veel stappen voor nodig zijn en waarbij alles goed moet gaan om de voordelen te kunnen garanderen.
“Voordat ze een prototype gingen maken, vroegen de experts bij RheaVita zich af of ze een aantal prototypestappen zouden kunnen overslaan door gebruik te maken van een softwarematige oplossing”, weet Broekhuijsen. “Ze zagen een digitale tool voor zich die de machine niet alleen aanstuurt, maar die ook voor verschillende producten kan aangeven wat de juiste procesinstellingen en recepten zijn. Een Digital Twin zou zich daar heel goed voor lenen.”
Organisatorische aspecten
“De grootste uitdaging is dat veel maakbedrijven zich tijdens het oriënteren al snel in de techniek verliezen”, weet Jeroen Broekhuijsen, business consultant Digital Factory bij TNO. “In hun enthousiasme willen ze dan vaak alle mogelijkheden van Digital Twins in één keer doorvoeren. Maar dat is niet realistisch. De belangrijkste vraag is waar ze die technologie voor gaan gebruiken. Wat is het doel? En welke mate van nauwkeurigheid is daarvoor nodig? Vaak blijkt dan dat een simpelere versie van een Digital Twin dan al volstaat.”
Het invoeren van een Digital Twin vraagt om een andere manier van werken. “Die is zelfs vele malen belangrijker dan de technische oplossing”, benadrukt Broekhuijsen. “Doordat iedereen de neiging heeft om zich op de techniek te richten, zie je vaak dat een Digital Twin-initiatief strandt omdat er te weinig aandacht was voor de organisatorische aspecten.” Uiteindelijk gaat een medewerker uit het bedrijf aan de slag met de resultaten van de Digital Twin, het is belangrijk om eerst te weten wie dat is, wat die medewerker dan nodig heeft en hoe dat het werk van die medewerker gaat veranderen.
Om dit soort valkuilen te voorkomen, hanteert TNO bij Digital Twin-projecten een zeven stappen model gebaseerd op drie basis vragen:
1. WAAROM - Wat is het doel? Wat is het toepassingsgebied? En wat is er al?
2. HOE - Hoe maken we de technologie binnen onze business toepasbaar? Hoe krijgen we de Digital Twin operationeel? Hoe evalueren, updaten en verbeteren we onze Digital Twin?
3. WAT - Hier wordt de echte replica gemaakt
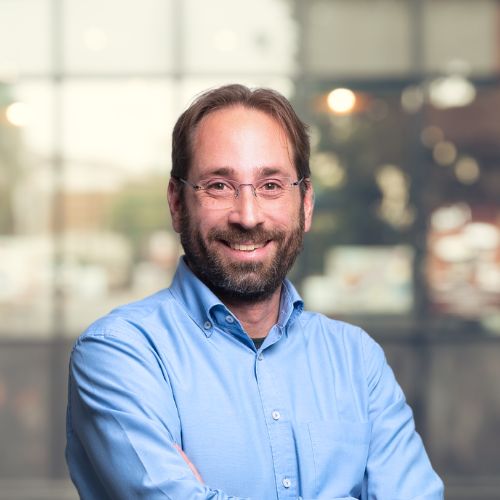
“Een Digital Twin is meer dan een replica, het biedt nieuwe inzichten om processen en apparaten te optimaliseren. Juist startups, scale-ups en het mkb kunnen profiteren van deze technologie, maar de doeltreffende implementatie ervan vormt voor deze bedrijven een uitdaging."
Prioriteiten
De grootste uitdaging was om verschillende partijen goed met elkaar te laten samenwerken. Tot die tijd waren dat namelijk nog redelijk gescheiden werelden. Dat werd meteen al duidelijk toen een van de betrokken bedrijven een visualisatie van de machine had gemaakt. “Die zag er top uit,” zegt Broekhuijsen, “maar er zat geen kennis van het vriesdroogproces in. Dus je zag wel hoe het apparaat werkt, hoe je hem kan aansturen en wat er je ermee kan doen, maar niet wat er precies nodig is om een specifiek product op de juiste manier te vriesdrogen, welke onderdelen van het apparaat daarbij betrokken zijn en hoe die onderdelen op de juiste manier moeten worden aangestuurd.”
Er is aardig wat denkwerk voor nodig om te bepalen welke procesparameters van belang zijn en welke partijen welke informatie moeten aandragen om een goed beeld van het geheel te krijgen. Broekhuijsen: “Eigenlijk is het onbegonnen werk om dat allemaal in één keer te doen. Voor RheaVita hebben we gekeken welke optie echt prioriteit heeft. Vervolgens keken we welke stap we op dat vlak konden maken en welke waarde dat dan op zou leveren. Op die manier zijn we op een aantal varianten gekomen waarvan duidelijk was dat die haalbaar waren. Inmiddels zijn we zover dat we een informatiemodel hebben waarmee we de performance van een prototype van een vriesdroogmachine kunnen verbeteren. Met de simulatie van die machine kunnen we niet alleen op een computerscherm zien hoe hij werkt, maar ook checken of de werking afwijkt ten opzichte van wat het informatiemodel voorspeld had.”
What’s next?
De volgende stap? “De Digital Twin die nu voor het prototype werkt ook mee te leveren met de machines die RheaVita aan klanten levert. Daarbij zou het helemaal mooi zijn als we de Digital Twin kunnen inzetten om op basis van verschillende scenario’s precies aan te kunnen geven waar iets misgaat en wat de oplossing daarvoor is. Maar dat is een nog veel grotere stap. RheaVita heeft de basis gelegd om verder te kunnen door bouwen en de voordelen van een Digital Twin te gaan benutten.”
De Digital Twin is een cruciaal element om de kracht van de aanwezige data van het productieproces en het eindproduct tot waarde te kunnen brengen door het gebruik van allerlei toekomstige AI-applicaties. Door nu in te zetten op een gedegen framework van waaruit data eenvoudig ontsloten kan worden ben je als onderneming in de maakindustrie in staat om snel nieuwe disruptieve digitaliseringsapplicaties te integreren. Denk daarbij aan het verbeteren van je manufacturing througput en kwaliteit met een verbeterde planning en benutting van de bestaande productie faciliteiten. Vaak resulteert het inzicht direct in een verbetering van de productiviteit zodat niet waarde toevoegde stappen met de wel bekende lean manufacturing werkwijze snel verbeterd kunnen worden. Ook wordt het hiermee makkelijker om toekomstige operator support systemen zoals automatisch gegeneerde werkinstructie eenvoudiger te koppelen aan de bestaande bedrijfsautomatisering. Daarbij ontstaat dan ook de mogelijkheid de data vanuit de digital twin te gaan delen in de waardeketen van leverancier, service provider tot aan de eindklant. Kortom digital twinning is een cruciaal element om te bouwen aan het verdienvermogen van de toekomst van een maakbedrijf, groot of klein.
Standaardisatie
Eén van de manieren om een Digital Twin toegankelijk te maken voor kleinere bedrijven is gebruik te maken van (Europese) standaarden waarbij grotere organisaties hebben vastgelegd hoe een Digital Twin werkt en wat de beste manier van werken is. Als consultant is Broekhuijsen actief betrokken bij deze standaardisatie organisaties en helpt hij mee om deze beste manier van werken vast te leggen. Vanuit Europa is er steeds meer aandacht voor Digital Twins zodat steeds duidelijker wordt hoe je data, simulaties en het bedrijfsproces met elkaar kunt koppelen. Voorbeelden hiervan zijn de “ISO norm 23247 – Digital Twin Framework for manufacturing” waarmee een Digital Twin modulair gemaakt wordt en duidelijk wordt hoe onderdelen gekoppeld moeten worden.
Daarnaast is er vanuit Platform Industrie 4.0 uit Duitsland de “Asset Administration Shell” die beschrijft welke informatie een Digital Twin van een apparaat kan bevatten en waar een standaard interface wordt afgesproken die een apparaat zou moeten hebben om universeel met apparatuur te verbinden. In combinatie met het “Digital Twin Capabilities Periodic Table” van het OMG Digital Twin Consortium kan dan geprioriteerd worden, een roadmap gemaakt worden en een overzicht van de informatie die nodig is voor het doel opgesteld worden. Deze aanpak is ontwikkeld vanuit het EU project Change2Twin waarbij 30 MKB bedrijven in Europa een éérste Digital Twin hebben ontwikkeld voor hun maakbedrijf. Zo is er een structuur waarin je goed kunt beschrijven welke productiedata je nodig hebt, hoe het resultaat er uit ziet in een dashboard, of je het gedrag van het apparaat in Machine Learning (AI) kunt vangen of dat je de twin kunt koppelen met je fabrieksplanning en kun je deze functionaliteit uitzetten in de tijd waarbij de business case steeds uitgebreid kan worden.
Neem contact met ons op
Laat je inspireren
SEAMIIC: Autonome handling van onderdelen en kwaliteitscontrole
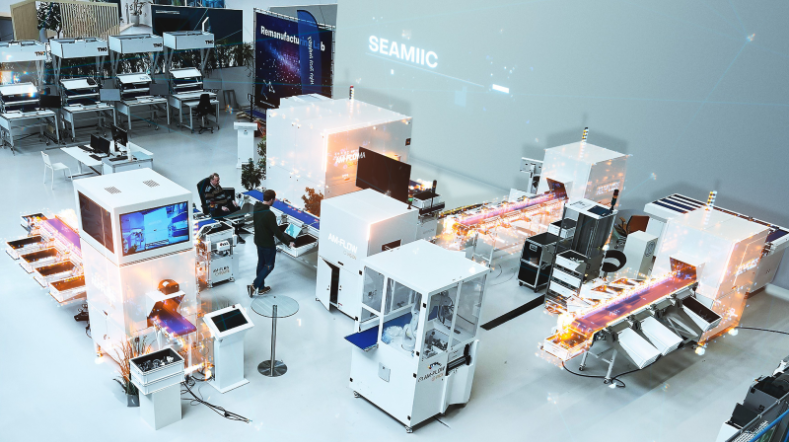
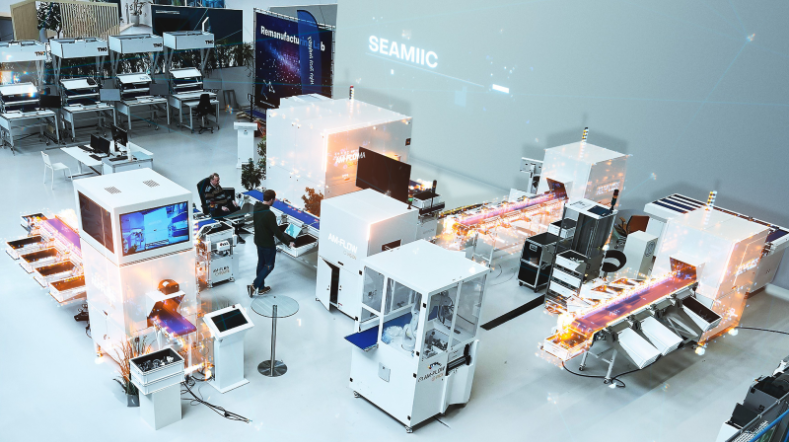
Samenwerken voor wederzijdse vooruitgang
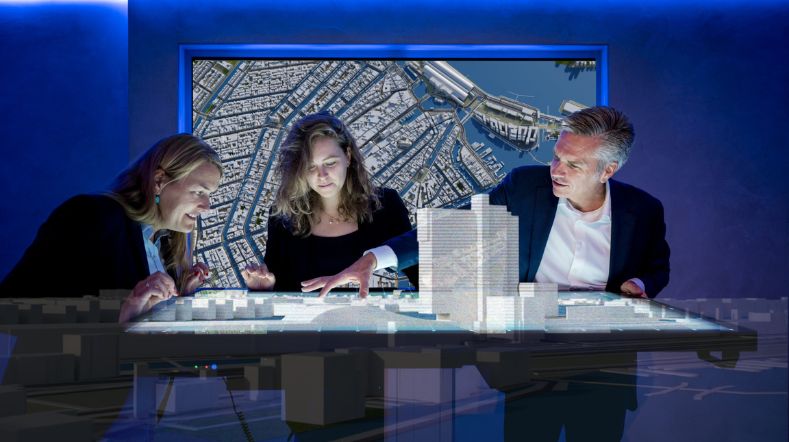
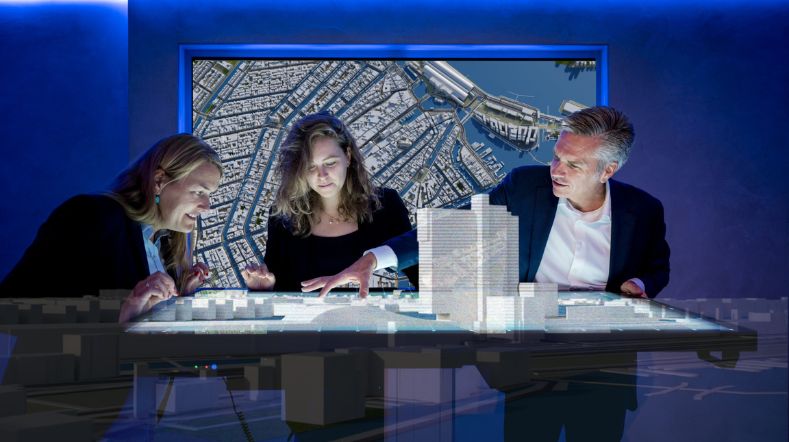
Naar circulair ondernemen met het Digitaal Product Paspoort
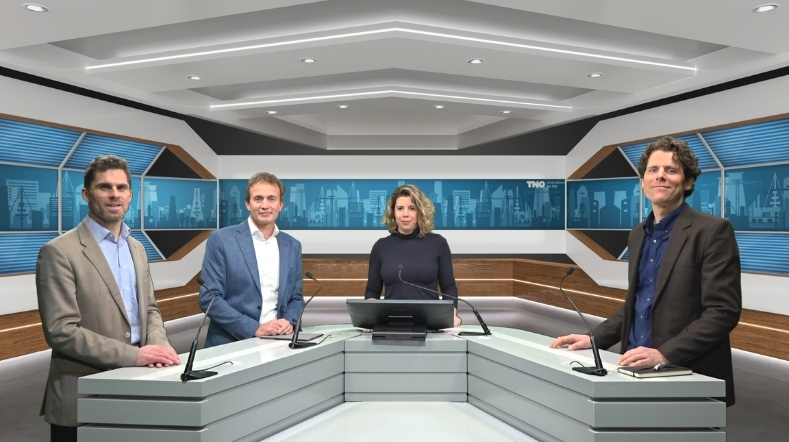
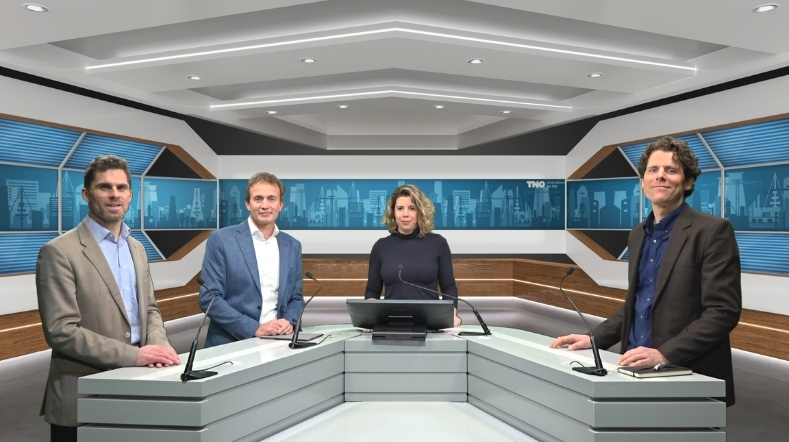
Nieuwe TNO spin-off Scenexus haalt investering van 1,6 miljoen euro op
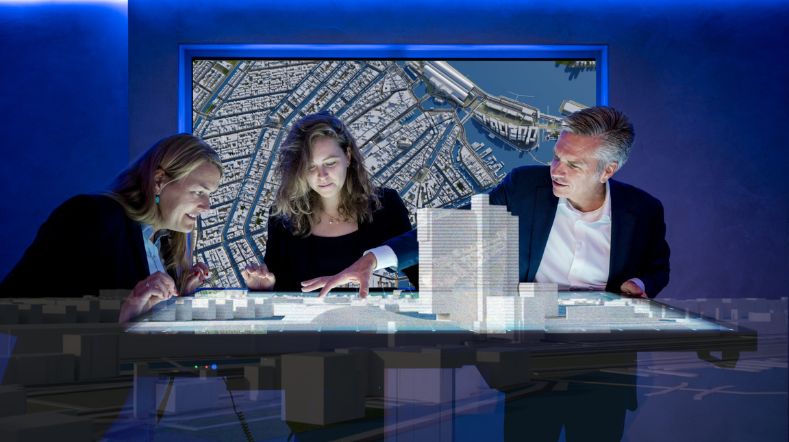
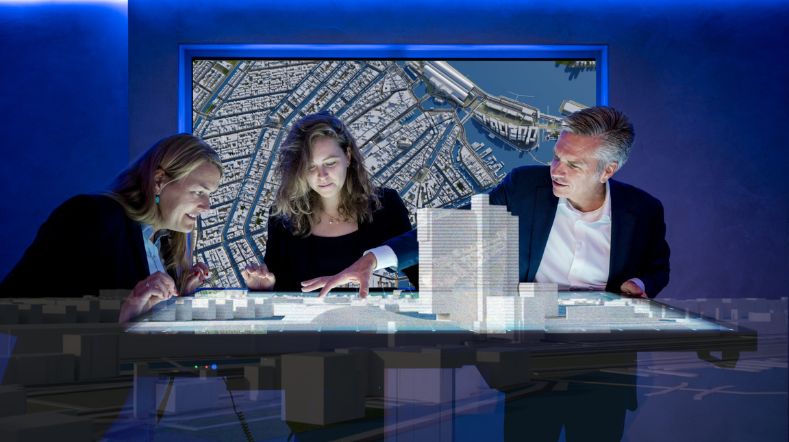
Scale up: manufacturing throughput and quality
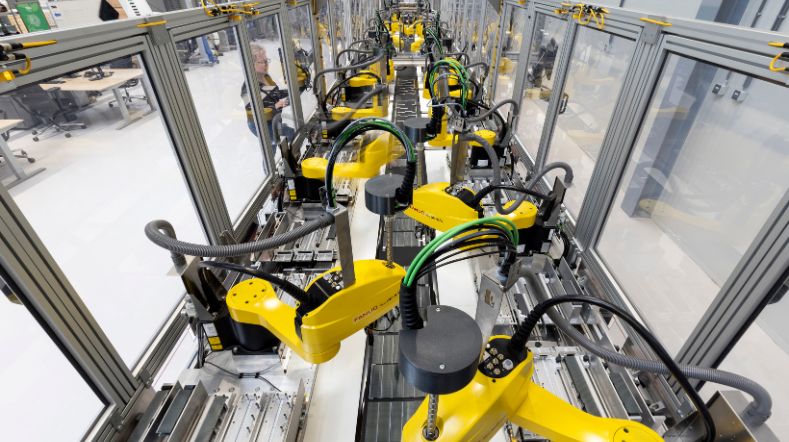
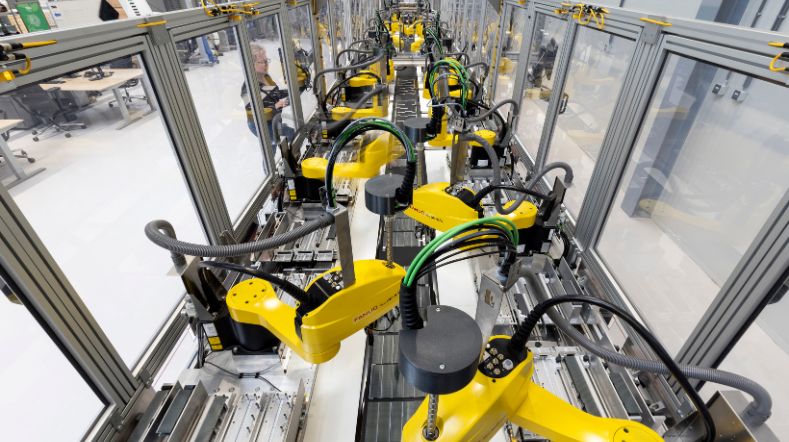