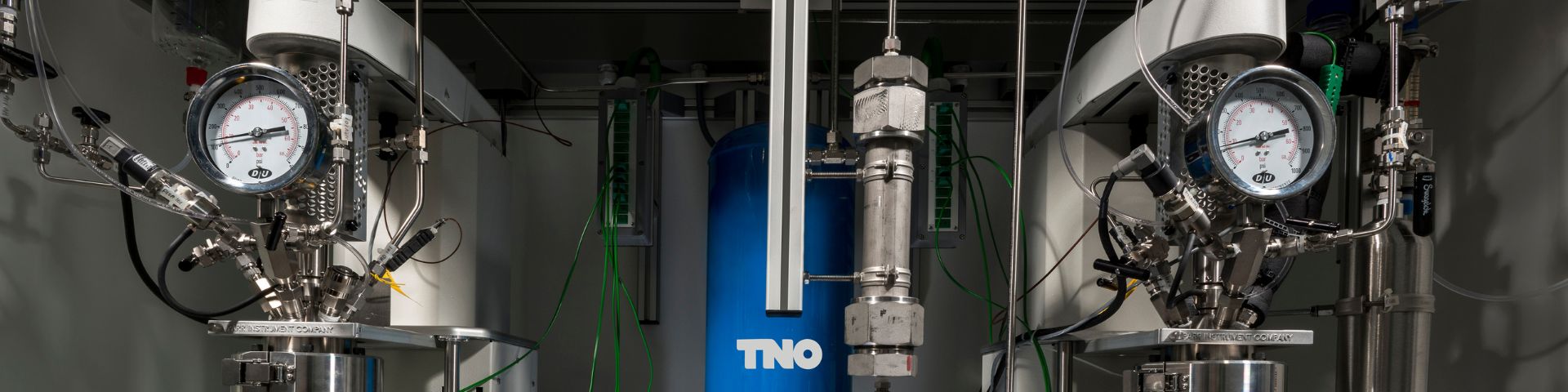
Application of dissolution to recycle ABS plastics in a circular way
Developing technologies for a circular future is at the heart of our sustainability strategy at TNO. It’s the reason we’ve set ourselves a goal to produce half of all plastics circularly by 2030 – and we’re working towards that target in many different ways. To accelerate implementation, we are currently working with ABS producer ELIX Polymers where we are exploring the applicability of the process for recycling ABS polymers (Acrylonitrile, Butadiene, Styrene) derived from end-of-life electronics.
One area of innovation is plastics recycling technologies. Improving recycling processes is key to addressing the alarming growth of plastic waste. Furthermore it will lower our dependence on oil to produce plastics, and reduce unacceptable levels of CO2 emissions – and we’ve already made exciting developments.
The crux of the dissolution process
With dissolution, a physical recycling technology that utilises solvents to dissolve post-consumer plastics, polymers can be recovered that are of superior quality than the recyclate from mechanical recycling.
At the same time it has a higher material efficiency and requires less energy than chemical recycling. Put simply, it’s because the polymer remains intact throughout the process, rather than being broken down into monomers at high temperatures.
The topic has long been an area of exploration for TNO Senior Scientist, Mark Roelands. An expert in process integration, separation technologies and solvent-based plastics recycling.

"We found that using a lower boiling temperature facilitates evaporation and recovery of solvents, which speeds up the dissolution process and saves costs."
In fact, we have identified multiple benefits, as Mark explains. ‘We found the energy consumption and cost in the dissolution process is largely in solvent recovery and polymer drying. A low boiling temperature makes it easier to evaporate and recover our solvent, speeding up the process.
‘As well as this, we achieve a polymer solution with a low viscosity, which enables the use of conventional separation technologies.’ In this way, TNO was able to achieve favourable process economics in terms of energy consumption, efficiency of polymer recuperation, and effective decontamination.
TNO and ELIX Polymers forge sustainable solutions
We collaborate with several equipment manufacturers for different adjacent process applications, allowing us to scale up faster.
One example of a partnership that has produced exciting results is TNO’s work with ELIX Polymers, a leading manufacturer of ABS (Acrylonitrile-Butadiene-Styrene) resins and derivatives in Europe. Toni Prunera Casellas, head of business development and R&D at ELIX, explains how the partnership began.
‘We worked with TNO on Plast2beCleaned, a project where the main objective was to recover polymers as well as the flame-retardant additives from WEEE. So, we looked to find a way to recover a material - the ABS- that was of high enough quality to be recycled in a new product.’ In fact, multiple partners were involved in the project to find ways to recover the 3 recyclates produced via the dissolution process, polymers, antimony trioxide, and brominated flame retardants.
And the collaboration with ELIX has been a catalyst for new projects. ‘We’re now focusing on the polymer itself and how effectively we can remove pollutants of that ABS – not just from electronic waste but also from old automotives – by eliminating the pigment and other additives, for example.’
Cooperation from raw material supplier to end-user
It’s through these partnerships that technologies like dissolution can evolve at a more rapid pace, and the opening of the pilot plant in Rijswijk will allow even more opportunities for collaboration. Mark explains:
‘As a not-for-profit organisation, it’s not about competing, but collaborating – bringing our expertise together towards a common goal. ELIX already has an ABS plant and provided the domain knowledge of ABS at the start of the project. At TNO we have the expertise and the facilities in the field of dissolution and decontamination. To this end, we also work closely with the research institute Fraunhofer ICT, which is developing technology to remove dissolved impurities.
‘By working together, we were able to recover ABS – among other things – that was recompounded with fresh ABS by Electrolux to produce a washing machine part. That’s a great value-chain project example – all the way from the waste collector to the end-user, and including the virgin-grade producer, too.’
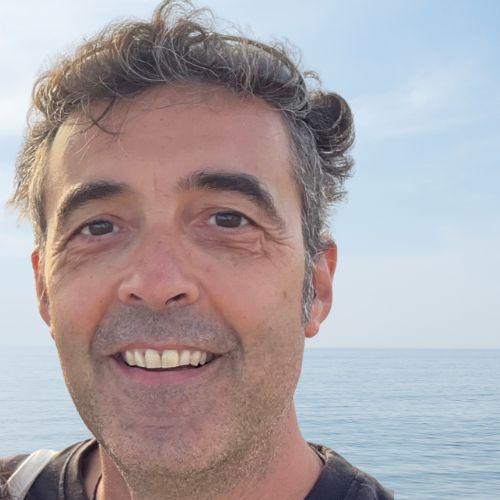
"Together with TNO, we see dissolution as one of the key recycling technologies of the future, a future where plastics are circular"
Closing the loop on plastics
Looking ahead to the future, dissolution is an area of focus for ELIX. ‘It is one of the key recycling technologies of the future, and we know TNO share that view,’ says Toni. ‘The circular economy concept is based on finding the shortest loops possible. Dissolution, by retaining the polymer structure rather than using a chemical or thermochemical process to get to monomer stage, helps us to close that loop.’
For Mark, fractionization will be the next challenge on the horizon. In June this year, we plan to open a pilot plant in the western part of the Netherlands, this will enable further research. ‘As well as looking at removing pigments and flame retardants we want to look at removing the rubber particles in ABS, for example, so we can replace them with fresh ones and rejuvenate the ABS. But that’s 2025 – decontamination is my focus for 2024!’
TNO are keen to hear from potential new partners who can benefit from these technologies. In Mark’s words, ‘Fundamentally we ask ourselves: where can this technological advancement land? Which partners and international parties can we connect with, who can then take over and apply this activity, and commercialise it?
‘From emerging start-ups to established international companies, we’re looking for partners with the same goal in sight: a future where plastics are circular.’
Want to find out how TNO can work with your business on recycling technologies?
Get inspired
Early results show the potential of circular healthcare plastics


Biobased materials
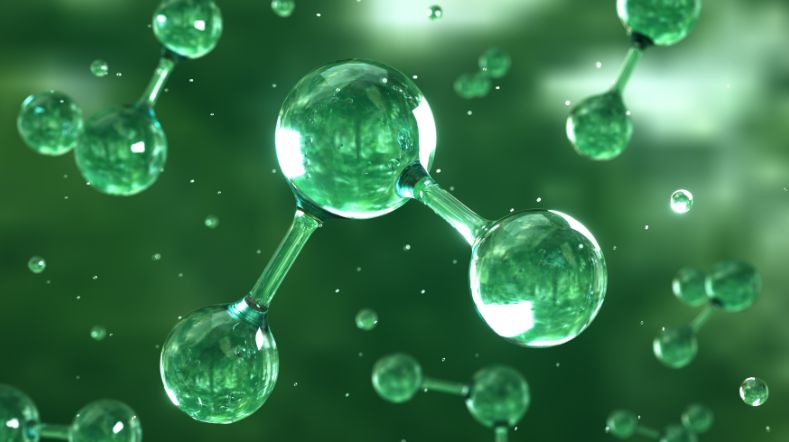
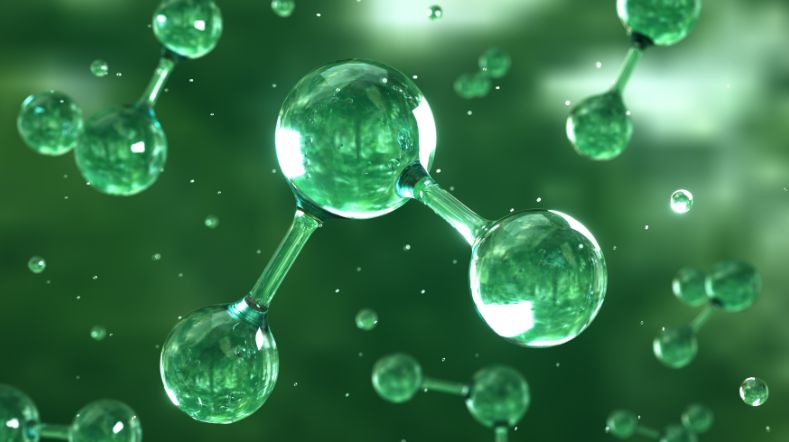
Enhanced solvolysis contributes to the future of composite recycling
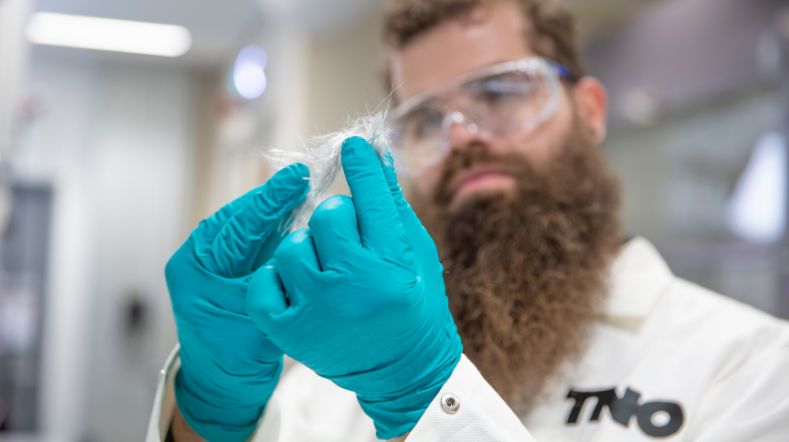
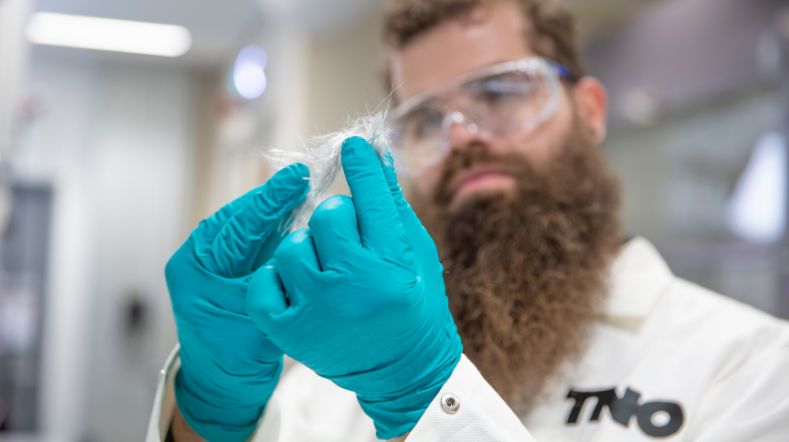
Collaboration for sustainability: better results through joint innovation
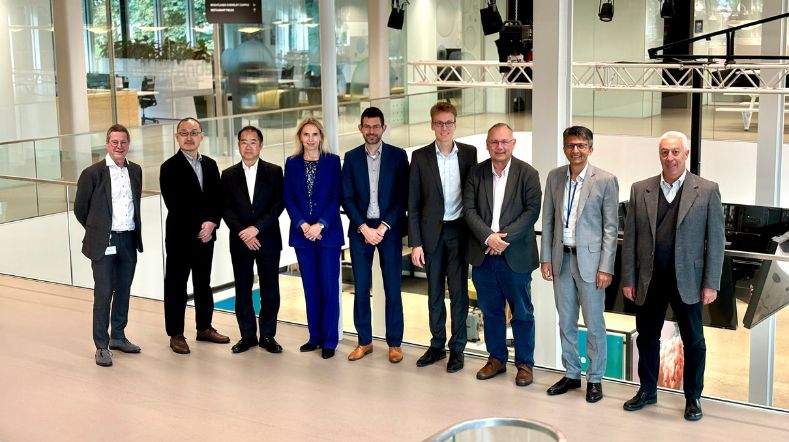
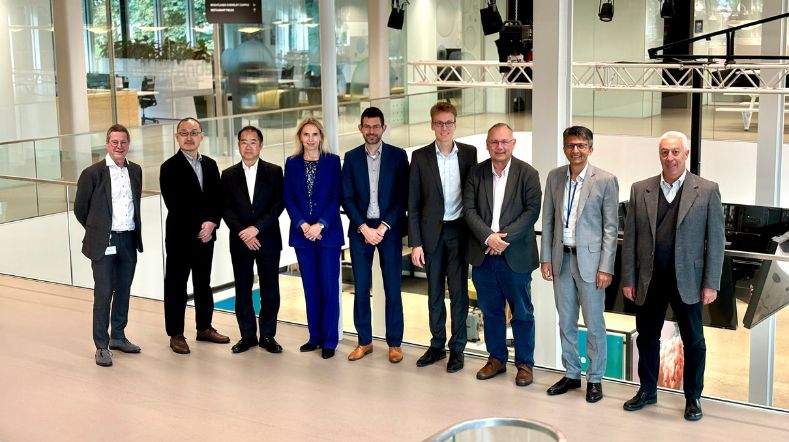