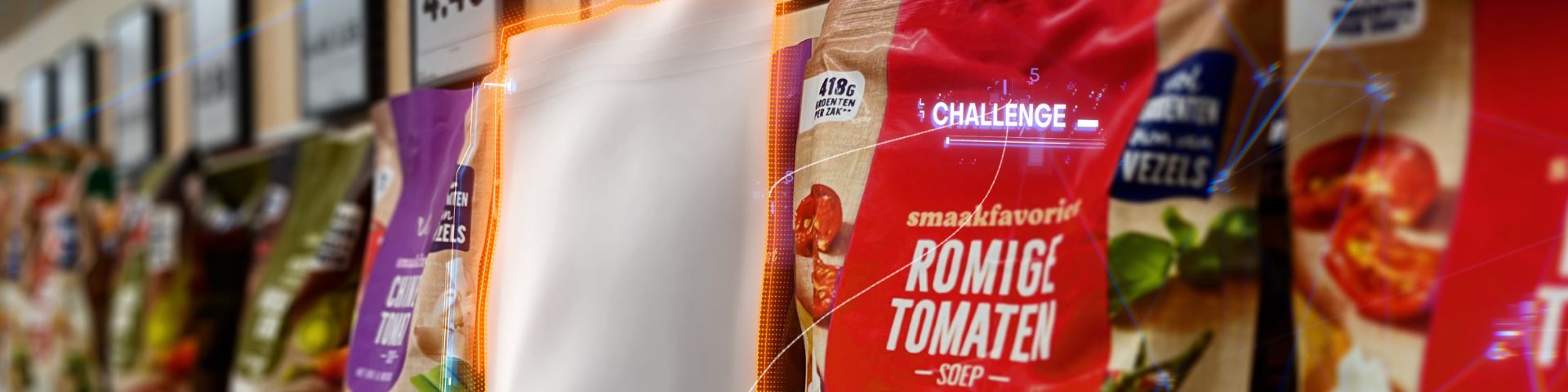
Progress in circular packaging for soups and sauces
TNO Brightlands Materials Center has made significant progress in developing a recyclable, mono-material soup pouch made from polypropylene (PP). Together with partners, we developed a retortable soup pouch that can be filled and sterilized as usual and meets functional requirements such as barrier performance and shelf life. This innovation addresses the pressing need for circular packaging solutions in the food industry. However, there's one challenge left: the drop-impact resistance needs to be increased for a wide market acceptance and guaranteeing a successful commercialization of the new monomaterial soup pouch.
Complex soup pouches difficult to recycle
Current soup pouches are tough to recycle. That’s because they’re made from multiple-layer films of different materials; PET, aluminum, PA, and PP. Each serving a specific function like sealing, stiffness, or barrier protection against oxygen and moisture to prevent for example spoilage and loss of taste.
Next to that the pouches must be retortable, meaning the packaging needs to be able to cope with the high temperature (115–130°C) and pressure that are associated with the production of soup that can be preserved for a longer time.
The combination of these materials needed to fulfill the requirements, can’t be separated and recycled in the current recycling systems. As a result, they often end up in incineration, and not into new products.
New monomaterial PP retortable pouch passes first key tests
Together with the partners Sabic, Oerlemans Plastics B.V., Four Seasons Food B.V, Greenyard Prepared Belgium, Hogeschool Zuyd, and Plato product consultants, TNO-BMC has developed a monomaterial polypropylene (PP) laminate. The pouch can withstand high-temperature sterilization, is printable, and meets oxygen and moisture barrier requirements.
Over 2,000 pouches were produced and tested on commercial soup filling lines. The packaging showed solid results in taste and smell tests, sealed well, and maintained its quality after processing.
Two key challenges remain
While the new pouch has shown excellent results in terms of barrier performance, taste, and shelf life, its drop-impact resistance is still slightly below that of conventional multi-material pouches. This is a critical requirement for wide market acceptance, particularly for acceptance by A-brands.
Secondly, the pouch was designed to follow RecyClass guidelines. RecyClass is a European initiative that helps companies design plastic packaging that can be recycled. It provides technical criteria and testing protocols to assess recyclability.
The pouch passed internal checks. It contains over 95% polypropylene (PP), uses barrier layers accepted by RecyClass, and is detectable by near-infrared sorting systems. Still, recyclability has not yet been externally validated. Not all current sorting systems can yet fully separate PP from other flexible plastics like polyethylene (PE). Full circularity will depend on future upgrades to sorting infrastructure, expected within two to five years.
Both the drop resistance and recyclability will be addressed in a follow-up project.
An almost > 50% lower carbon footprint
A life cycle analysis shows that the mono-PP pouch has a 41–53% lower carbon footprint compared to traditional multi-material pouches. The new pouch is slightly more expensive due to extra lamination steps. Therefore, future work will focus on simplifying the structure to reduce costs.
Closer to circular soup packaging
The mono-material soup pouch represents a major step toward circular food packaging. However, it is not yet ready for commercialization. Key next steps include improving drop-impact resistance, confirming recyclability through external validation, and optimizing the pouch structure to reduce costs. We invite partners across the value chain to collaborate in scaling this innovation and achieving full circularity.
We encourage you to visit us at K Fair 2025 and share your biggest challenges. Or, contact us for more information. We are ready to get started.
Visit us at the K Trade Fair
You can find us at the world's largest trade fair for plastics and rubber.
8 to 15 October 2025, Düsseldorf, Germany
📍We will be in Hall 7, stand SC10
Get inspired
Biobased plasticisers: from compliance to competitive edge
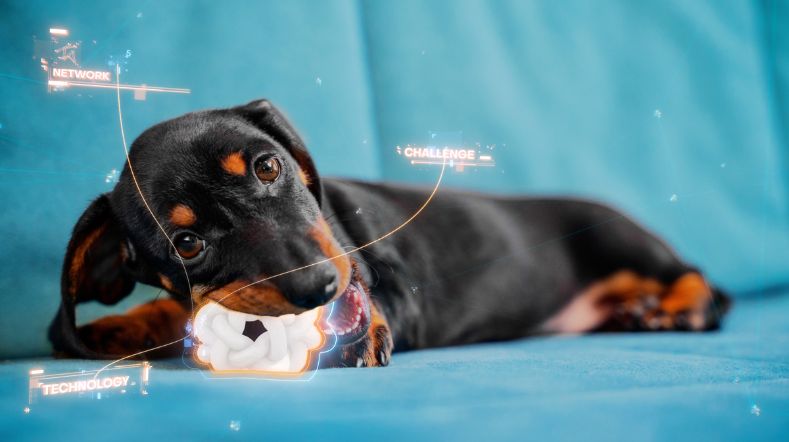
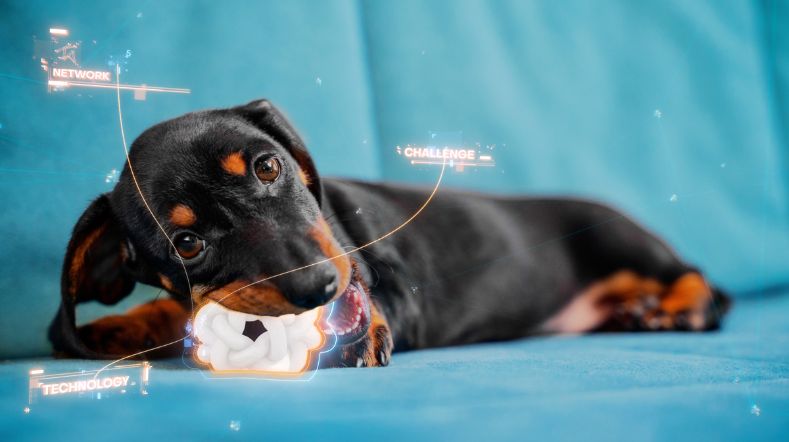
Microplastics in clothing
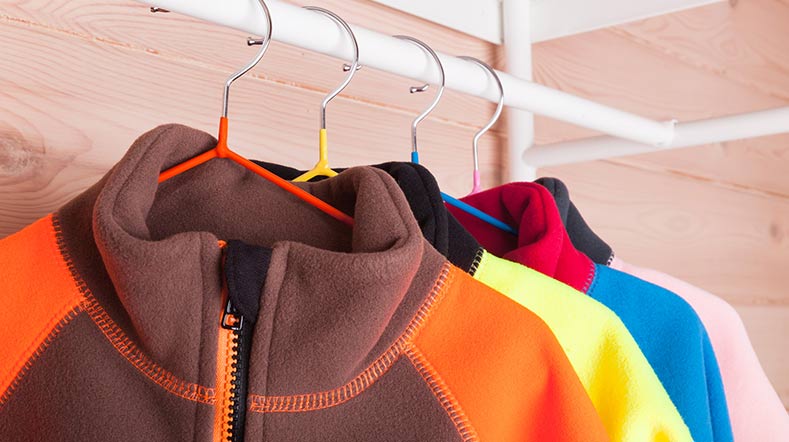
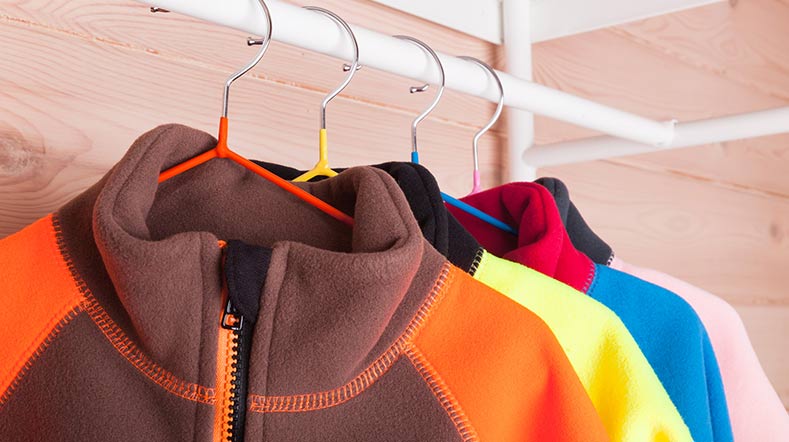
Early results show the potential of circular healthcare plastics


Thermoplastic composites for sports innovation
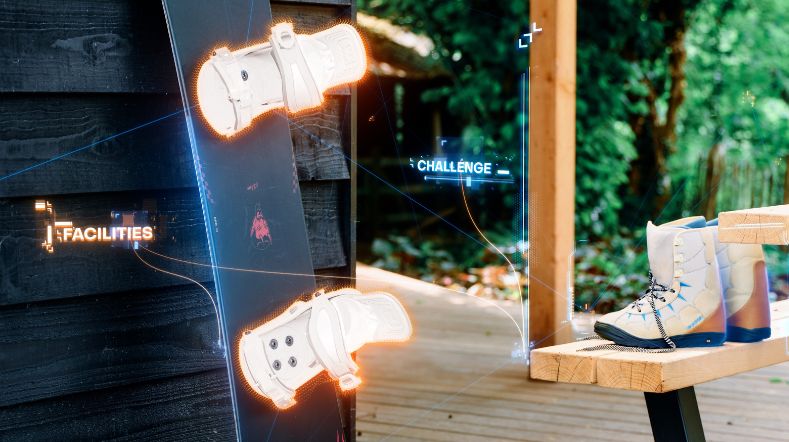
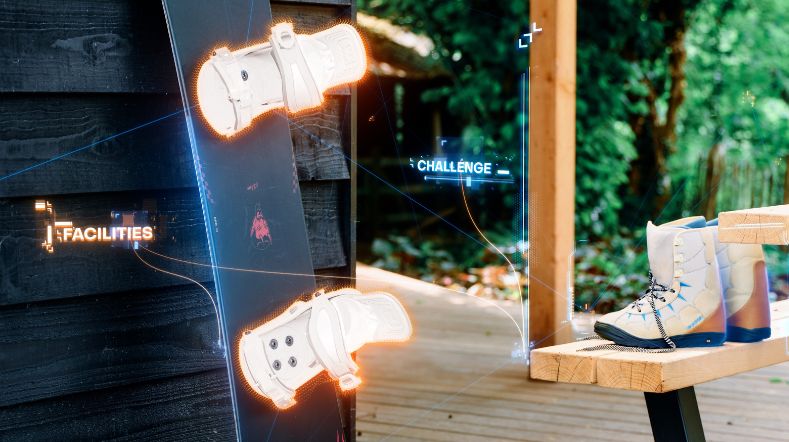
Biobased materials
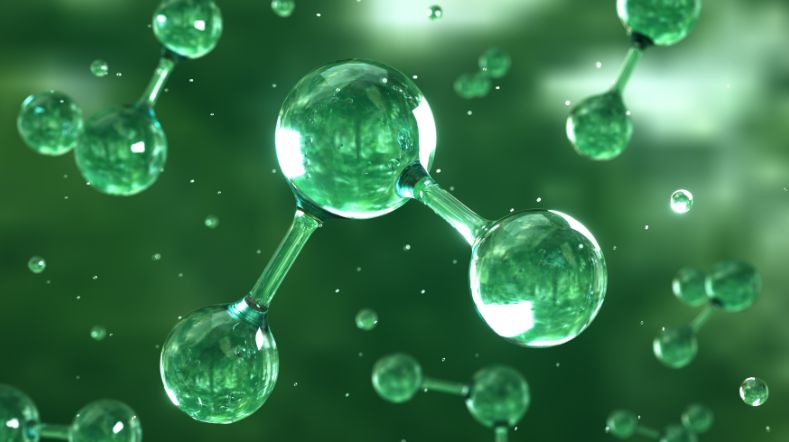
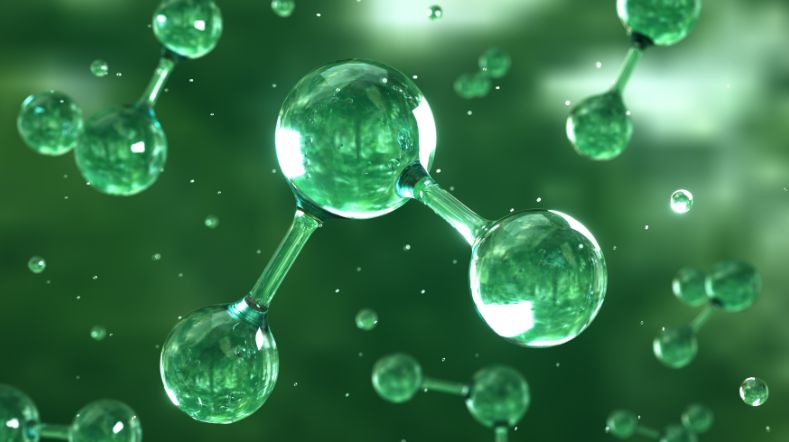