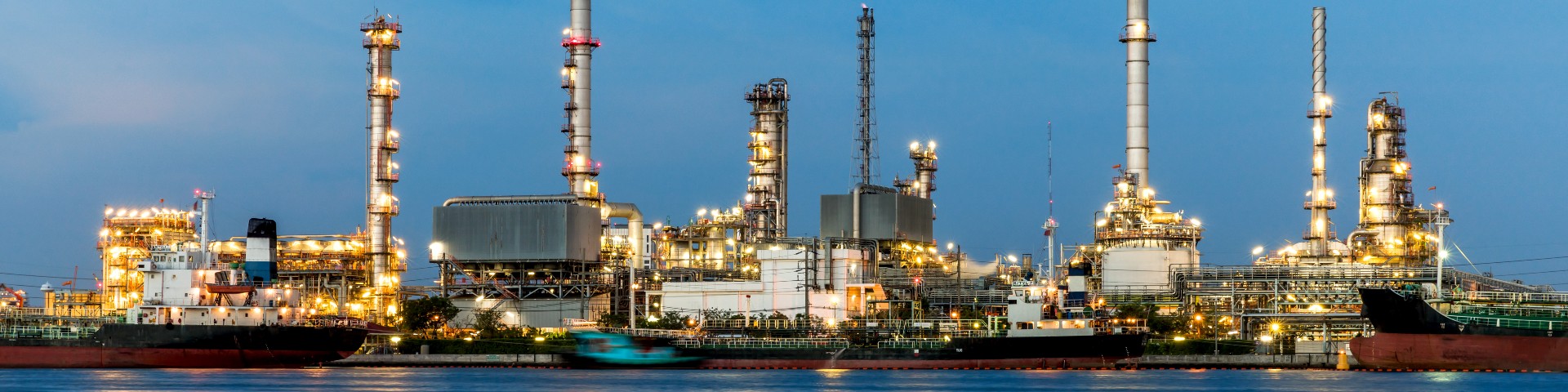
Thermal cracking for plastics: breakthrough reached in chemical-based recycling
Some plastic waste streams are simply not suitable for mechanical, physical, or chemical recycling – whether it’s for technical reasons or it’s simply not economical, or both. That’s where thermal cracking comes in, as a solution to bring plastics into the circular economy. Thermal cracking is an advanced thermochemical recycling process that can break down plastic waste into new ‘building blocks’, which can then be used as feedstock for existing industrial plants. TNO has developed the MILENA thermal cracking technology to efficiently convert various types of plastic waste into high-quality chemicals.
Advanced recycling for food and medical applications
Thermochemical recycling can be used to make feedstock for high-quality plastics, such as food or medical applications. Chemical-based recycling produces monomers as well as these building blocks similar to those at the start of the polymer production process. This means they have the same composition and quality as ‘virgin plastics’ made out of raw materials derived from fossil fuels.
TNO is developing technologies to make that all possible, with the added benefit of reducing our usage of fossil fuels. We can also continue to use existing and time-tested petrochemical plants and infrastructure, such as by integrating the thermal cracking process with naphtha crackers, using existing separation facilities.
Innovative solutions for mixed plastic streams
Thermal cracking works by heating plastic waste to an elevated temperature, until it cracks and breaks down into smaller molecules. It is just one thermochemical conversion process available; there are others including pyrolysis and catalytic pyrolysis. These mainly differ in the temperature applied, whether any catalysts are present, and the process design.
With TNO’s MILENA thermal cracking technology, plastic waste is cracked at a higher temperature (550-850°C) without adding oxygen, so they form mainly gaseous molecules such as ethylene, propylene, and BTX (Benzene, Toluene, and Xylene). These, in turn, can be used as building blocks for new polymers and/or chemicals.
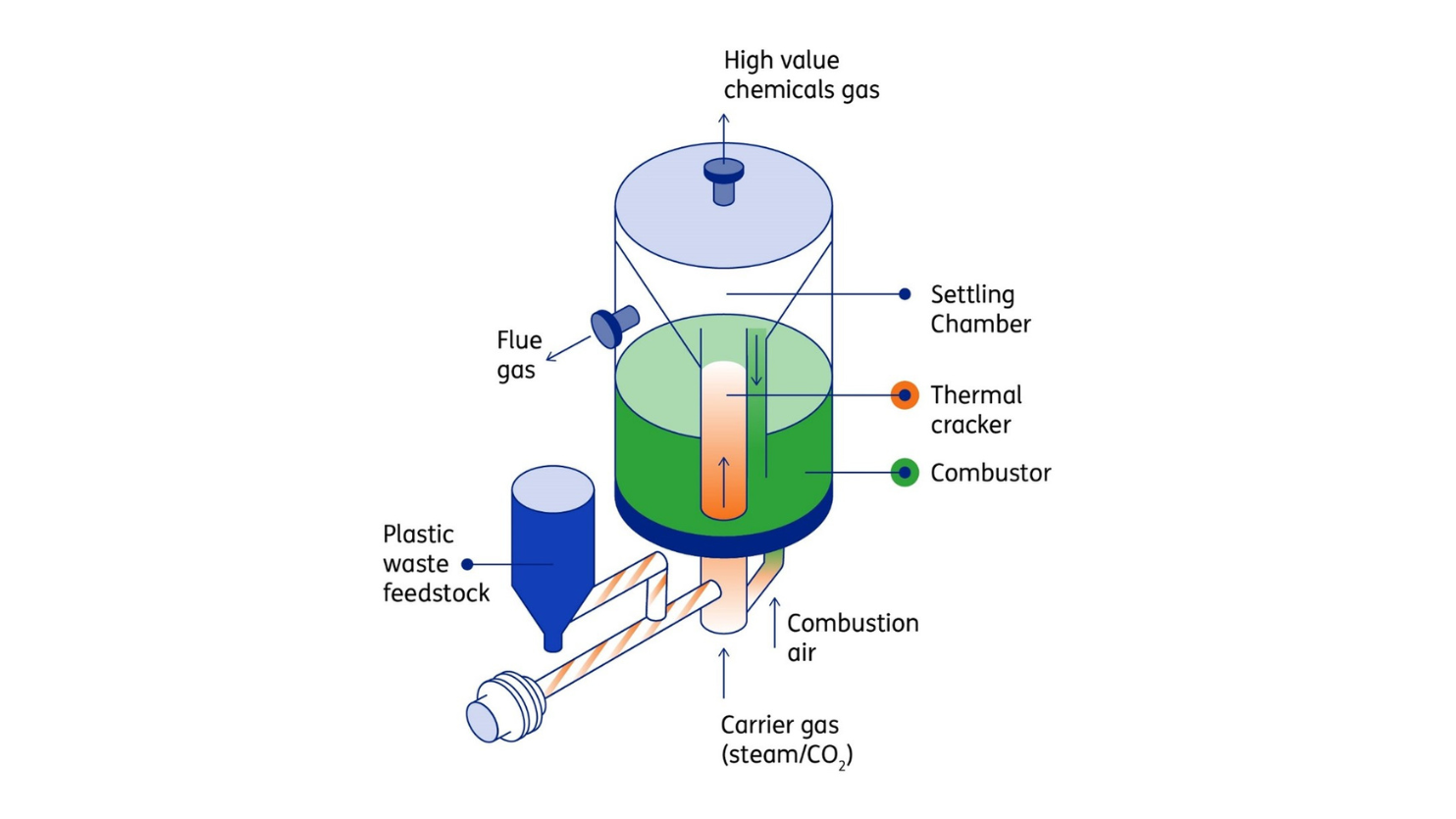
The figure above illustrates how the MILENA technology works. Plastic waste is fed through an inlet to the riser reactor, where it comes into contact with a heat source (hot sand). This environment results in thermal cracking (marked in the orange zone). In the settling chamber, the gases are separated from the heat source. The cooled sand is then fed into the combuster. The light gases released during cracking are used as feedstock for new plastics, while the heavy by-products are incinerated in the combuster, releasing energy to reheat the sand. And all in a circular process.
Admittedly, this technology uses more energy than mechanical or physical recycling and requires investment in chemical process plants. But it is more robust and better suited to mixed and contaminated plastic streams compared with other recycling technologies. This means it can play a vital role in the future. After all, there will always be a need to process a mixture of plastics and films that can’t be recovered by mechanical and chemical means.
Optimising the thermal cracking process with MILENA technology
Thermochemical cracking has been proven to work very well for plastic waste streams rich in polyolefins ‒ an umbrella term for polypropylene (PP) and polythene (LDPE or HDPE). These are often used for food packaging, bottles, and pipes.
In the typical pyrolysis process, the polyolefin-rich waste forms a broad mix of liquid products, from which naphtha can be derived for use as crackers.
By contrast, the MILENA thermal cracking process forms gaseous products in one go, so they can be used as building blocks straight away. This allows you to skip several steps compared with the standard pyrolysis process. The fact that these gaseous products are formed in a more direct way makes this technology easy to integrate into existing plants.
Thermal cracking technology is also well suited to processing polystyrene waste from yoghurt packaging, for example. MILENA technology is being developed together with SYNOVA technologies to process waste containing polyolefin or polystyrene waste.
Thermal cracking in other waste streams
Thermal cracking has also proven itself useful for other waste streams, such as textiles, mattresses, insulation materials, and composites. Every application comes with its challenges, but they all have something in common: we can separate valuable products from complex plastic waste streams.
Thermochemical recycling in other forms
Plastic waste streams could instead be gasified or incinerated. Gasification is the process of converting waste into syngas (CO+H2) at a very high temperature, using a limited amount of oxygen. Syngas is a highly versatile feedstock that can be used for a wide variety of chemicals and fuels. TNO uses various technologies to convert syngas into valuable products.
From a circularity point of view, incineration is the least preferred solution for plastics. But if it is used, it should be combined with full heat integration and carbon capture and utilisation to achieve maximum circularity. TNO has developed several carbon capture and utilisation technologies to optimise CO2 removal and carbon sequestration.
Machine learning as a tool in thermal cracking
Thermal cracking and indirect gasification are promising thermochemical recycling routes. They valorise difficult-to-treat waste streams, such as mixed plastic waste. To facilitate scale-up and commercialisation of these technologies, Machine Learning (ML) models can predict product compositions of different feedstocks under various process conditions.
Machine Learning is a powerful tool for modelling complex processes. TNO developed a physics-informed ML model by combining ML with physical principles. This model accurately predicts the complete carbon distribution of thermal cracking and indirect gasification products, while ensuring scientific consistency. It uses direct input parameters such as operating conditions (temperature and steam flow) and feedstock properties to make fast and accurate predictions. This model is suitable for a wide range of feedstocks, including biomass and plastic waste.
The physics-informed ML model:
- assists with process optimisation by maximising product yields and minimizing unwanted byproducts, such as CO2.
- serves as a screening tool for new feedstocks, reducing time and cost associated with extensive characterisation and experimental work.
- is adaptable for real-time process control to improve the economic viability and sustainability of recycling processes.
This model is a significant first step towards the modelling and development of advanced thermochemical recycling processes. Further developments are in progress to broaden the model’s application range.
Want to know more about physics-informed machine learning models?
Read more about our research on the development of a novel physics-informed machine learning model for advanced thermochemical waste conversion.
Struggling to process your own waste streams? We’d be happy to take a look with you at your waste streams. And then based on technical, economic, and impact analyses, we can help you decide on your options: whether mechanical, physical, or chemical recycling, cracking, incineration, or gasification.
Get inspired
Biobased materials
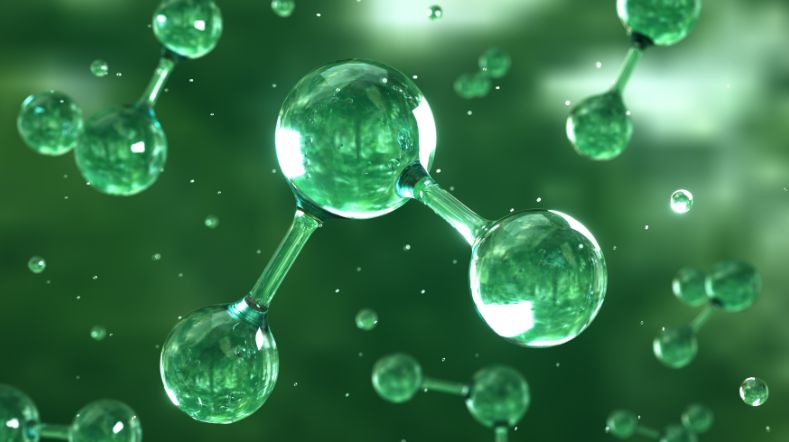
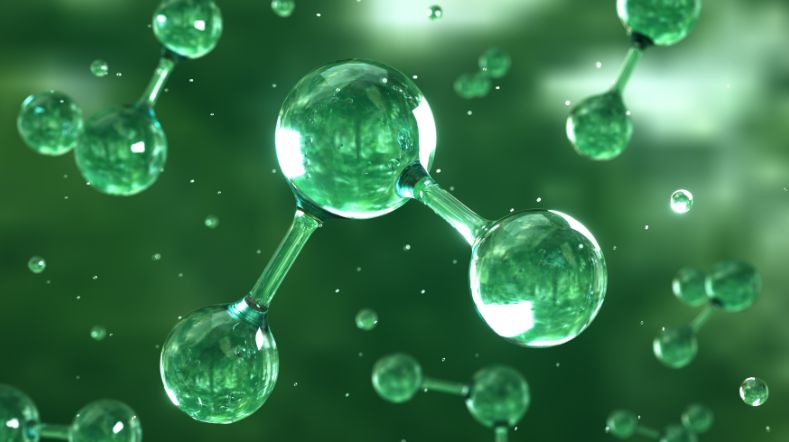
Enhanced solvolysis contributes to the future of composite recycling
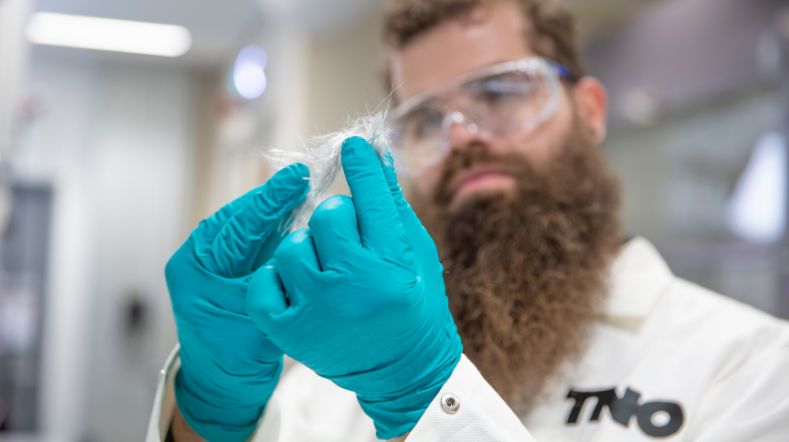
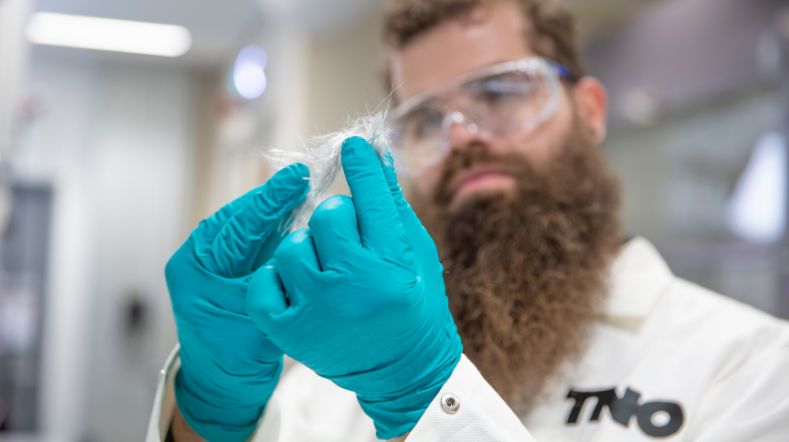
Collaboration for sustainability: better results through joint innovation
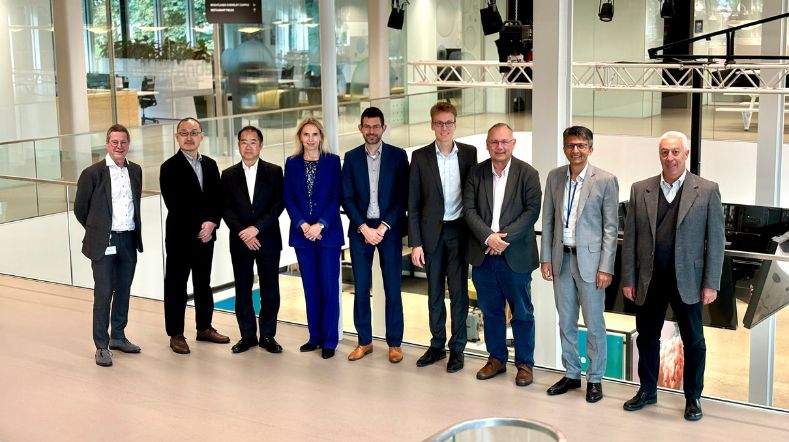
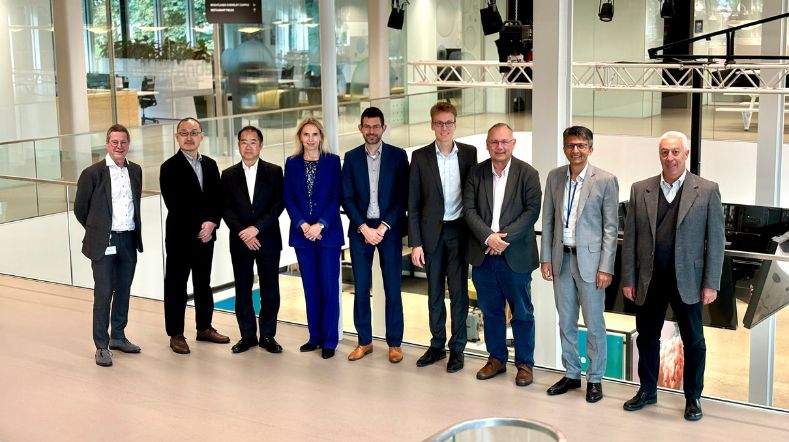
Webinar: Biobased plastics in a sustainable future
Biobased plastics
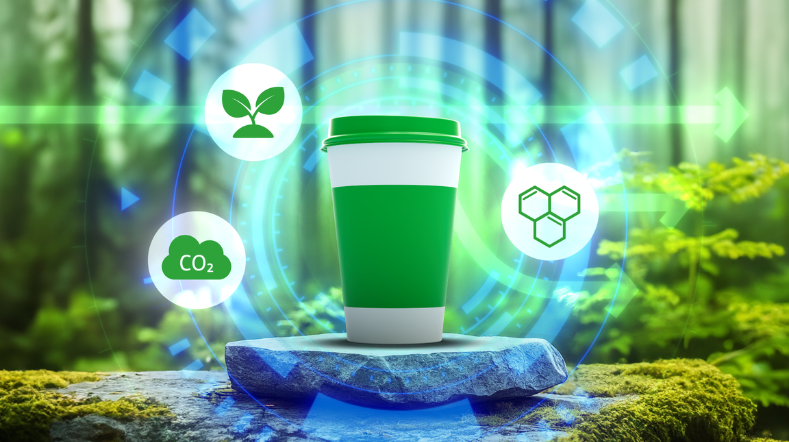
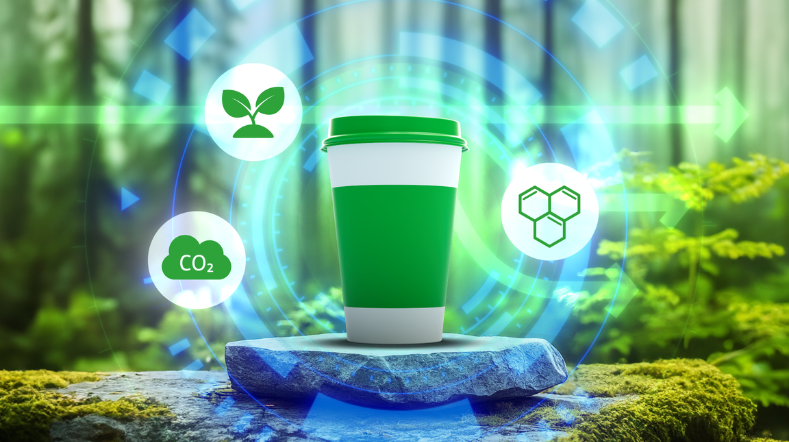