Cold baked brick - energy saving
TNO has developed a new process for producing a brick that does not require extremely high temperatures. The production process of bricks normally consists of heating clay to 1000 to 1200 degrees Celsius.
The new process uses an (alkali) activator, where the aftertreatment temperature is between 20 and 50 degrees Celsius. This results in major energy savings for the producer. TNO has carried out various tests and produced samples. It has become clear that this new production method offers new possibilities for the recipe for the bricks. In addition, there are new possibilities in the field of texture, strength, colour and dimensional stability of the bricks.
Future of the cold baked brick
TNO's new technology offers a number of inherent advantages for the construction industry. The coming period will be dominated by knowledge valorisation: bringing the new knowledge to the market. The advantages of cold baked brick at a glance are:
- Lower production costs as a result of reducing energy costs during baking;
- Contribution to lower CO2 emissions (smaller footprint, reduction in consumption of primary raw materials);
- Product development, using the possibilities of cold baking (e.g. extra taut bricks or thin wall panels)
Get inspired
How ‘smart thermochromic glass’ saves energy in homes
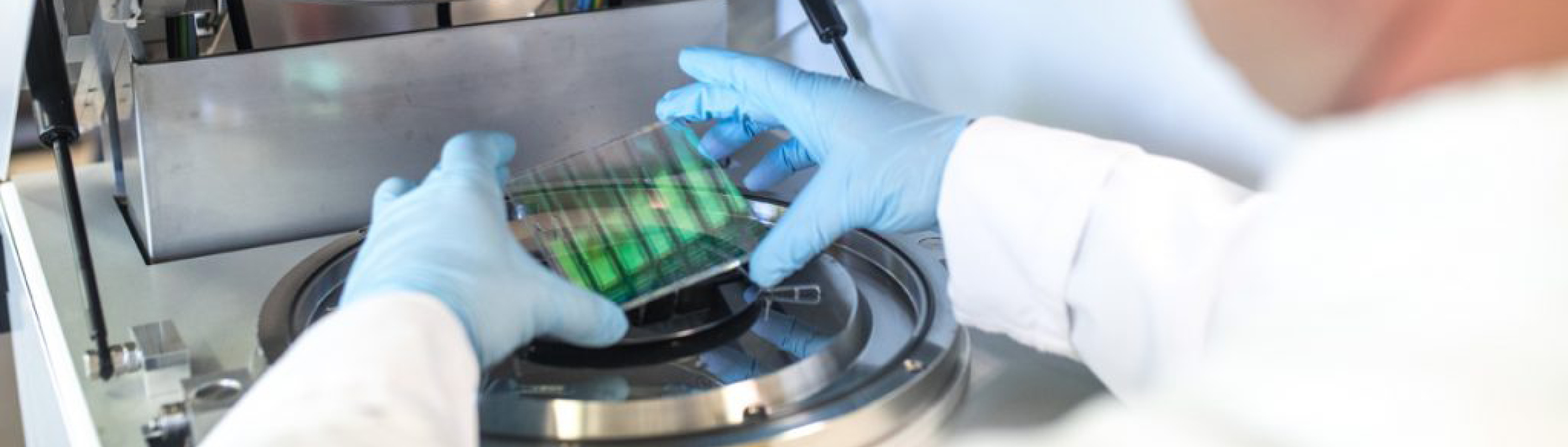
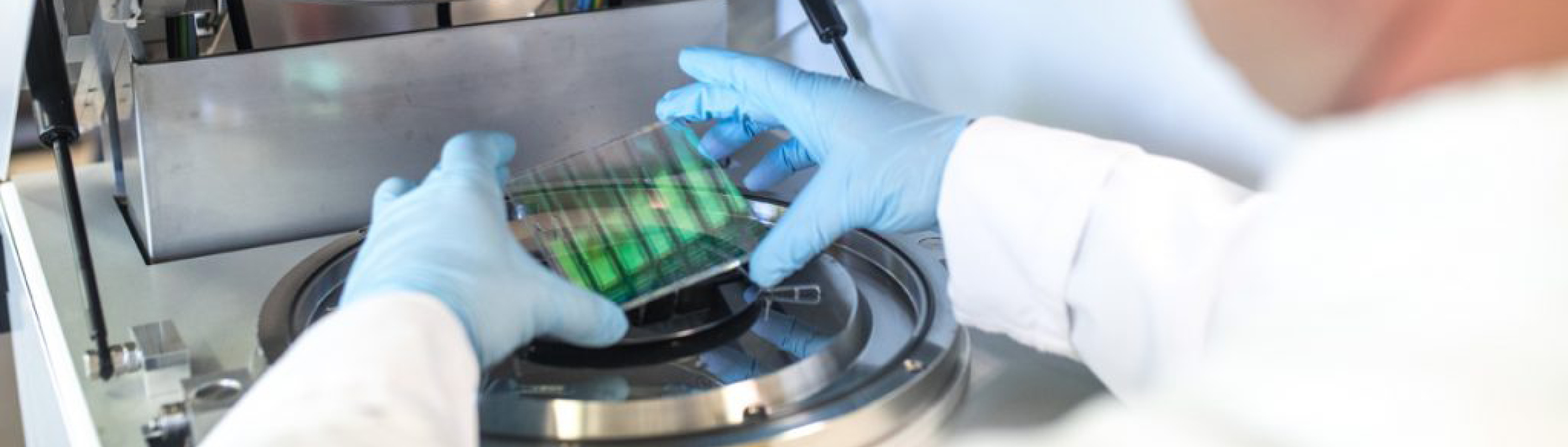
Making homes sustainable: knowledge breakthroughs and new opportunities thanks to AI
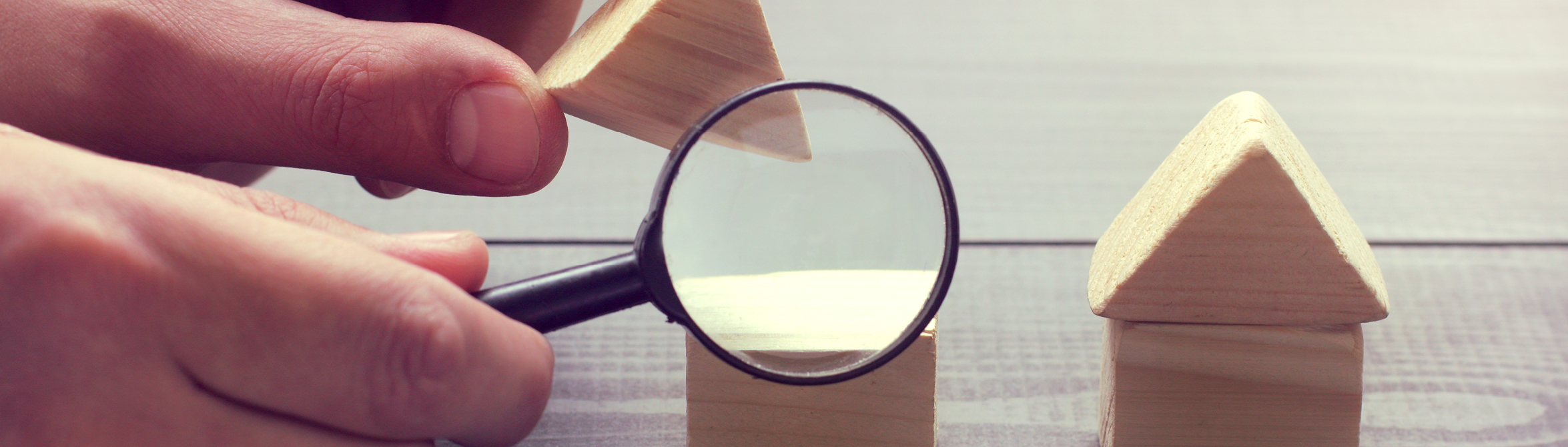
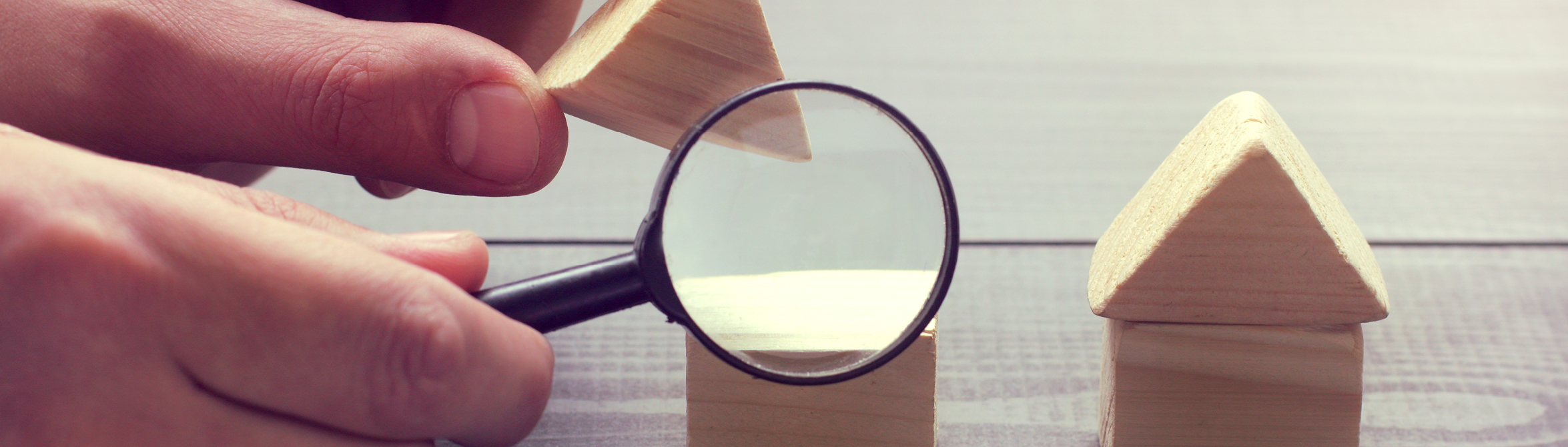
Baking energy efficient bricks
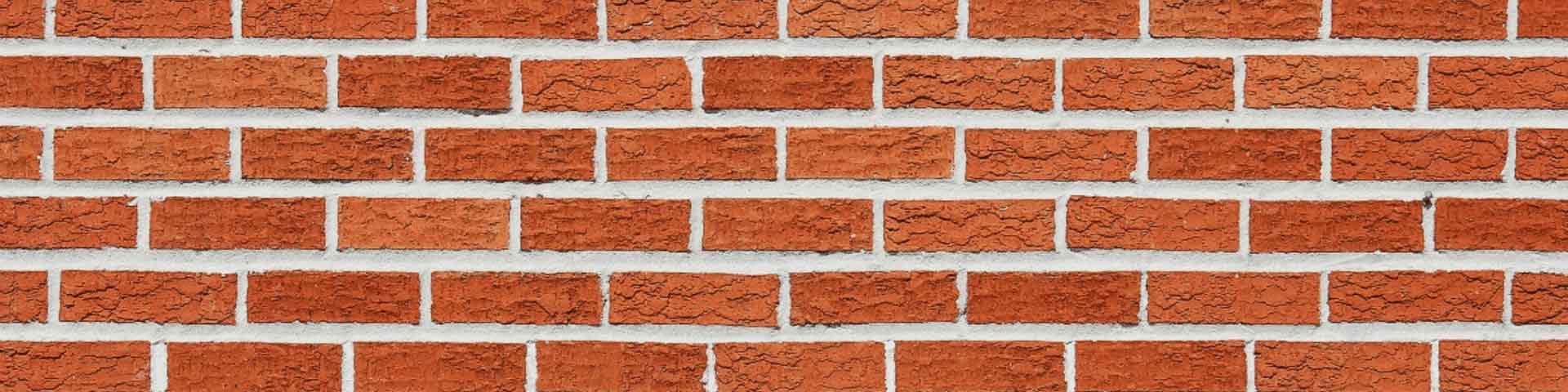
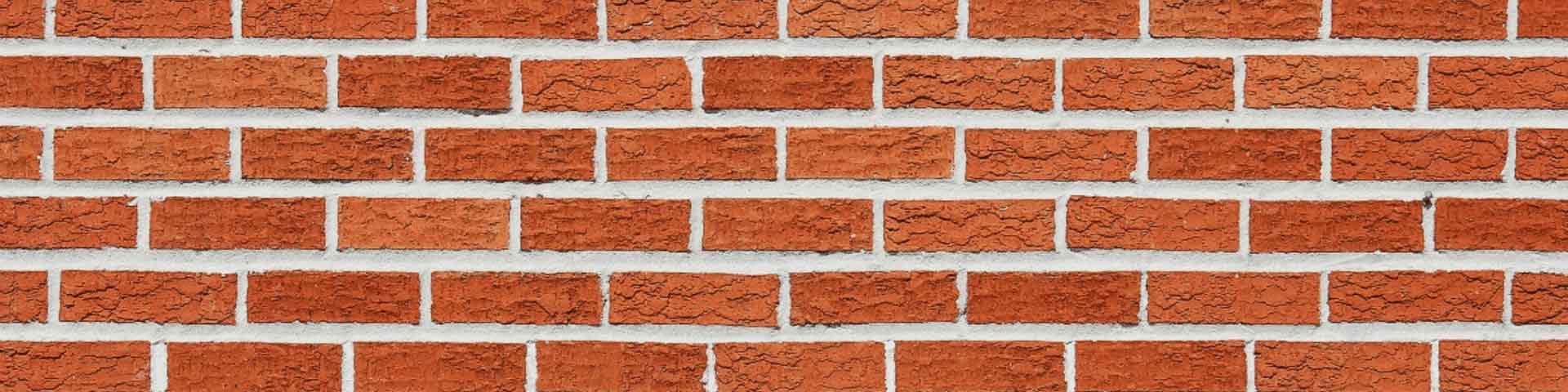
Cold ceramic bricks do have potential in Malawi
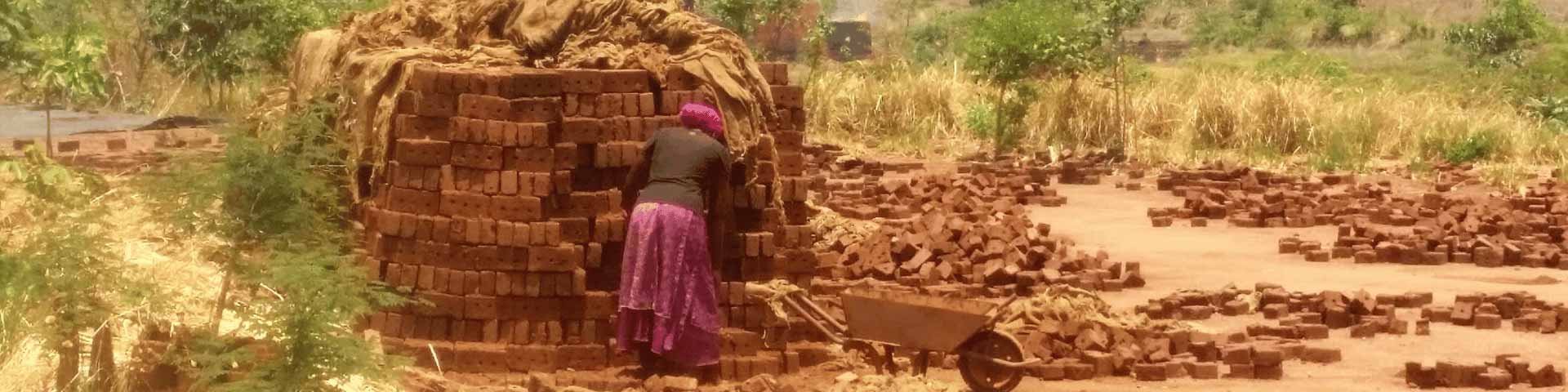
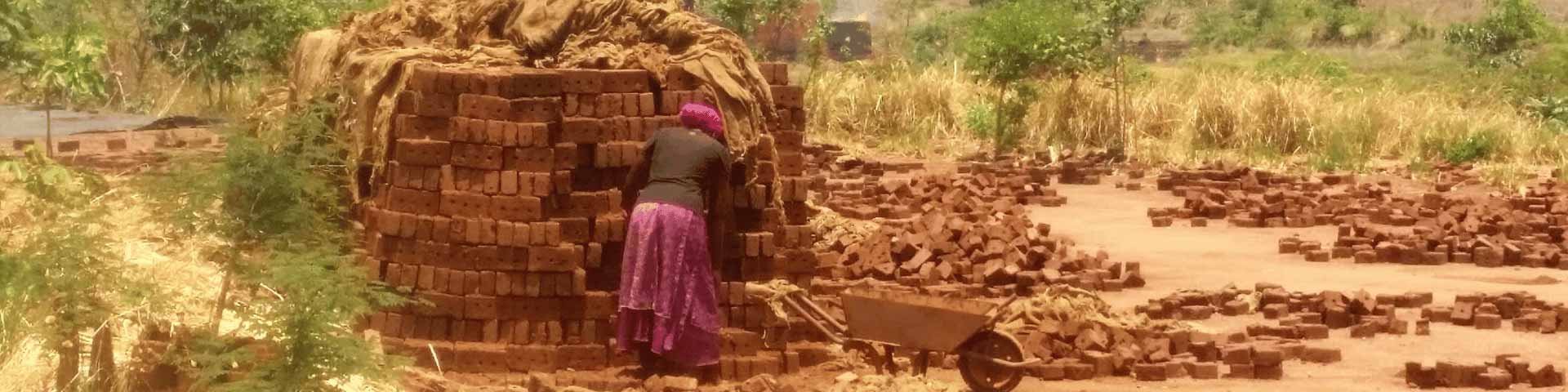