Energy supply
TNO researches, develops, orchestrates, and enables cutting-edge innovations that drive the change to net zero.
TNO Energy Supply focuses on an efficient energy production and storage infrastructure, both onshore and offshore. From effective, ecological and circular production and use of all components related to wind and solar energy.
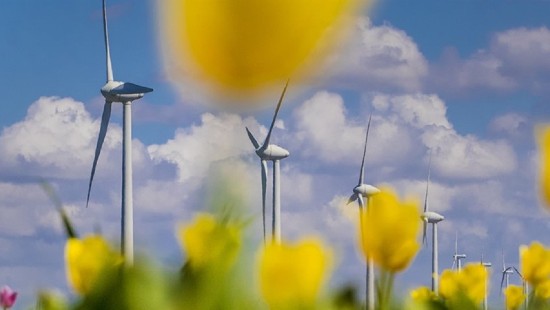
Cheaper and more effective electricity from solar and wind
Increasing renewable electricity is essential, but challenging. We’re developing technology for cheaper and more effective solar and wind energy.
Our latest developments
97 resultaten, getoond 1 t/m 5
TNO and Jungle AI collaborate to detect cyberattack on wind turbine and improve detection capabilities
In a recent event at the SWITCH renewable energy fieldlab in Lelystad, TNO demonstrated a realistic live cyber-attack on one of its very own renewable energy assets: a wind turbine.
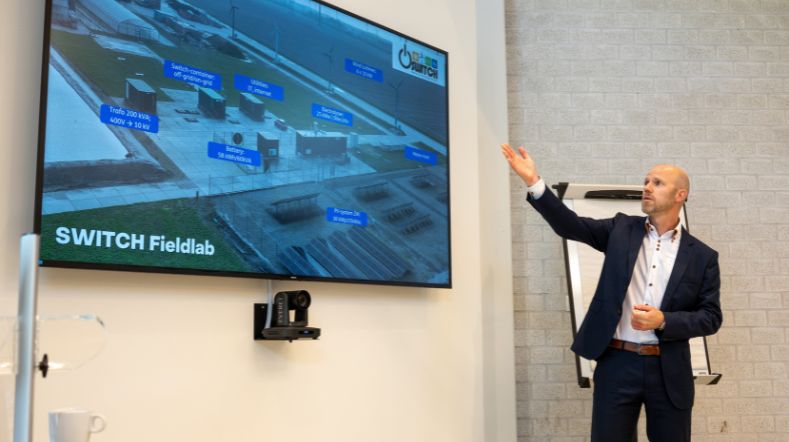
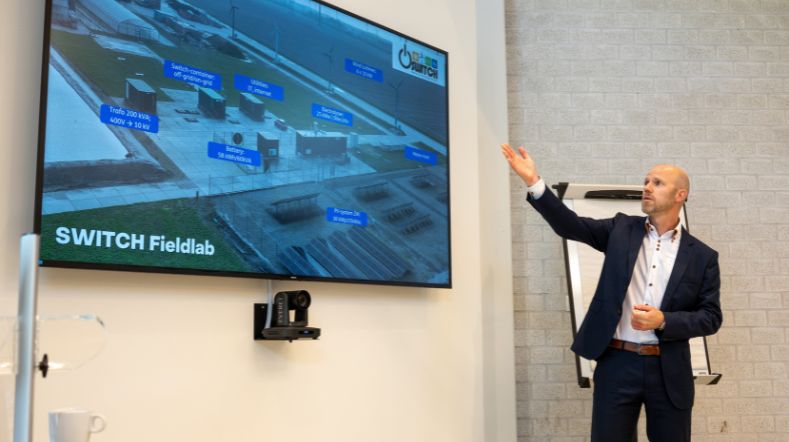
Improving wind turbine maintenance with the sensor installation robot
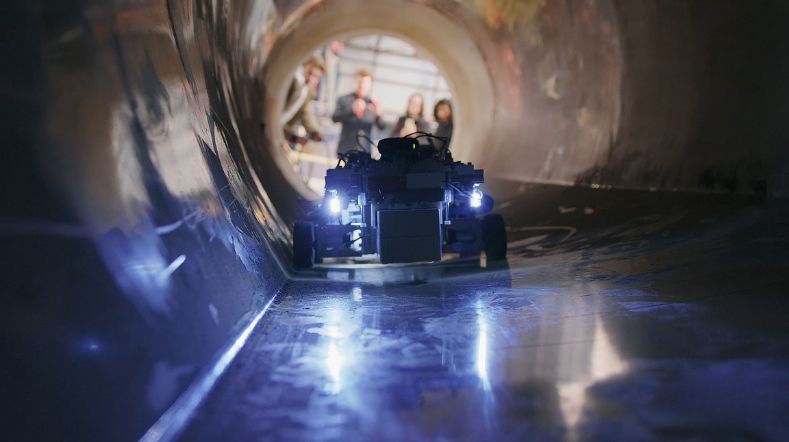
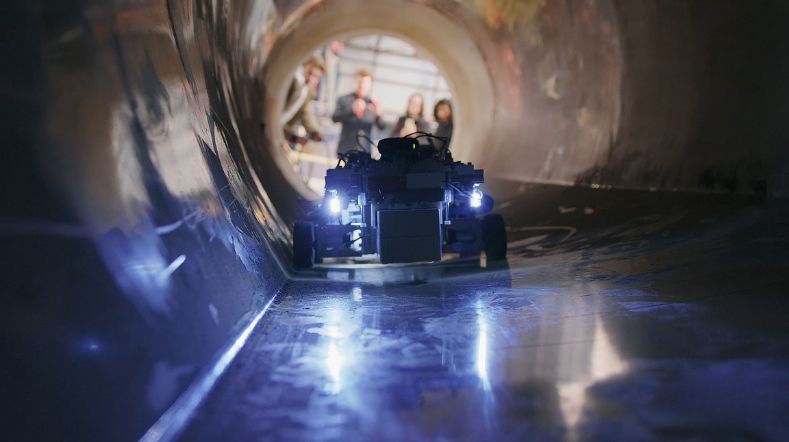
Project launched for recycling wind turbine blades
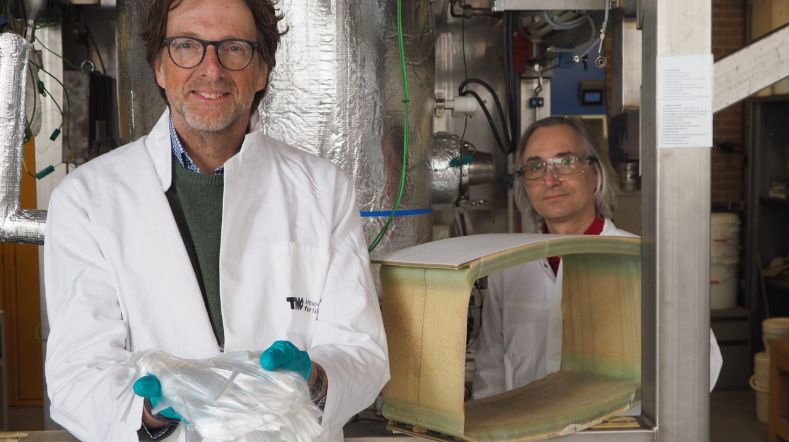
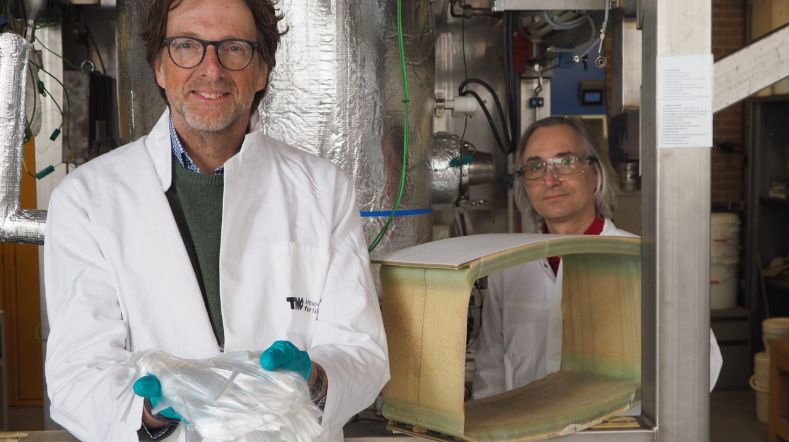
Shade screens with rollable solar foil combines energy generation with climate control in greenhouses
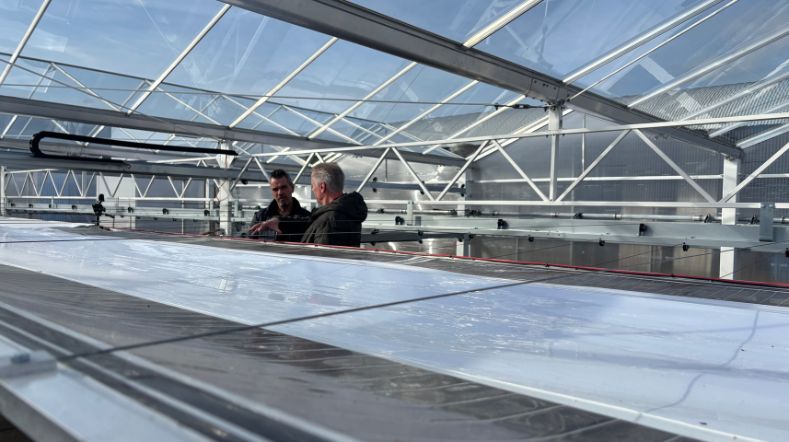
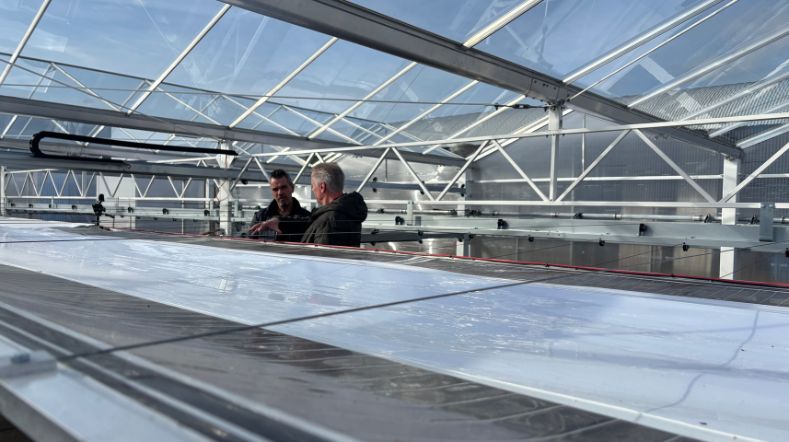
TNO research leads to better damage prediction for offshore wind turbine blades
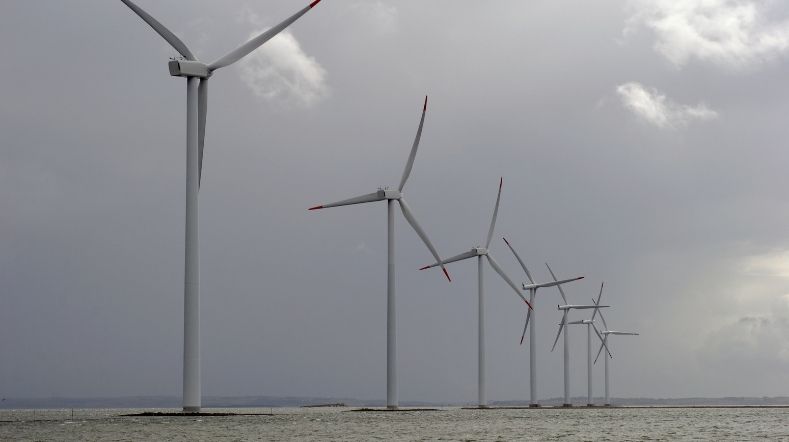
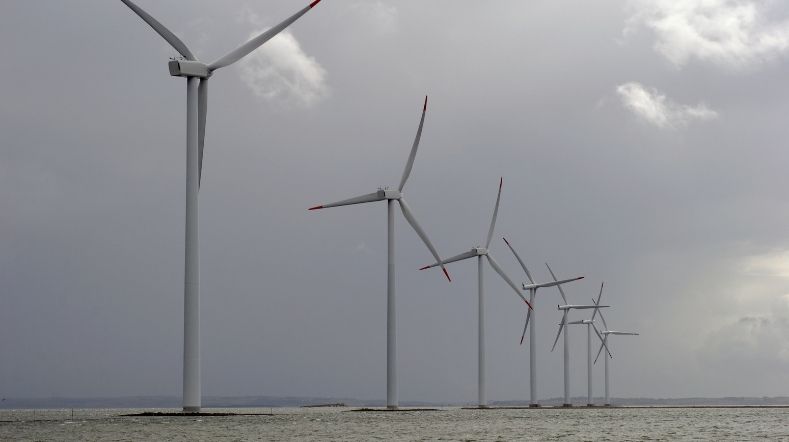