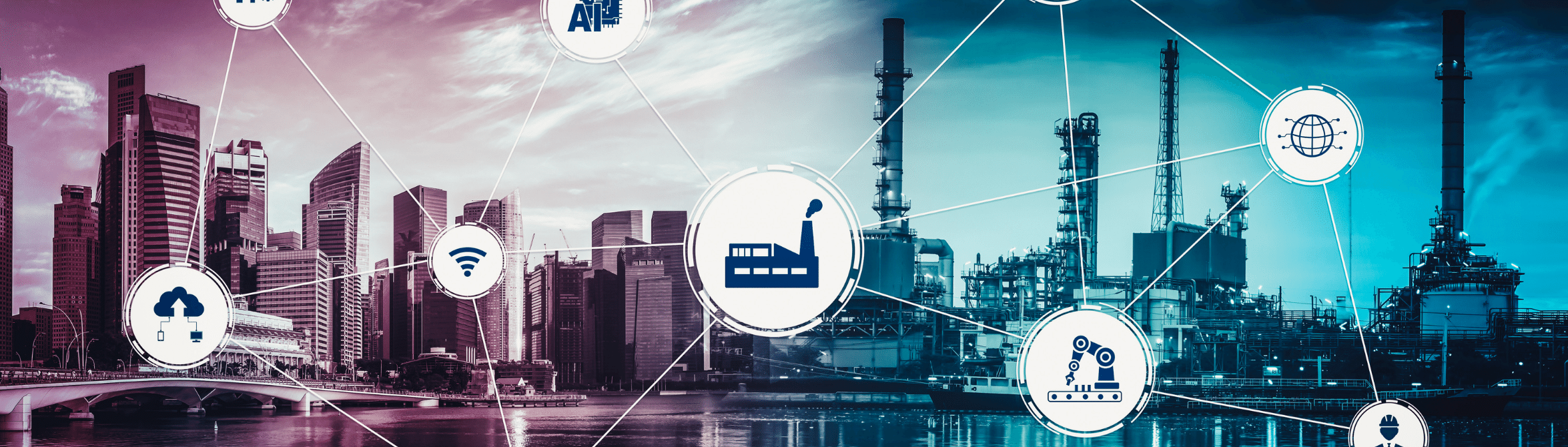
Dutch industry needs 'digital connectors' to increase productivity
By committing to a short time-to-market, first time right engineering and a seamless production chain, the industry is rapidly digitizing, generating huge amounts of data. To keep control, we need a strong and secure European data infrastructure that will help manufacturing companies to increase their profitability and productivity. Discover how TNO partners are accelerating their digital transformation with 'digital connectors', field labs and training.
Digital Sovereignty Dossier
-
Strengthening digital sovereignty makes Europe less vulnerable politically and economically
-
Data sovereignty: an opportunity for European businesses and technology providers
Market trends and technological developments are happening so fast that the industry needs to shift up a gear. It is expected that all aspects of the manufacturing process will be fully digitized within ten years. Increasingly large financial interests, faster market introductions, and higher quality demands require a fully integrated supply chain offering hyper-connectivity, which means that all company assets are connected and able to communicate with eachother. This development fits in seamlessly with our Dutch Smart Industry ambition to have the most flexible and best digitally connected production network in Europe by 2025. This digitization results in explosive data growth; data is not only generated during production, but throughout the entire life cycle. With a strong European data infrastructure, we can secure our digital sovereignty. But how do you build such a network, and how can you, as a manufacturing company, ultimately reduce costs and increase productivity?
Hightech eco system
This was the fundamental question that laid the foundation for Brainport Industries. Started in 2011 as a cooperative of seven suppliers within the high-tech manufacturing industry, Brainport Industries has grown into an ecosystem of 120 technology companies in the Netherlands, including the Brainport Industries Campus (BIC). Managing Director John Blankendaal: “We facilitate high-tech manufacturing companies in improving their time-to-market and time-to-money. Customers such as ASML and Philips benefit from a supply-chain that grows with them. Digitization is the only way to accomplish that productivity boost and maintain our competitive position.” The efficient exchange of data across the entire supply-chain is crucial in this regard, Blankendaal knows. “15 years ago there were hardly any data standards or agreements. Jobs came in by fax and were typed into the production management system by hand, resulting in a lot of errors and extra costs.” Together with industry partners, we have formulated standards and security requirements for data exchange with our suppliers. That eventually grew into the Smart Connected Supplier Network (SCSN), one of the fastest growing data standards for the manufacturing industry.” The SCSN shows that users can gain momentum by organizing themselves and formulating requirements for and together with their suppliers.
"15 years ago there were hardly any data standards or agreements. Jobs came in by fax and were typed into the production management system by hand."
Living lab for digital factory
TNO has been involved as a knowledge partner in the data innovations of Brainport Industries from the very beginning. Egbert-Jan Sol, Program Director Smart Industry TNO. “The standardization of communication between machines within companies and with other organizations within the supply-chain will continue to grow in the industry over the years. Machines will be able to exchange information without human intervention. With the Digital Factory, which TNO has set up together with Brainport Industries, we show the possibilities.” In this living lab, students, developers and entrepreneurs work on the blueprint for the digital factory of tomorrow. “We use the RAMI 4.0 model for this,” Blankendaal explains. “This is a three-dimensional model in which all business assets are connected to each other and within the supply-chain. We then record all assets, equipment and processes in a so-called Asset Administration Shell (AAS). This allows you to digitally steer and manage processes even better. Ultimately, such an AAS can develop into a Digital Twin, to create simulations and predictions, to further optimize your production process.”
Digital plug
RAMI 4.0 is an example of a 'digital plug': a model that describes how all systems within an organization and within the supply-chain can communicate with eachother. Egbert-Jan Sol: “That plug is an easy to understand metaphor for a complex problem. Behind the socket there is a complicated world of electricity production, contracts, network management, et cetera. But that plug is easy to use, everywhere. Actually just as easy as the apps on your smartphone. That’s our future goal for production systems: to simply donwload a new app whenever a new machine is installed in the factory.” Standardization makes it easier to connect equipment and new parties in the suplpy-chain with reduced costs for a reliable, 'plug & play' process.
The challenge lies with SMEs
Although the first European digital standards and 'digital connectors' are in place, there’s still a long way to go. Egbert-Jan Sol: “It's great that a handful of large high-tech companies are already working according to Smart Industry standards. But in the end, our country will benefit much more if the approximately 60,000 SMEs, accounting for 80 percent of our GNP, will increase their productivity through digitization.” That is why TNO is working with the Growth Fund project NXTGEN High Tech Equipment and the Smart Industry program on the implementation of 'digital connectors' for companies. This innovation takes place in 50 field labs: practical environments where large companies, SMEs and start-ups collaborate with mbo and hbo colleges, technical universities, knowledge institutions and local authorities. In addition, TNO focuses on training and education of employees, to learn and understand about 'digital connectors' and how to use them. At the Brainport Industries Campus, TNO ensures a successful knowledge spillover. Blankendaal: “There is now an mbo Smart Industry course on campus, and hbo students are building an Asset Administration Shell for robots in the Digital Factory.”
"Our country will benefit much more if the approximately 60,000 SMEs, accounting for 80 percent of our GNP, will increase their productivity through digitization."
Step out of your comfort zone
Working together and sharing knowledge is the way forward, especially for smaller companies, Sol knows: “Regions with a lot of cooperation within industrial ecosystems show the highest economic growth rates. For manufacturing companies that want to digitize, it’s important to step out of their comfort zone to stock up on knowledge, through their trade association or regional partnerships. At TNO, we can then help translate that knowledge to their company.” Blankendaal also sees collaboration as an important first step: “The world is changing too fast and the risks are too great to do it all on you own, especially for SMEs. Together you can gain momentum, and that is where TNO provides added value. I have worked intensively with TNO over the past 20 years, and they are really involved as a partner. I know my way around within TNO. Because we see that the digitization of SMEs is lagging behind, I am now also working with TNO on the European Digital Innovation hubs. With these hubs we take SMEs on the path of digitization.”
More information or partnership requests?
For questions regarding this subject please contact Jeroen Broekhuijsen.
Do you want to know more?
Download the paper Digital Sovereignty