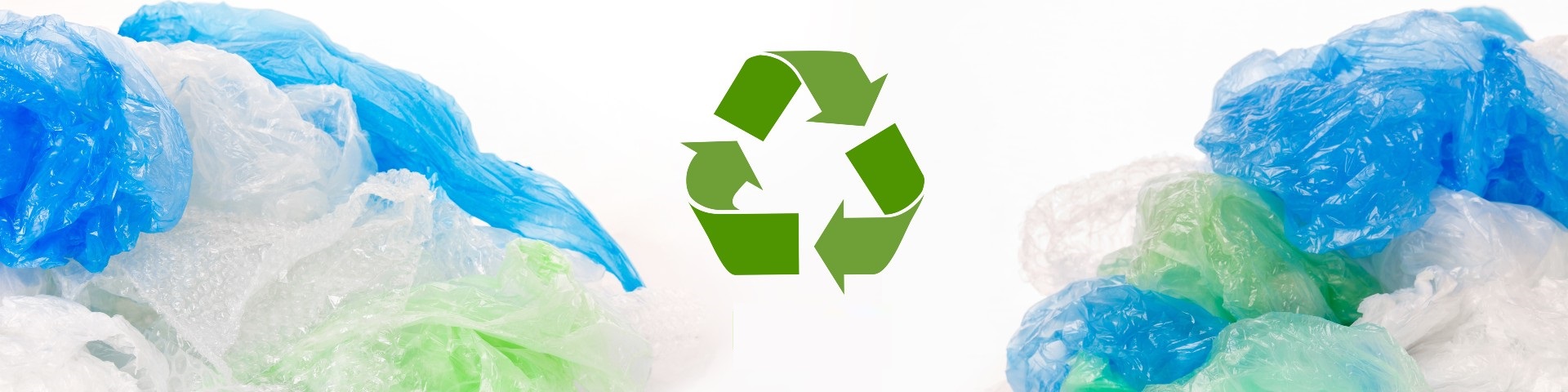
Recycling plastics through dissolution
In the Netherlands we currently recycle only 30% of the plastic waste of which half is used in high-value applications. However, the Netherlands wants to be 100% circular by 2050. To close the plastics chain, we need new recycling technologies, ideally ones that combine high efficiency with low energy consumption That is why TNO developed the Möbius dissolution technology – a solvent-based process that enables efficient and environmentally friendly recycling of polymers and additives.
The different ways of recycling plastic
What is the best, sustainable solution for waste management and recycling? Companies initially choose to recycle plastic into plastic, i.e. mechanically recycling.
But what if mechanical recycling is not possible because the quality of the plastic waste stream is inadequate? Or if the recycled plastic can only be used in low-value applications, also known as ‘downcycling’?
Other plastic recycling options include chemical recycling, which splits the various polymers into chemical components that companies can use to make new polymers. This process produces virgin-like plastic but consumes significant amounts of energy.
Between mechanical and chemical recycling there is physical recycling, which includes physical treatments such as dissolution.
What is dissolution?
Dissolution uses a solvent that will dissolve one polymer but not another, or the polymer but not the additives in the plastic. These polymers and additives can then be recovered and reused in an equivalent application.
The challenge is that the combination of plastics and additives always varies over the different waste streams. So in developing TNO Möbius dissolution technology, we are looking for new unique solvent-polymer combinations.
Recycling plastics into purified polymers
TNO Möbius dissolution technology is a physical recycling method developed to selectively dissolve certain polymers from a plastic mixture under superheated conditions. We then combine this dissolution technology with removal of impurities from the polymer solution. The purified polymer can then be recovered.
TNO Möbius technology involves the use of a low-boiling solvent at elevated temperature and pressure. This facilitates the dissolution of the polymers and allows recovery of the solvent.
Technology for purifying plastics
The viscosity of the polymer solution is low enough to allow for the use of conventional separation techniques such as filtration and adsorption. This enables us to remove the additives and impurities present in the plastics.
These additives include small particles such as pigments, plasticizers and flame retardants. The latter are added to plastic components such as electronic housing to prevent devices from smouldering or ignition.
After removing the impurities and additives, we are able to recover pure polymers that can be reused in plastics for all kinds of applications. TNO Möbius technology is also capable of simultaneously recovering the valuable additives.
The technology and equipment are named after the Möbius strip, which is a symbol of circularity. One advantage of this technology, compared to current state-of-the-art dissolution processes, is its potential for energy efficiency.
This is because the selected (low-boiling) solvent can be evaporated and recovered at a low temperature (typically below 120 °C). The use of a low-boiling solvent also enables efficient recovery of polymers with low solvent content.
Development and scaling up
In recent years, a small team of scientists, engineers, and technicians developed the TNO Möbius dissolution process. After first dissolving polymers in a small-batch setup, they scaled up the process from a plastic waste throughput of a few grams per batch to dozens of grams in a semi-batch process in the current TNO Möbius ‘Metis’ setup. Each stage of the scale-up not only increased waste throughput, but included additional functionalities, such as specific separation steps, and improved process continuity.
TNO Möbius Leto
The next stage is to further develop the technology and build an even more scaled-up and semi-continuous setup. Completion of this Möbius ‘Leto’ pilot plant, which will include recovery and recycling of the solvent, is planned for Q3 2024. This setup is designed to process polyolefins from packaging waste and ABS plastic from sources such as end-of-life vehicles.
We will use the TNO Möbius Leto pilot plant to determine key process parameters for further upscaling towards commercialization of the processing of these waste streams. It will also allow us to produce kilogram-scale polymer samples for our partners so they can test the properties of the recycled polymer for use in their applications.
Another goal is to expand the scope of the technology to recover clean polymers from other plastic waste streams, including materials such as discarded carpets, electronics, and construction waste.
Solvolysis
TNO is also extending their solvent based recycling to solvolysis to recycle those plastics that cannot be recycled with the dissolution technology. Solvolysis is crucial as it transforms previously non-recyclable plastics into valuable raw materials, such as strong fibres recovered from automotive composites. Within the R&D Hub, we are collaborating to further enhance this technology for more efficient recycling of thermoset composites.
Collaboration across the plastics value chain
So far, TNO Möbius technology has been developed and applied in national and European collaborative projects with research institutes and industrial partners, as well as in commercial projects for clients.
The larger projects often span the entire plastics value chain for end-of-life materials such as discarded electronics (PLAST2bCLEANED, Impres), automotive waste (ALMA, ABSoIEU) and (multilayer films) packaging (CIMPA, Syschemiq).
Collaboration with Braskem and ELIX Polymers
These projects then lead to collaborations with industry such as Braskem and ELIX Polymers.
We concluded a joint development agreement with Braskem to recycle polyolefins efficiently and environmentally friendly with use of the TNO Möbius Technology. Polyolefins are polymers that are build up from carbon and hydrogen only and can be processed into products such as plastic bags, packaging, film, pipes and fibres.
We also entered into a collaboration to recycle ABS polymers with ELIX Polymers, a leading European producer of ABS resins and derivatives.
ABS is a light but tough, impact-resistant polymer that is easy to injection mould. This polymer is used un durable products such as car bumpers and household appliances. Therefore, the ABS in waste streams is too degraded to be re-used in high-end products. TNO is further developing the TNO Möbius technology to rejuvenate the ABS and with this close the value chain.
Expertise in research for recycling technologies
TNO’s strength lies in the fact that many of these projects and collaborations leverage the knowledge and synergies of the various TNO expertise groups focused on areas such as:
- dissolution-based recycling
- characterization of polymer behavior
- mechanical recycling and redesign of plastic products
- chemical analysis of polymers
- systematic impact assessment of plastics value chains
- thermochemical recycling
- solvolysis
Are you a new partner who can benefit from this technology?
Get inspired
Early results show the potential of circular healthcare plastics


Biobased materials
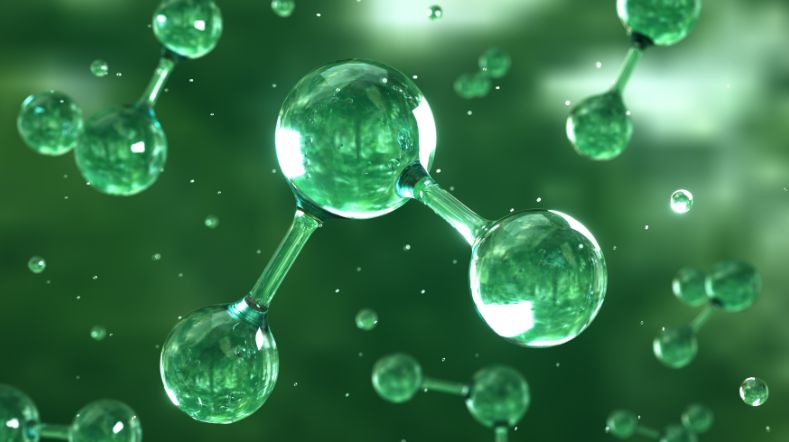
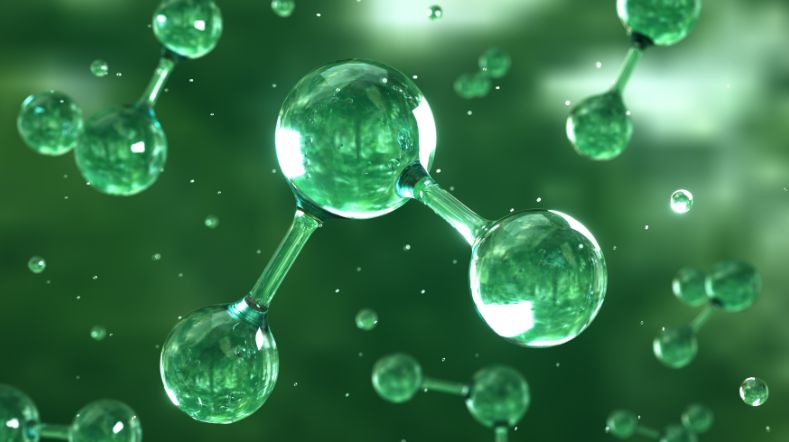
Enhanced solvolysis contributes to the future of composite recycling
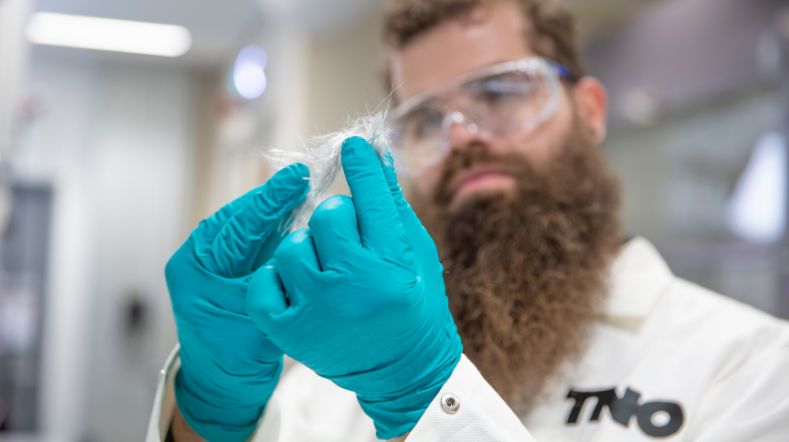
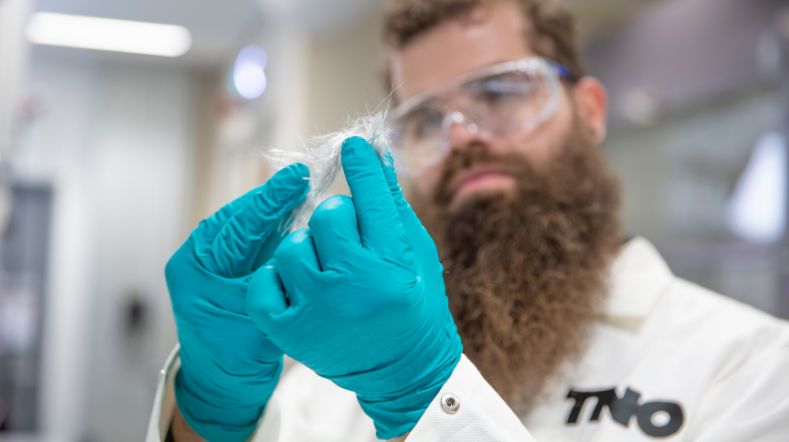
Collaboration for sustainability: better results through joint innovation
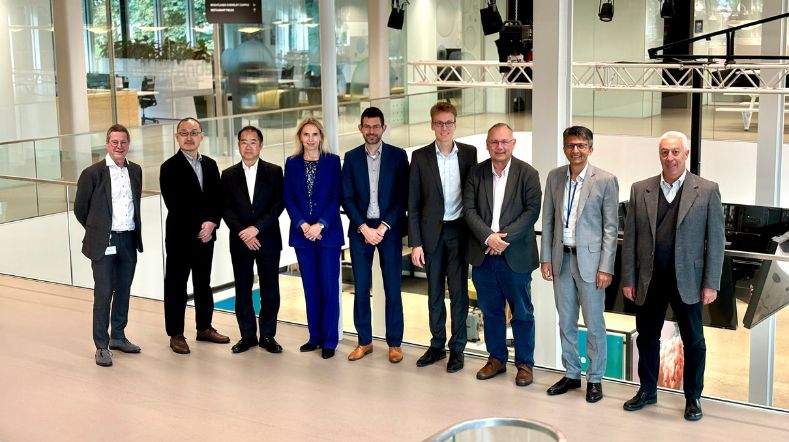
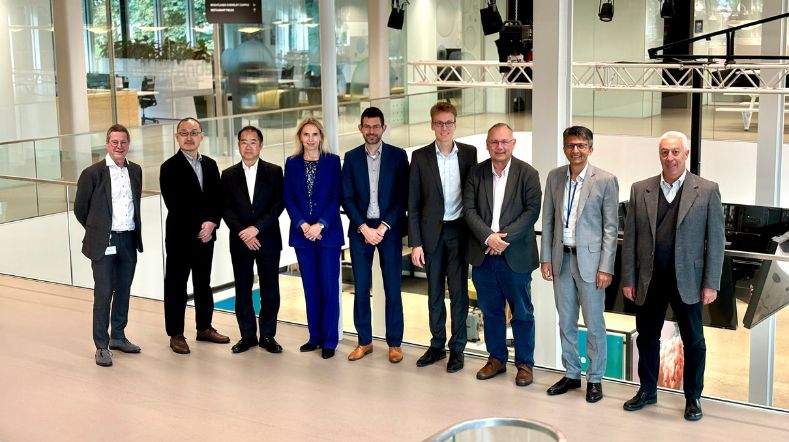