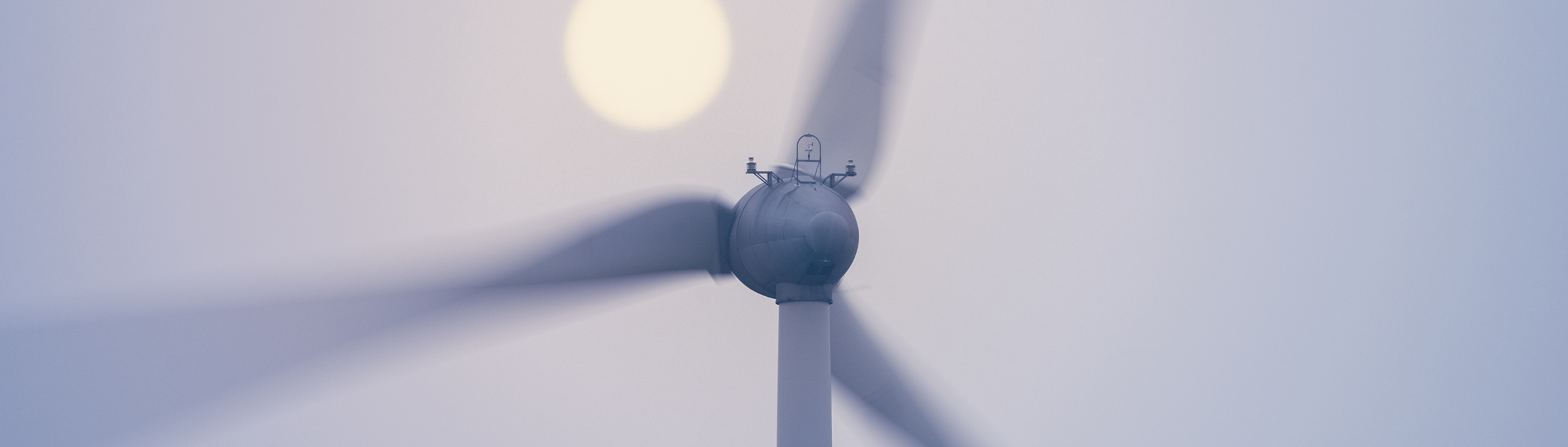
Windturbine met bladen van 145 meter: kostenreductie en meer efficiëntie
Als de trend zich doorzet, hebben windmolens in 2040 bladen van 145 meter. In het rapport ‘Future Blades’ onderzoekt TNO hoe deze bladen eruit kunnen zien, maar bovenal hoe ze getest en gecertificeerd moeten worden. Het fysiek testen, zoals nu gebeurt, is met bladen van een dergelijke lengte vrijwel onmogelijk.
Windmolens worden steeds groter en de grens lijkt nog lang niet bereikt. Rond 2040 zullen ze een vermogen van 27 Megawatt hebben, waar nu circa 15 Megawatt het maximum is. De turbine van de toekomst draait met bladen van 145 meter, circa 35 meter langer dan die van de grootste windmolens op dit moment.
“Met nog langere bladen wordt bij minder wind hetzelfde vermogen geleverd als de huidige generatie windturbines. En met hoge windsnelheden tot wel twee keer zoveel vermogen als nu”, stelt Noud Werter, scientist bij TNO. “Je kunt er dus nog grotere parken op zee mee bouwen of het aantal windmolens in een park verminderen. Dat scheelt aanzienlijk in productie-, plaatsings- en onderhoudskosten. Kostenreductie is een belangrijke reden om windturbines en bladlengte te blijven doorontwikkelen.”
Alle aspecten
In het rapport ‘Future Blades’ onderzoekt TNO alle aspecten van bladen van 145 meter (pdf): van ontwerp en constructie tot productie, testen en certificering. Welke stappen moeten worden gezet om zulke lange bladen mogelijk te maken? “Bij deze lengte zullen bladen bijvoorbeeld slanker moeten zijn dan nu, wat relatief tot minder gewicht en belasting van de boutverbindingen leidt”, zegt projectmanager bij TNO Michiel Hagenbeek.
“Maar het betekent ook dat het blad meer zal doorbuigen en dat heeft weer consequenties voor de materiaalkeuze en constructie.” Bladen van 145 meter leveren praktische problemen op bij het transport. TNO onderzoekt in het rapport wat nodig is om bladen in delen te produceren en pas op de eindlocatie samen te voegen. Daarbij is gekeken wat voor- en nadelen zijn van verschillende keuzes. Hagenbeek: “De tip van het blad zal slijten door regeninslag. Bij veel erosie zou je er bijvoorbeeld voor kunnen kiezen de tip na een aantal jaren te vervangen. Dit en andere scenario’s hebben we doorgerekend in het rapport.”
“Je kunt met deze bladen grotere parken op zee bouwen of het aantal windmolens in een park verminderen”
Inzet van 3D-printing
TNO voorziet dat de productie van bladen verder geautomatiseerd wordt. Noud Werter: “Hierdoor treden minder fouten in het productieproces op waardoor de robuustheid van de bladen op een hoger en constanter niveau komt. Het aanbrengen van lijm en het nabewerken van de bladen kan je bijvoorbeeld automatiseren.” Ook zou 3D-printing, een techniek die nu sterk in ontwikkeling is, op termijn kunnen worden toegepast.
Hagenbeek: “Als je zowel hars als vezel met dezelfde polymeer kan printen, vergroot je niet alleen de stijfheid van het blad, maar maak je ook recycling makkelijker. Je hebt immers maar met één materiaalsoort te maken.” 3D-printing maakt het mogelijk topologisch geoptimaliseerde constructies toe te passen. De vorm van het blad volgt dan de opgelegde belastingen, legt Hagenbeek uit. Het leidt tot een gewichtsbesparing en betere prestaties.
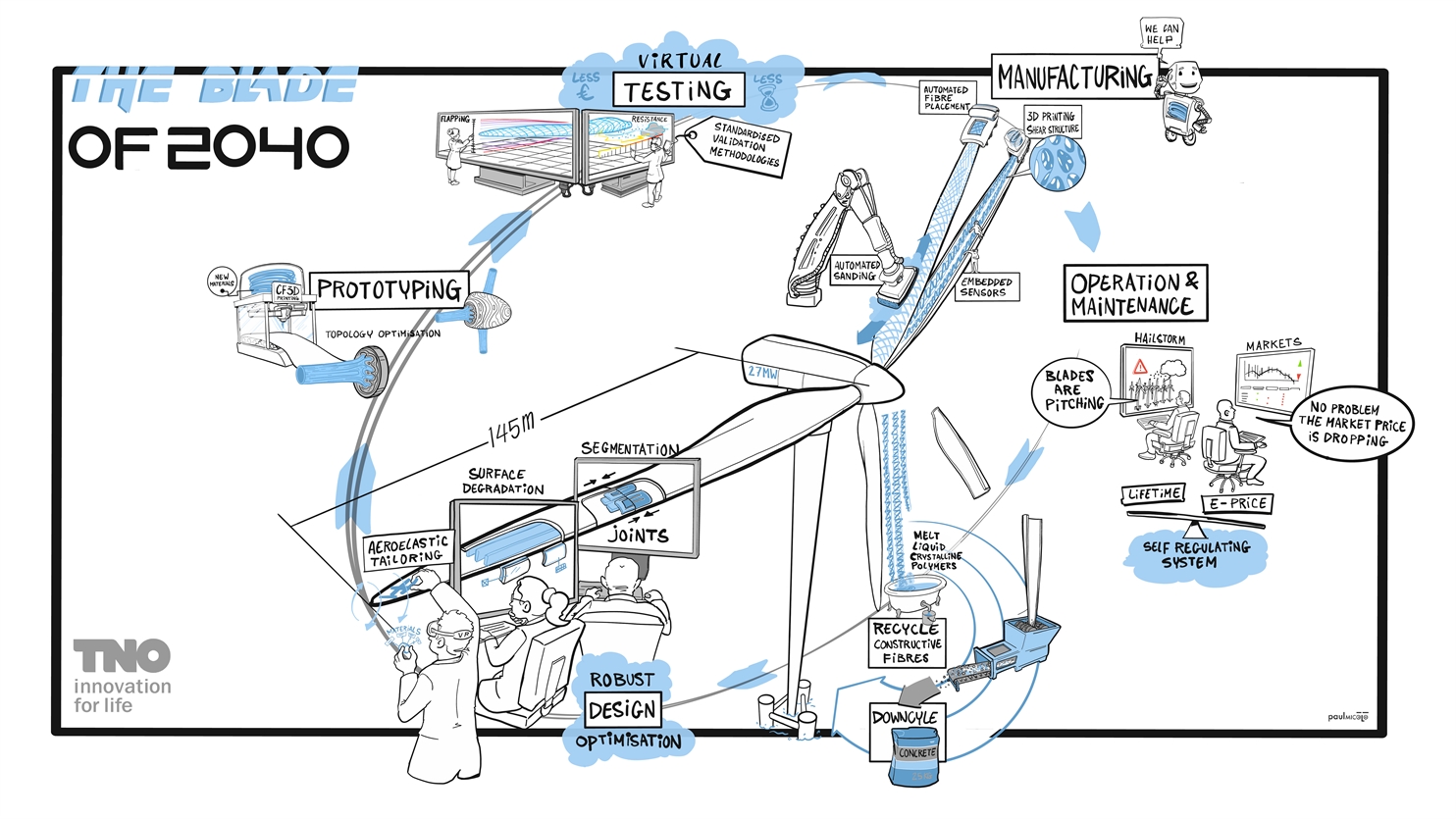
Sensoren voor continue monitoring
TNO heeft ook gekeken naar sensoren in de bladen. Die maken het mogelijk continu de status van de bladen te monitoren, zodat bijvoorbeeld duidelijk is wanneer onderhoud nodig is. Sensoren kunnen bladen ook laten reageren op windomstandigheden. Hagenbeek: “Bij hoge windsnelheden zou de sensor een signaal kunnen afgeven waardoor de turbine kan besluiten het blad te ontlasten. Zo verminder je slijtage, verleng je de levensduur en optimaliseer je het rendement.”
De uitdaging: testen en certificeren
Een van de uitdagingen in 2040 is om bladen van 145 meter te testen en te certificeren. Nu worden bladen fysiek getest op robuustheid en verwachte levensduur. Noud Werter: “Bij fysieke testen wordt het aantal rotaties dat een blad gedurende pakweg 30 jaar zal maken, gesimuleerd. Dat fysiek testen wordt al moeilijk als bladen, zoals nu, langer dan 100 meter zijn. Je hebt er gigantische testlocaties voor nodig en het testen duurt steeds langer. Bij bladen van 145 meter is het vrijwel onmogelijk om op de traditionele manier vermoeiingstesten uit te voeren. Zulke grote testlocaties zijn er gewoonweg niet en erg kostbaar om te bouwen. Bovendien duurt het nog langer om het aantal rotaties tijdens de volledige levensduur van een blad te simuleren.”
“Virtueel testen is ook kosteneffectiever, omdat je alleen de componenten versterkt die minder goed uit de test komen”
Virtueel testen
In het rapport ‘Future Blades’ gaat TNO in op het virtueel testen van windmolenbladen van 145 meter. Noud Werter: “Virtueel testen wil zeggen dat je variaties in de eigenschappen in kaart brengt. Je ontleedt het blad in zijn verschillende componenten – de materialen, de constructie, de verbindingen – en test die componenten afzonderlijk. Vervolgens wordt deze informatie geïntegreerd in een overkoepelend model, waardoor testen van het blad als geheel niet noodzakelijk is. Wij laten in het rapport zien – en dat weten we ook uit ander onderzoek – dat hierdoor een nog nauwkeuriger beeld ontstaat van de robuustheid van het totale blad en de verwachte levensduur. Het is ook kosteneffectiever, omdat je alleen de componenten versterkt die minder goed uit de virtuele test komen.”
Michiel Hagenbeek vult aan: “Een van de grote voordelen is dat uit de deeltesten verschillende waarden komen. Het computermodel laat daarmee de bandbreedte zien waarbinnen alle toekomstig geproduceerde bladen vallen. Virtueel testen zegt dus niet alleen iets over één windmolenblad – zoals bij de testen die momenteel plaatsvinden – maar over alle windmolenbladen die op dezelfde manier ontworpen, geconstrueerd en geproduceerd zijn. Dat maakt certificering gemakkelijker.”
Bladen van 145 meter zeker mogelijk
Virtueel testen lost het probleem op dat het fysiek testen van bladen van 145 meter praktisch vrijwel onmogelijk is. Maar het zorgt ook dat een nieuw type bladontwerp veel sneller en goedkoper naar de markt gebracht kan worden.
Werter en Hagenbeek: “De techniek moet nog een paar stappen maken. In ‘Future Blades’ laten we zien welke stappen dat volgens ons zijn. Wij denken dat het zeker mogelijk is om windmolenbladen te maken van 145 meter. Bovendien laten wij zien dat het virtueel testen tot betrouwbaardere bladontwerpen leidt en praktische problemen kan helpen oplossen. We werken hard aan het virtual testing-concept om het zo snel mogelijk te kunnen valideren.”
Neem contact met ons op
Laat je verder inspireren
Windenergie webinars
Switch naar het hybride energiesysteem
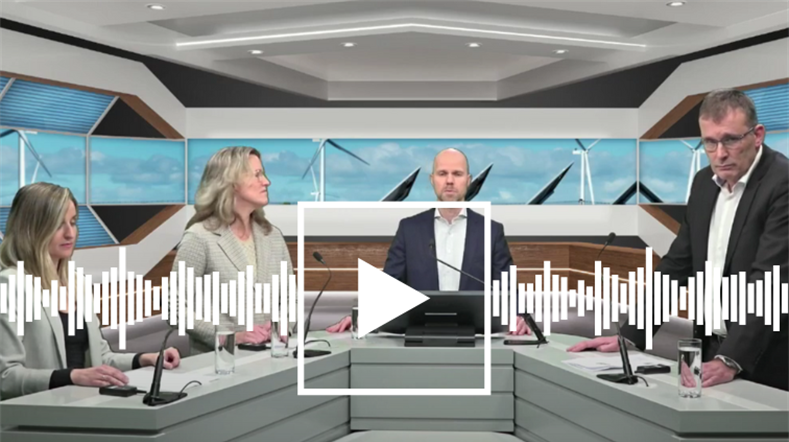
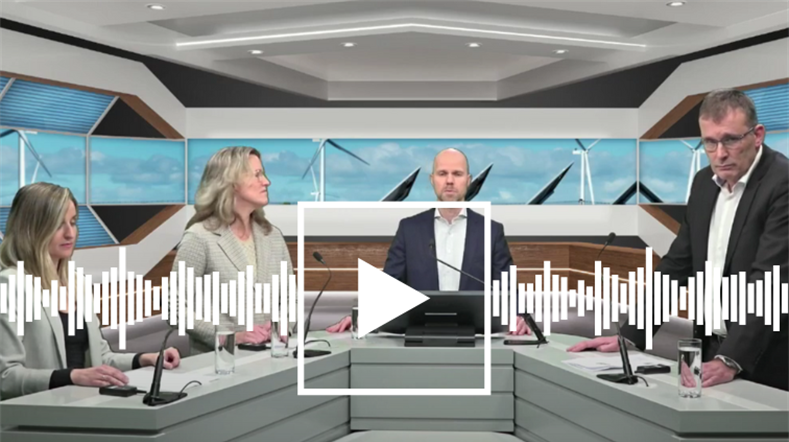
Wind op zee onder druk
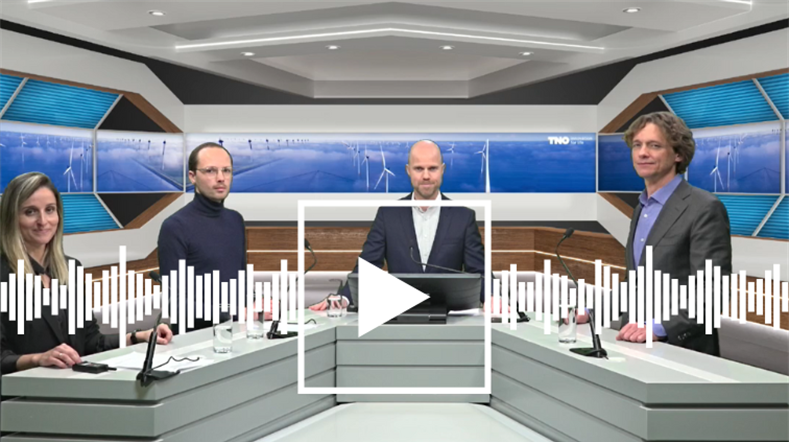
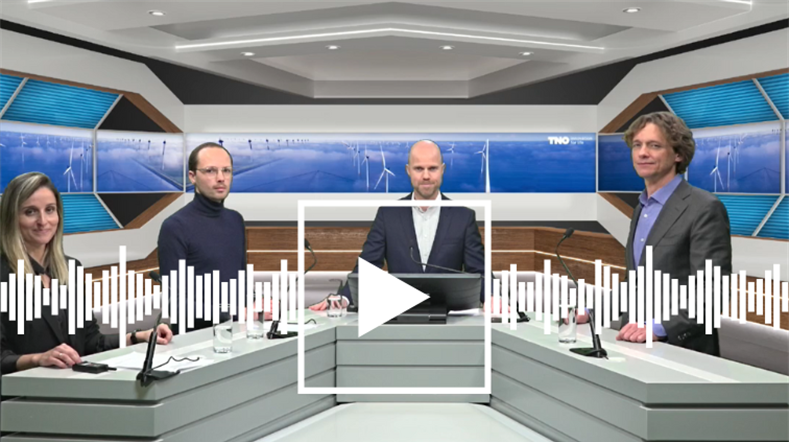