Verandert de wedloop tussen bescherming en gewicht van Defensievoertuigen?
Aan militaire voertuigen worden gezien hun functie en toepassing extreme eisen gesteld. Maar het beschermen van de inzittenden met steeds dikker en zwaarder materiaal loopt tegen de grenzen aan. Voor de bescherming voor de inzittenden van Defensievoertuigen wordt traditioneel gekozen voor gepantserd staal, maar voor de toekomst wordt ook gekeken naar andere materialen.
“Het ondersteunen van de krijgsmacht met kennis en innovatie is een van onze hoofdtaken”, vertelt Mark, medewerker bij Defensie en werkzaam op de afdeling Grondgebonden Wapensystemen. “In deze functie kijken we continu met welke nieuwe technologieën we onze wapensystemen kunnen verbeteren op punten als onder meer bescherming, mobiliteit en vuurkracht. Om een praktisch voorbeeld te noemen zou dit voor een militair voertuig een betere bepantsering kunnen betekenen, de mogelijkheid om verder en sneller te kunnen rijden en de capaciteit om een groter kanon mee te nemen."
"Als we genoemde verbeteringen voor een militair voertuig willen realiseren, komen we met de stalen constructies niet verder; we lopen eenvoudig tegen gewichtsproblemen aan. De voertuigen worden door de toevoeging van meer staal té zwaar om nog goed inzetbaar te zijn in het veld en mogen wettelijk gezien ook niet meer op de openbare weg rijden. We richten onze pijlen daarom op een ander soort materiaal dat lichter is van gewicht en in verschillende uitvoeringen al wordt ingezet voor veiligheidstoepassingen als kogelwerende vesten en deuren."
"De ontwikkeling van deze materialen heeft al jaren onze aandacht en we zijn nu zover dat we ze mogelijk kunnen inzetten voor het vervaardigen van delen van defensievoertuigen. In dit onderzoek, dat wordt uitgevoerd in Europees verband, is TNO een van de partijen waarmee we samenwerken.”
Welke alternatieven voor staal zijn inzetbaar voor Defensie?
TNO-experts Dennis van Veen en Lucas Amaral, werkzaam op de afdeling Platform Protection and Advanced Materials (PPAM) zijn beiden betrokken bij het onderzoek. “In ons project onderzoeken we mogelijkheden om met lichtgewicht composietmaterialen onderdelen te construeren voor een gepantserd militair voertuig met een gewicht van 10 tot 13 ton”, vertelt Van Veen, die al enkele jaren aan het onderzoek werkt. “Het uiteindelijke doel is om door het gewicht te verlagen, het operationeel vermogen te vergroten. De naam van het onderzoek is dan ook L-AMPV. Dit staat voor ‘Light weight constructions for Armoured Multi-Purpose Vehicles’.”
“Een composiet is een materiaal dat is opgebouwd uit verschillende type materialen”, legt van Veen verder uit. “Gecombineerd zorgen deze materialen voor eigenschappen die beter zijn dan die van de afzonderlijke bestanddelen. Vaak wordt met composiet lichtgewicht, vezelversterkt kunststof bedoeld, zoals materialen voor bijvoorbeeld racefietsen, maar in feite is versterkt beton ook een composiet. In het L-AMPV-project zoeken we naar een composiet met eigenschappen als hoge stijfheid, slagvastheid en taaiheid. Het moet licht van gewicht en tegelijk net zo sterk, zo niet sterker zijn dan gepantserd staal zodat het onze militairen beter kan beschermen in oorlogssituaties.
Welke fases zijn er tot nu toe doorlopen in L-AMPV?
“De eerste fase van het onderzoek was een haalbaarheidsstudie; we wilden vooraf weten of dit project een reële kans van slagen heeft, voor we er meer tijd en geld aan besteden. Het resultaat was positief en daarom is L-AMPV 2 opgezet. Het doel van deze tweede fase was te onderzoeken of het mogelijk is om van composiet voertuigonderdelen te maken die voldoen aan de eisen die de krijgsmacht hieraan stelt.”
“ In het samenwerkingsproject L-AMPV 2 richtten onderzoekteams uit verschillende Europese landen zich ieder op de mogelijkheden om van lichtgewicht composiet een onderdeel voor een militair voertuig te maken”, vervolgt Amaral.“ TNO heeft onderzoek gedaan naar het vervaardigen van een bodemplaat; de ‘underbelly’. De bodemplaat moet zo sterk zijn dat deze bescherming biedt tegen onder meer landmijnen in oorlogsgebieden, zoals we bijvoorbeeld in Afghanistan hebben gezien.”
“Het onderzoek hebben we stap-voor-stap opgebouwd. Met als uitgangspunt de kennis van de haalbaarheidsstudie hebben we eerst op kleine schaal verschillende composieten getest. Bepaalde combinaties elimineer je en met andere ga je verder. In elke stap maakten we eerst berekeningen en gingen daarna verder testen met steeds grotere en meer realistische elementen.”
“Uiteindelijk hebben we een volledige bodemplaat getest, met daarop een behuizing die een de reële afmeting, gewicht en dynamica van een gepantserd voertuig simuleert. De behuizing bevatte sensoren en camera’s om zoveel mogelijk te weten te komen over wat er binnenin het voertuig gebeurt als het over bijvoorbeeld een landmijn zou rijden. We zijn erin geslaagd een lichtgewicht bodemplaat te maken die in de geschetste situatie intact blijft. Er vindt wel wat vervorming plaats, maar de inzittenden zouden veilig zijn.”
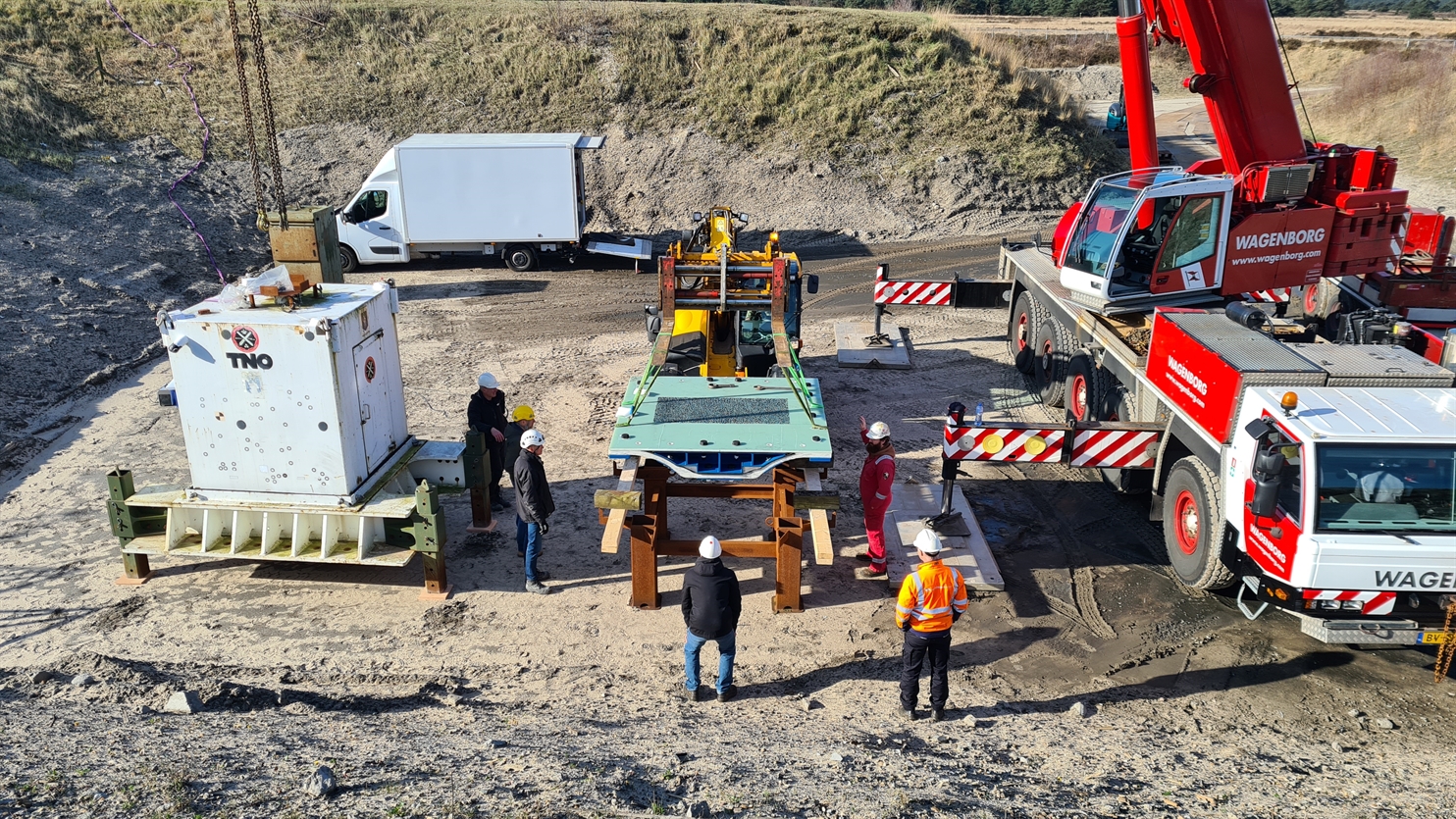
Wat zijn de kosten van constructies met composiet?
“Een onderzoek als dit is uiteraard behoorlijk kostbaar, daarom delen we de kosten met onze Europese partners”, legt Mark uit. “Maar als we kijken naar wat uiteindelijk de kosten van fabricage en gebruik zullen zijn in vergelijking met de huidige, met staal bepantserde voertuigen, is daar juist veel winst te behalen.
Fabricagekosten zullen onder meer lager zijn omdat lichtgewicht onderdelen gewoon gemakkelijker te hanteren zijn. Ook zijn verschillende vormen en ontwerpen veel eenvoudiger en dus voordeliger te realiseren omdat met composiet relatief gemakkelijk complexe vormen kunnen worden gemaakt die in staal niet mogelijk zouden zijn. Daarbij zijn de belangrijkste ruwe materialen goed lokaal beschikbaar. Dat betekent dat we voor de levering van deze grondstoffen minder kwetsbaar zijn in het geval verder oplopende geopolitieke spanningen. Tenslotte zullen de onderhouds- en vervangingskosten in de praktijk lager zijn omdat composiet simpelweg niet roest. Uiteraard is ook een flinke besparing op brandstofkosten mogelijk.”
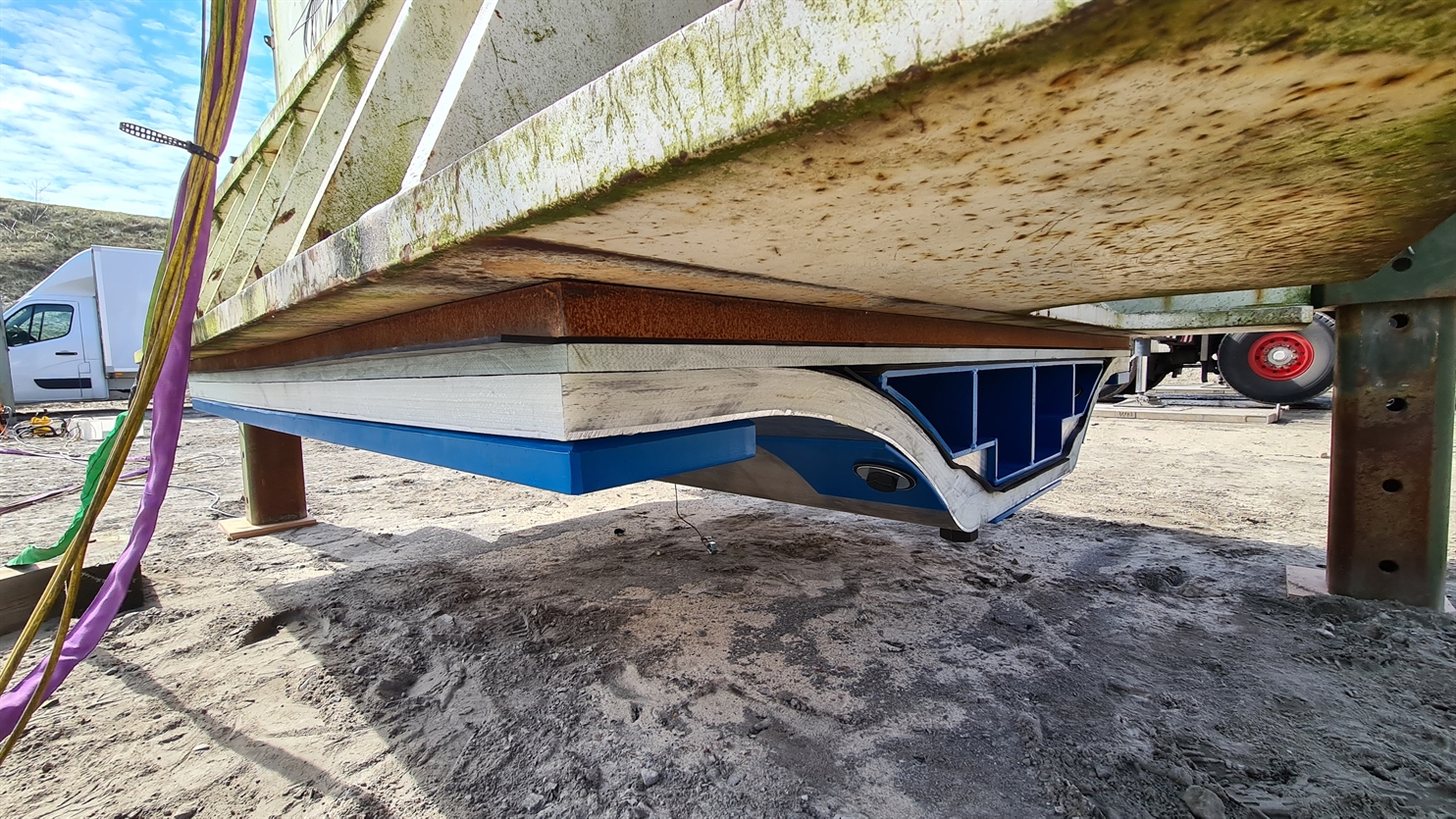
Doelen voor de toekomst
“Met de resultaten van ons onderzoek naar de bodemplaat en het onderzoek dat elders in Europa is gedaan naar deuren en luiken van composiet, hopen we snel te kunnen starten met L-AMPV 3”, neemt Amaral weer het woord. “De plannen voor deze fase staan nog in de steigers maar logischerwijs gaan we ons richten op onderzoek om de onderdelen in te zetten voor echte voertuigen in plaats van te werken met modellen."
"Daadwerkelijke toepassing in de (militaire) praktijk is en blijft het hogere doel van al het onderzoek dat we uitvoeren. Daarbij is het wel noodzakelijk dat alle partijen aan boord blijven, want we hebben de industrie hard nodig. Een investering in dit project levert bedrijven weer veel ‘know-how’ op voor het maken van composiet producten op het gebied van veiligheid, maar ook bijvoorbeeld de Europese jachtbouw en de auto-industrie kunnen ervan profiteren.”
Neem contact met ons op
Lachgas minstens uur aan te tonen in bloed en adem
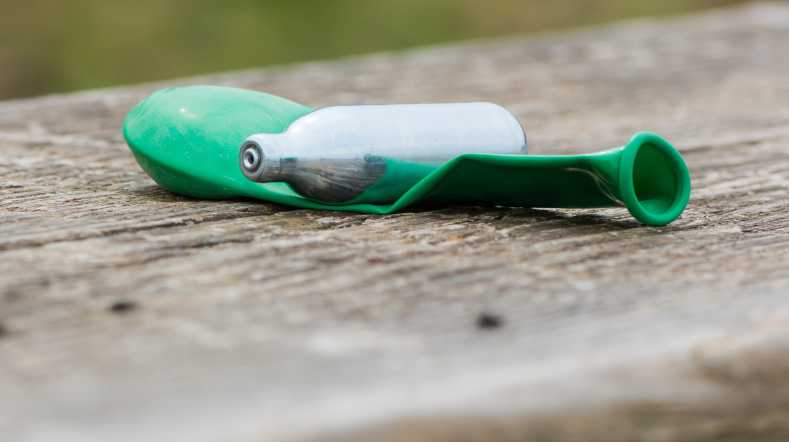
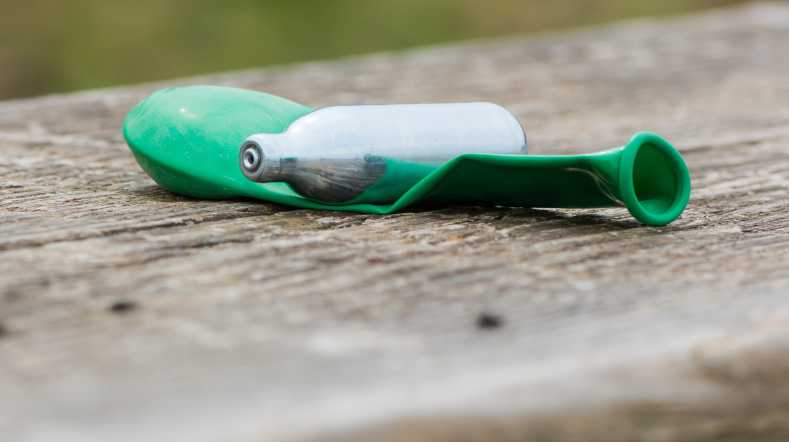
PITCCH event: Showcasing Open Innovation
Veilig de weg op met reflecterende coating
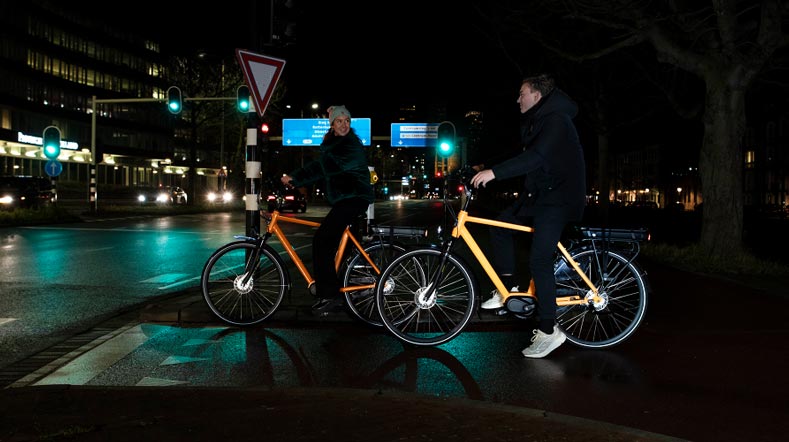
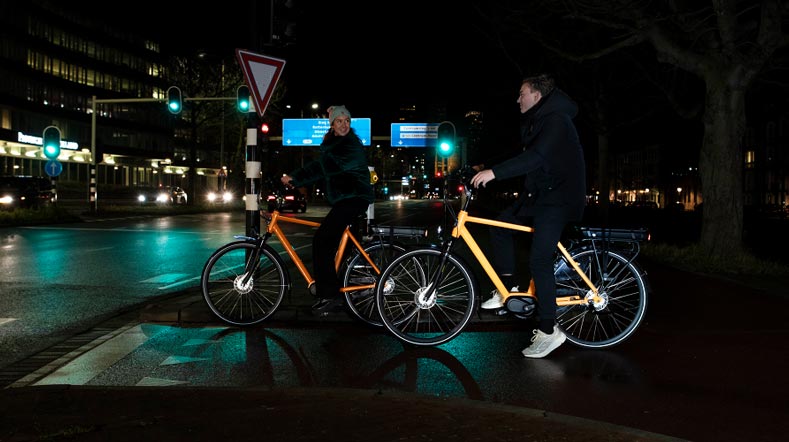