Maritime structures: efficiency and safety at sea
Efficiency and safety at sea. To achieve this, we’re committed to research into foundations, alternative fuels, joints, and ship vibrations. Through innovations in models, measuring, and sensors, we contribute to safe and reliable maritime structures, both new and existing, operating under extreme conditions.
Continuous monitoring of systems is becoming increasingly important. Ideally, companies want to know the status of a system at all times. Firstly, due to the increasing costs of inspection. Secondly, because ongoing optimisation is bringing us ever closer to the fatigue limits. In order to analyse data properly and be able to intervene in time, we need to make materials and large structures smarter.
Offshore foundations
How do you build a foundation at sea, such as for a wind turbine or floating solar panels? This requires up-to-date knowledge of noise during pile-driving, protection against corrosion, and the use of lighter materials, especially now that offshore wind turbines are becoming ever larger. We’re helping industry to push the boundaries with test set-ups and simulations.
We can solve many technical problems, but we have to do so in an economically responsible way. Our country is quite a forerunner in this respect. Nowhere in the world is a wind farm created without a Dutch party being involved. Because it’s such a big industry, we make sure to stay well-connected and to understand what’s going on.
Corrosion and service life determined with AI
Inspecting for corrosion is currently carried out by divers. But the question is what those divers need to assess. They can’t see much through the vegetation – and when is a situation really critical? It’s impossible to inspect all the 100+ wind turbines of a wind farm. But a wind farm may well contain that many turbines. This is neither practical nor profitable.
For this reason, we’re using new sensors and measuring techniques to work out how to do this in a smarter fashion. One of these new techniques is AI. Through smart analysis of the data that’s already available, we can calculate the behaviour of the structure in other places so accurately that no additional sensors are needed there.
Computer simulations and test set-ups
In our research, we combine computer simulations with realistic test set-ups. Testing is time-consuming and costly, so it’s important to carry out simulations. But you’ll still have to check regularly whether the calculations are correct. This definitely applies to newer materials, such as composites. A composite behaves very differently from steel, so we naturally include this in our modelling for industry.
Suitable for scaling up
Because assumptions are no longer correct, there’s a chance that joints such as steel to steel or steel to composite will break. That’s why we’re researching which joints are most suitable for scaling up. To start with, we analyse in a laboratory environment which parameters do or do not have an influence. We do this in close cooperation with industry, in order to find out what they’re up against and what else they experience.
Optical and acoustic sensors
Another of our special areas of expertise is the development of sensors that monitor the status of joints, such as an optical sensor integrated into the blade of a wind turbine. Sensors currently last 2 to 3 years. But we’re committed to developing optical, acoustic, and other sensors with a lifespan of 20 years. This is particularly desirable with the advent of digital twinning, with which we also monitor structures and joints virtually.
Mimicking reality
Even an M72 bolt can be pulled or vibrated apart. It’s a matter of using force. But instead of deliberately destroying something, we mimic reality to gain insight into the behaviour of a joint. Sometimes, we do this with sensors or joints we’ve developed ourselves. At other times, we test and quantify a company’s application. In this way, every piece of research is an interesting new challenge.
Get inspired
Increasing Wadden Islands’ sustainability with energy from water
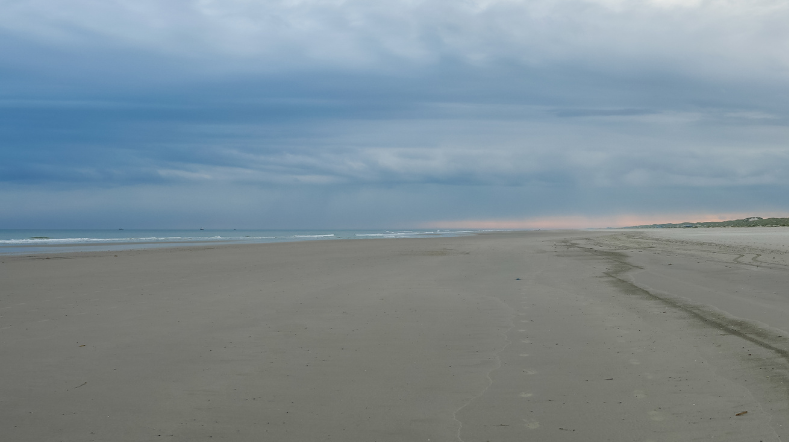
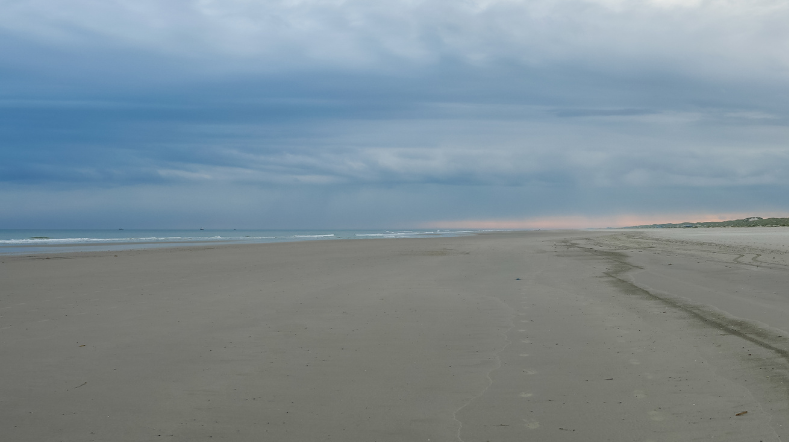
Advancing wind turbine blade reliability through innovative monitoring and digital twin technology
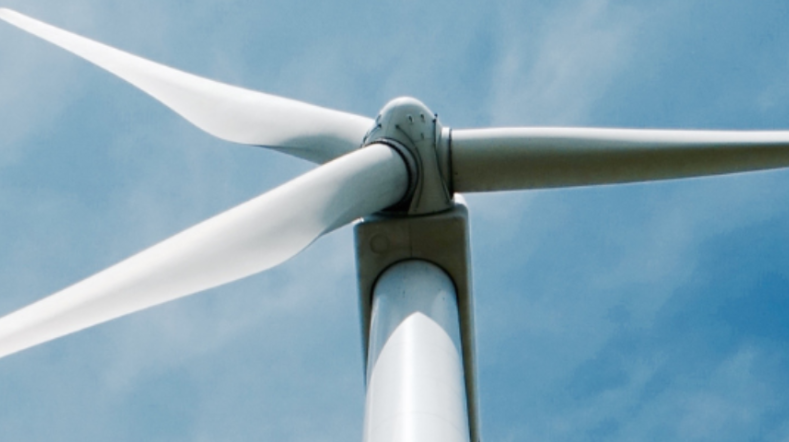
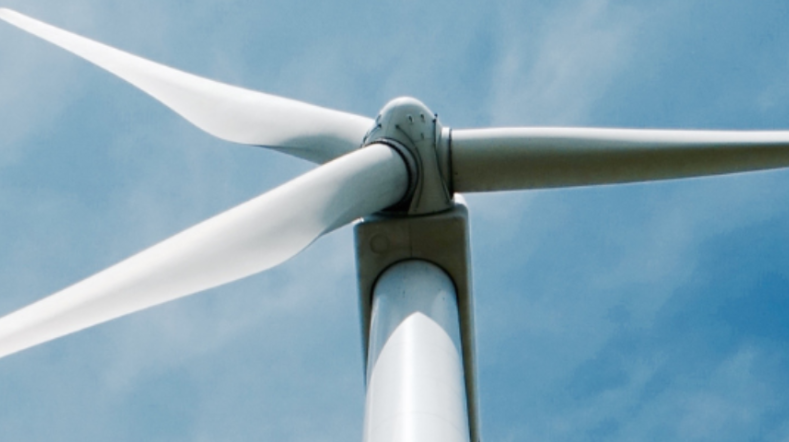